Automated Welding System Nearly Triples Speed of Production: LJ Welding Automation
November 2, 2023
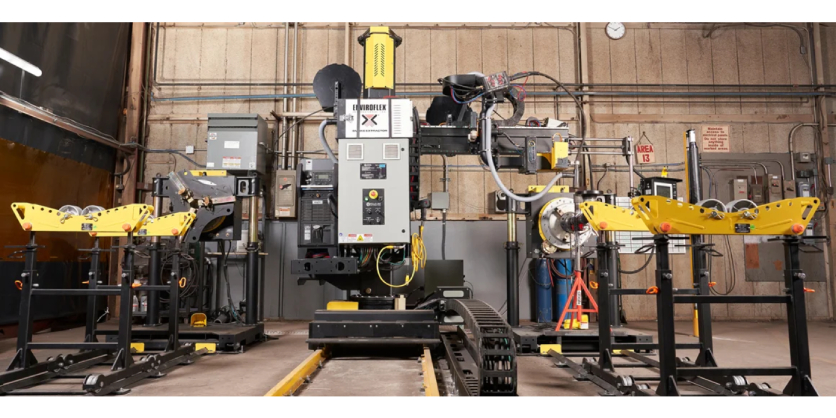
Modular engineering with TwinCAT for a pipe welding system for boiler room solutions
Pipe Titan is the latest robotic welding system from LJ Welding Automation. The integrated PC-based control technology from Beckhoff facilitated the implementation of a modular system architecture, offering a lot of flexibility for changing production processes in fully or semi-automatic operation. For one manufacturer of boiler room systems, Cleaver-Brooks, implementing this system increased throughput, quality and safety.
Dean Jacobs, Principal Automation Engineer at LJ Welding Automation based in Edmonton, Alberta, can describe the world of welding equipment in two words: bolt-on. “People bolt on this subsystem here, bolt on that one there,” says Jacobs,. “Soon, your welding cell has seven control panels and needs a massive power bar to feed them all.” The bolt-on approach was born of necessity. However, as technologies advance and equipment end users demand more modular solutions, the design and maintenance of such systems has become unsustainable.
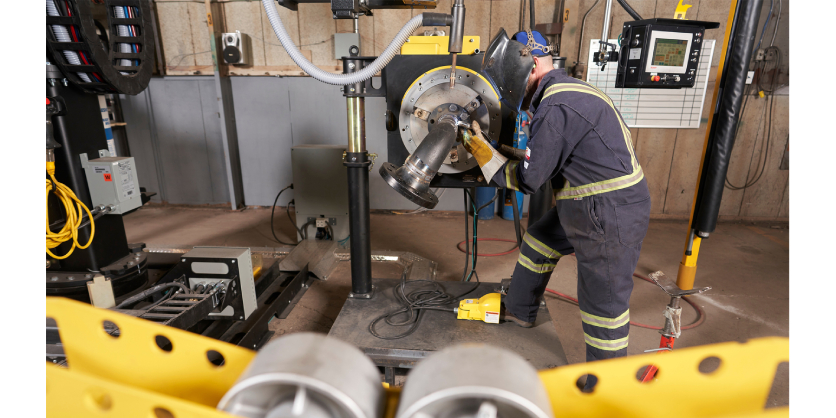
LJ Welding, however, recognized early on that an integrated approach not only provides a cleaner look, but also a key differentiator in the marketplace. The company provides wide-ranging solutions for welding, specializing in submerged-arc welding manipulators. With customers in more than 50 countries, it serves the most diverse industries.
VP of Product Development Tim Robinson says: “Over the last 17 years, we have expanded rapidly, and now we have hundreds of products as well as many custom, application-specific solutions. We can also tie together multiple pieces of equipment and provide complete turnkey plant design.”
VP of Product Development Tim Robinson
With the new Pipe Titan pipe welding system, LJ Welding offers such a complete processing center. The system is optimized for 2- to 24-inch-diameter pipes. One of the first Pipe Titan systems needed to deliver high-performance pipe welding at the Cleaver-Brooks facility in Stratford, Ontario. EtherCAT and PC-based control technologies from Beckhoff helped consolidate functionality into a centralized control architecture and provide a flexible, fully integrated solution.
Welding is a core competency in boiler manufacturing
Cleaver-Brooks is a global provider of efficient boiler room solutions, with a focus on reducing energy usage, cost and environmental impact. The pioneer of packaged firetube and watertube boilers stands alone in offering an entirely integrated boiler room solution for applications of any size. Cleaver-Brooks had several requirements for Pipe Titan, including reducing costs, improving quality, increasing productivity and enhancing safety, according to Corporate Welding Specialist Joel McLeod.
