ABB Canada Launches Ergonomics Pilot Project to Help Improve Employee Health and Safety at Work
August 26, 2024
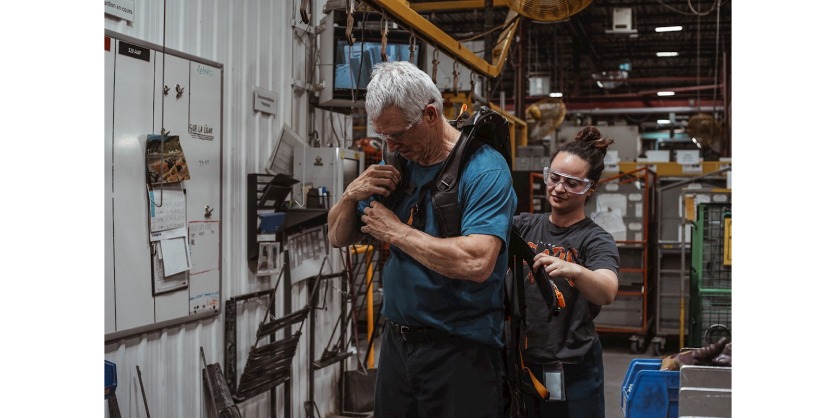
ABB Canada’s Health, Safety and Environment (HSE) team recently deployed an ergonomics pilot project at its Iberville, Quebec, facility aimed at improving overall employee well-being in the workplace. Exoskeletons are assistive technologies that mechanically support the body and reduce the stresses associated with physical work such as lifting heavy loads. Specifically, passive exoskeletons are wearable systems that use various mechanisms, including elastics or springs, to assist the user’s movements.
The idea was initiated by Geneviève Gagnon, MSc, an HSE consultant at ABB Canada. She specialized in ergonomics while completing her Master of Science at École Polytechnique de Montréal. Her knowledge has proved invaluable in helping improve the ergonomics of production team members in their daily tasks. “It’s important to stress that the use of the exoskeleton is only adopted when all other options have been tested,” she explained. “For example, first we adjust the employee’s workstation to place them closer to the task to reduce body strain, and if we don’t see an improvement, we bring in the exoskeleton.”
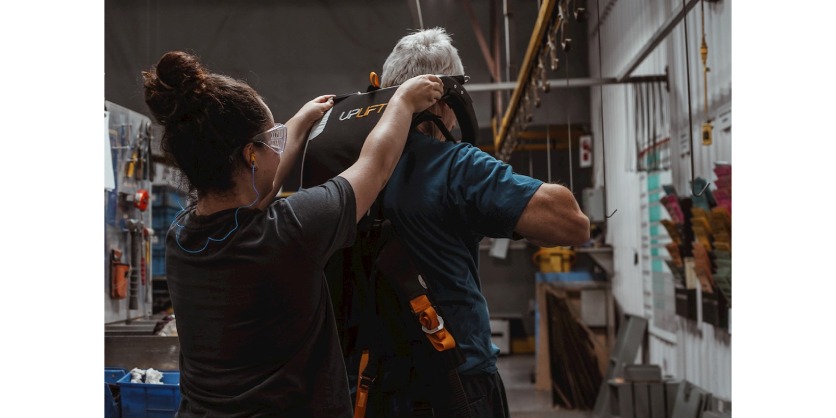
To implement this pilot program, the Iberville team worked with Mawashi Science & Technology, which is at the cutting edge of biomechanics and exoskeleton innovation. The Canadian company, based in St-Jean-sur-Richelieu, Quebec, specializes in new product development and research in the industrial, construction, defense and law enforcement sectors.
“Exoskeletons offer significant benefits for workers who perform physically demanding activities. Designed to augment physical capabilities, exoskeleton technology can go a long way to helping prevent short- and long-term musculoskeletal injuries. In addition to helping reduce risk of muscle, nerve, tendon, joint, cartilage, and spinal disc injuries, the use of the UPLIFT exoskeleton can help increase endurance up to 40%, increase operational efficiency, and help prolong one’s professional career,” explains Simon Pesant, Ph.D. Director, Customer Experience and General Administration at Mawashi.
