Comau Will Significantly Accelerate the Testing and Verification of Automotive and Stationary Batteries
January 18, 2024
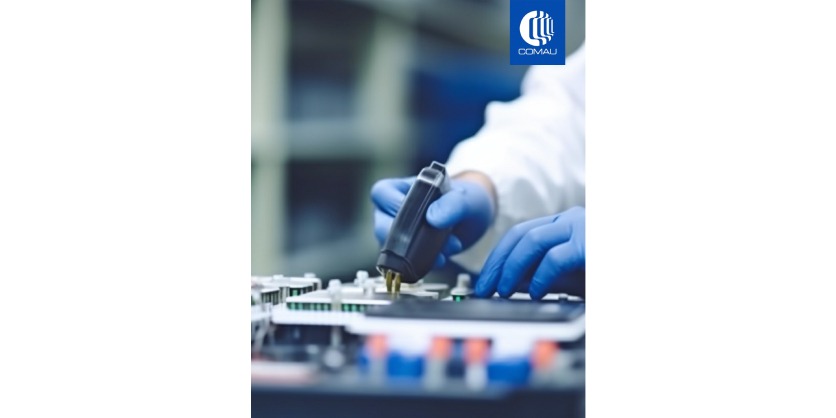
- Fastest is an EU project that aims to accelerate the development process of reliable, safer and more durable batteries
- Comau is tasked with designing the underlying digitalization and implementation strategy
- The final testing solution is expected to reduce the overall time and costs of battery production by at least 20% in addition to significantly reducing the need for experimental testing
Comau has committed to developing the digitalization strategy for a next-generation battery systems testing platform as part of a multi-country, multidisciplinary consortium in support of the FASTEST project. Under the scope of the project, Comau will leverage its longstanding expertise in digitalization, process simulation and electrification to significantly accelerate the testing and verification of automotive and stationary batteries. This is expected to reduce the overall time and costs of battery production by at least 20% in addition to decreasing the number of physical experiments and the subsequent reduction in materials costs.
Comau’s role is to both optimize the digitalization strategy and integrate its powerful In.Grid IoT platform to analyze the Digital Twin data. This will make it possible, in a second phase, to enable a complete information exchange with the virtual environment and further shorten time to market for battery manufacturers. Once the infrastructure has been validated, Comau will also help lead the industrialization pathway in close collaboration with the research centers, universities, industry players and cell manufacturers that are part of the consortium.
The FASTEST project is supported and promoted by the European Union within the framework of the Horizon Europe research and innovation program. Unlike current experimental testing methodologies that can take years to complete and are arguably expensive, the project’s intended use of a Digital Twin will allow customers to replace physical deployment with data-driven models, thus accelerating the testing and implementation process.
“This pioneering initiative aims to significantly lower the time and investment required for the development of batteries, cells and processes, confirming our efforts in innovative solutions for e-Mobility, as well as other sectors. The success of this project will help improve the competitiveness of the European battery industry within and beyond automotive, and is perfectly aligned with our development roadmap for current and next generation technologies,” says Stefania Ferrero, Comau Chief Marketing Officer.Stefania Ferrero, Comau Chief Marketing Officer
As part of Comau’s unwavering commitment to energy transformation solutions, the company is also actively involved in three of Europe’s top battery consortiums, having joined the European Battery Alliance (EBA), the Batteries European Partnership Association (BEPA) and the European Technology and Innovation Platform (ETIP) at the beginning of 2021. Similarly, Comau is a partner of Upcell – European Battery Manufacturing Alliance, an association that promotes the creation of an integrated European value chain for the development and production of electric batteries, and is also participating in numerous other projects regarding electrification as part of the HORIZON 2020 and HORIZON EUROPE programs.
More Information
Related Story
Comau Powers The Efficient Automation Production Of Next-Generation Electric Drive Systems For NIO
Comau has implemented a high-performance turnkey solution to automate manufacturing of NIO’s next-generation electric drive systems. The multi-faceted project also ensures fast and reliable co-line production for the electric vehicle manufacturer’s third-gen induction and permanent magnet motors, both of which are integral parts of its proprietary electric drive systems (EDS). The comprehensive solution includes primary lines such as e-motor assembly lines, gearbox manufacturing and inverter assembly lines, as well as EOL (End of Line) testing processes. It is designed to support a large-scale annual production capacity of 1 million units, to be used within NIO’s electric sedans, coupes and SUVs, as well as select models of its sub-brand ALPS.