Digital Twins Boost Machine Development
The first Festo automation components get their digital representations
May 4, 2023
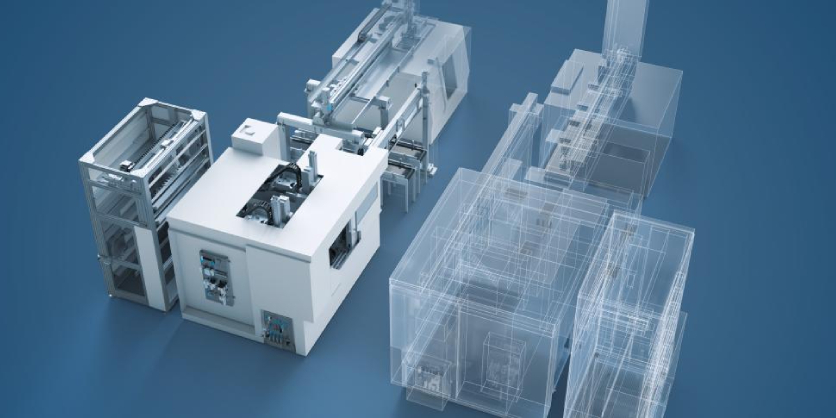
Faster time-to-market, more efficient engineering, more functionality and higher quality – these are the benefits of a digital twin for machine and system builders. Festo is working hard to equip its automation components with a digital twin – a digital representation in the form of administration shells. The company has joined forces with other German automation partners and the Industrial Digital Twin Association because standardisation is what machine and system builders expect. The advantages offered by digital twins will be demonstrated by a collaboratively built machine for a labelling application at the Siemens stand.
Digital twins can be used in many places in engineering, depending on the application. “Machine and system builders will demand digital twins so that they can develop their machines and systems faster and make fewer mistakes during the process,” explains Gerhard Borho, Member of the Management Board Digitalisation at Festo. Step by step, the principle of “digital first” continues to advance. Components and machines are developed virtually as much as possible before the hardware is produced; this also applies to testing and system integration. Similar developments can be seen in factory planning.
Gerhard Borho, Member of the Management Board Digitalisation at Festo
Shortening project timelines
Shorter development times require further simultaneous engineering by the machine builders. Digital twins therefore need to precisely replicate the capabilities of the components, if necessary down to the physical behaviour. This significantly shortens customers’ project timelines and increases productivity. Even before a machine developer has assembled the machine hardware, they can simulate it, test it and make adjustments. For example, they can design and program optimum, efficient handling systems using the virtual model. That is how errors can be detected and corrected at an early stage, which significantly contributes to efficient and stable operation later on.
Digital twins of automation components are much more than just 3D models that move virtually. They are digital representations that provide all kinds of information about the components, including a clear description of their capabilities, the documentation, the behaviour – e.g. simulation of their kinematics and kinetics – and the communication with them, including the role they play in the machine.
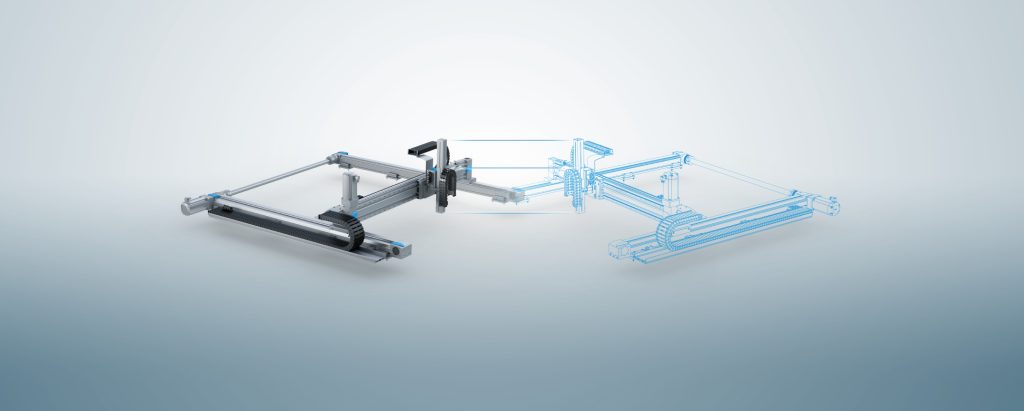
Focus on the entire life cycle
The Industry 4.0 machine architecture is based entirely on digital twins. Thanks to their standardised communication interfaces, they make life easier for our customers throughout virtually the entire lifecycle of a machine: from virtual commissioning and control of the machine to data acquisition and the resulting value-added services such as maintenance or diagnostics. Behavioural models of pneumatic functions were used to virtually commission the labelling machine mentioned earlier. The reduced need for searching in catalogues or on support portals or for preparing machine documentation provides further time savings.