“The ABB Installation Products team worked with Mawashi to gradually integrate the exoskeleton, enabling employees to adapt to this new equipment. “The exoskeleton technology is designed to augment physical capabilities, which can go a long way to preventing short- and long-term musculoskeletal injuries. The ABB Installation Products team worked with MawashiIt is recommended to gradually integrate the exoskeleton gradually, enabling as workers need employees to adapt to this new equipment. This process was important to assess the specific needs according to the task, including the type of movements involved, load characteristics, as well as the duration and frequency, to determine the appropriate exoskeleton configuration.”
“ABB is committed to placing Health, Safety and Environment at the heart of all its activities, including providing safe and healthy working conditions to help prevent work-related incidents and illnesses. With this pilot project, we wanted to help improve the comfort of our employees,” says Health Safety and Environment and Electrification Business Director, said Elaissi. “As part of their work, production employees are sometimes required to perform repetitive movements or lift heavy loads, which can lead to possible discomfort or injury in the workplace. By implementing this equipment, we hope to reduce discomfort and lighten the physical load of certain tasks for our employees.”
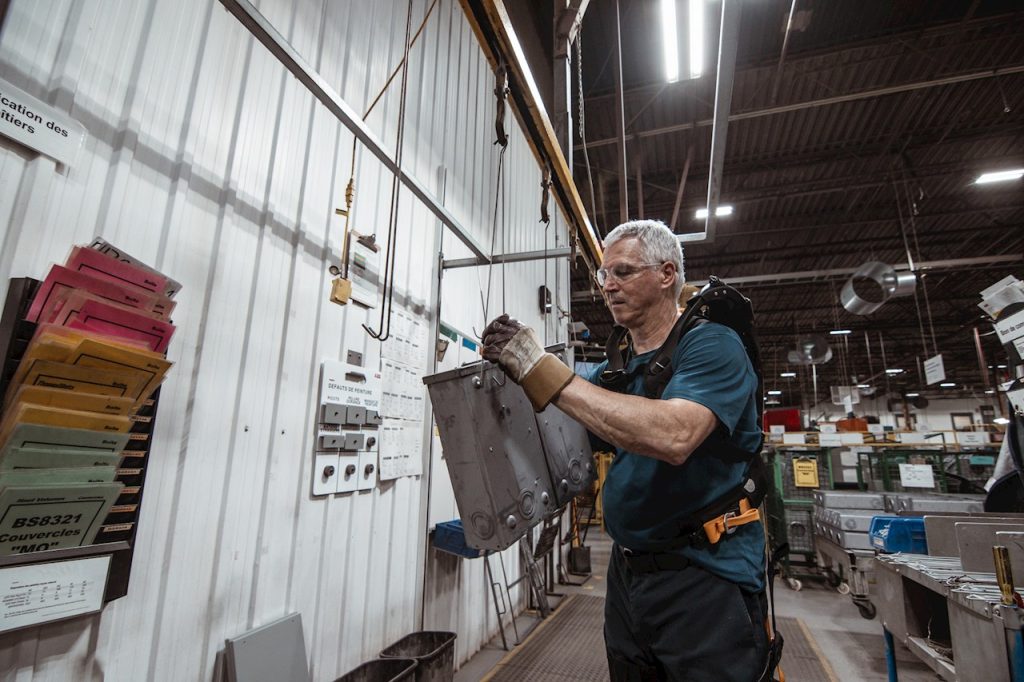
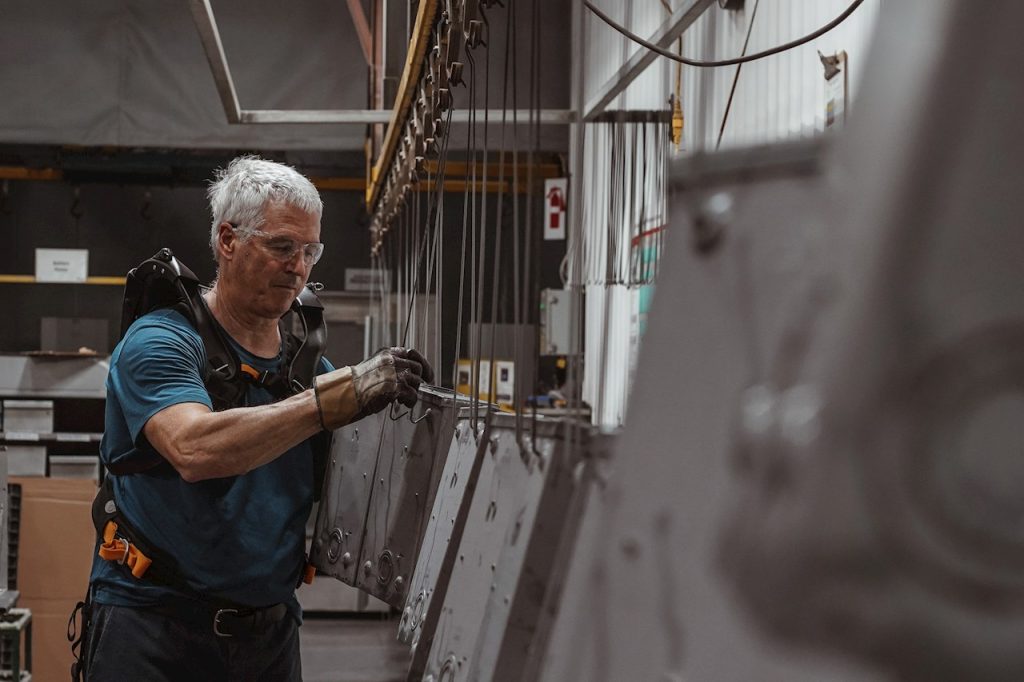
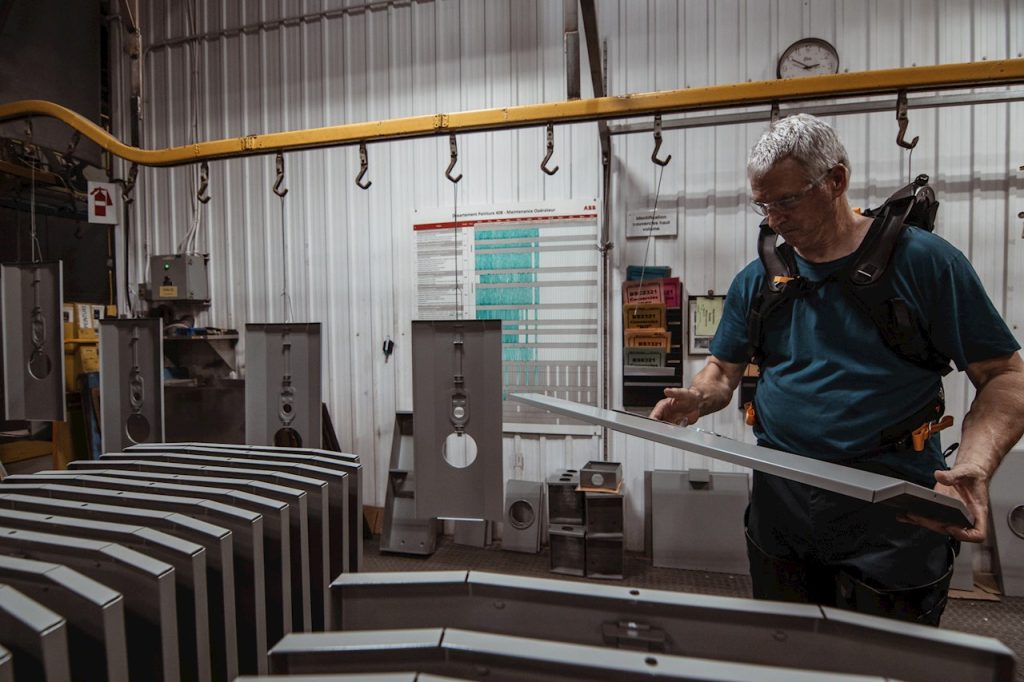
Based on pilot project learnings, the team will consider deploying exoskeleton usage on a broader basis in other ABB facilities. Once complete, the data will help to determine if there is greater need within the facility to implement such technology. Gradually, the technology will be incorporated into new employee training.
The Iberville facility currently has 176 employees and manufactures iconic brand products like Microlectric® meter sockets, T&B® cable tray systems and Superstrut® grounding plates and metal framing, among others. With an impressive production area of over 102,000 square feet, the facility produces over a thousand products each day including approximately millions of feet of metal strut annually, which are used across Canada in electrification.
Related Story
US $13 Million Investment by ABB to Expand Presence in Canada
ABB is investing US $13 million in its Installation Products Division Iberville manufacturing facility in Saint-Jean-sur-Richelieu, Quebec, to increase production capacity and establish a research & development facility at its global center of excellence for cable tray manufacturing. This will support rising global demand, especially in the data center segment, and is ABB’s second multimillion-dollar investment in a Canadian site in the last 12 months.