Until now, there was a multitude of data for each automation component in different formats such as CAD, PDF or even paper manuals. Data management was therefore cumbersome and difficult to access throughout the entire lifecycle of an automation product. This lack of digital continuity also made it difficult to fully network all objects. Festo is therefore working on seamless and consistent communication technology such as OPC-UA. Ultimately, the administration shell is used as a central source of information to utilise digital twins throughout a component’s service life.
Digital twins make things easier right from the planning stage and the preparation of concrete proposals. “Intelligent algorithms can be used to design and configure optimum and, at the same time, energy-efficient components,” adds the Member of the Management Board Digitalisation at Festo.
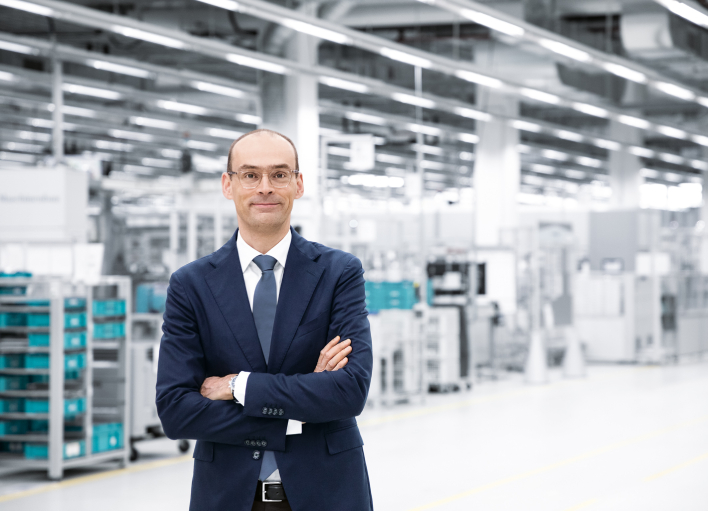
Advantages during commissioning
A virtual model allows the developer to test whether the slide can be moved, for example, and view the process data from the displacement encoder or the signal from the end position sensors. If the developer wants to create control sequences for the machine, they can easily be created using the components’ functions such as extend, rotate or grip.
Other value-added services can also be implemented on the basis of digital twins. The condition monitoring function generates a message when, for example, operating components are approaching the end of their service life. The machine’s digital twin could then automatically order spare parts. If at that point there are newer models for the components being replaced, the customer can use the virtual environment to first test how the new components interact before ordering them.
Condition monitoring can also be used in conjunction with the simulation models of the digital twins to create predictive maintenance plans. Furthermore, customers can use the digital twins to develop and test subsequent changes, optimisations or reconfigurations on the virtual model before these are implemented on the machine, which speeds up the process.
Together with other component suppliers, Festo has incorporated the digital twins of its electric and pneumatic automation products into a use case that gives machine and system builders the opportunity to discover the advantages of the digital twins live in the engineering tools from Siemens.
More Information
Related Story
The Festo Group
The Festo Group, among the world’s leading suppliers of automation technology and technical education, is deploying its products and services to meet the challenge of smart production for the future in the course of digitalisation. The company also relies on artificial intelligence and machine learning.
Established in 1925, the independent family-owned company based in Esslingen a.N., Germany, has been a driving force in automation for over 60 years and with its unique range of offers has become the world market leader in technical education. 300,000 customers worldwide in factory and process automation put their trust in the company’s pneumatic and electric drive solutions. In addition, Festo Didactic provides state-of-the-art training solutions for 56,000 industrial companies and educational institutions throughout the world. The Festo Group registered sales of €3.81 billion in the 2022 financial year and is represented at 250 locations throughout the world with a total of 20,800 employees. 7% of its annual turnover are invested in research and development.