“Welding is a core competency at Cleaver-Brooks that helps ensure the structural integrity and reliability of our boiler room products and systems,” Joel McLeod explains. “We use a variety of welding processes throughout production to assemble and join various metal components in order to create sturdy and leak-proof boiler systems.”
Corporate Welding Specialist Joel McLeod
The LJ Welding Automation engineering team needed to maintain a clean design with highly deterministic control and system modularity. They also needed automation and networking technologies to support a high-end welder from EWM, according to Dean Jacobs. This welding equipment uses highly tailored programs to limit heat in the workpiece, thus minimizing warping and corrosion in pressure piping. The new welder had to work with the existing recipe management system to guarantee reliable and consistent results.
PC-based control supports platform approach
As he has done before, Dean Jacobs turned to Beckhoff to meet the project’s challenges. “When I started at LJ a decade ago, it was a blank slate in terms of automation platforms,” he says. “A major draw of PC-based control was – and continues to be – the ability to integrate third-party technologies on one platform.”
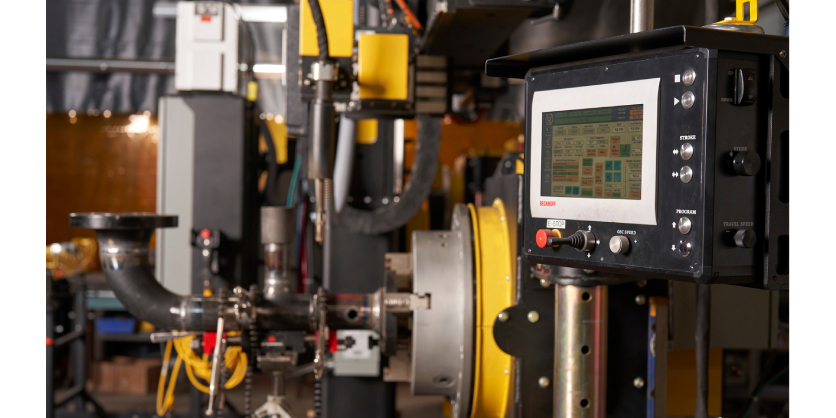
The Pipe Titan uses a CP6700 economy built-in Panel PC as the central machine controller, combining a 10.1-inch touchscreen for HMI with Intel Atom® processors in the control CPU in one device. The Pipe Titan has two separate positioners, and each has its own CX series embedded controller from Beckhoff. “The positioners have their own controller for simple one- or two-axis applications to rotate the pipe, along with functional safety and an HMI server. This way, they can function as independent machines if needed,” Dean Jacobs says. “You can unplug one positioner, take it to the other side of the plant, and use it. We use this modular architecture on all our larger machines.”
The modular TwinCAT 3 automation software enables this architecture as an end-to-end engineering and runtime environment. TwinCAT combines all functionality on a comprehensive platform for everything from PLC, HMI and motion control to IoT, analytics and even machine learning. TwinCAT supports programming in all IEC 61131-3 languages and their object-oriented extensions, custom or predefined function blocks, and computer science standards in Microsoft Visual Studio®.
LJ Welding leverages Structured Text, JavaScript for HMI development and other languages as necessary. TwinCAT helps the engineering team consolidate to a single tool chain to avoid switching between development environments. It also provides them with advanced source control options, as Benjamin Vandenberg, Automation Engineering EIT, explains.
EtherCAT brings together speed, flexibility and safety
The EtherCAT real-time Ethernet technology’s flexibility and scalability proved instrumental to the integrated yet modular design. EtherCAT enables free selection of topology, and hot connect capabilities. The Pipe Titan has multiple E-stops across its modules, which communicate via TwinSAFE, the integrated functional safety solution from Beckhoff.
As such, it supports modular machine designs without any hardwired safety controllers to physically adjust, Benjamin Vandenberg explains: “We essentially have three independent safety systems running, each one with an EL6910 TwinSAFE Logic Terminal. They communicate to each other using Safety over EtherCAT (FSoE), and we can simply turn those connections on and off in software using TwinSAFE features. We can add or remove different pieces of equipment as necessary to make it a more adaptable and scalable system.”
LJ Welding also relies on the vast number of available EtherCAT I/O terminals. The EL7211 and EL7221 servomotor terminals provide a compact motion interface to the AM8100 series servomotors. The EL3255 5-channel potentiometer modules ensure accurate speeds on the positioners when controlled by a hand pendant, variable-speed foot pedal, etc. EtherCAT-compliant third-party devices, such as a VFD on the Pipe Titan, work seamlessly with the EtherCAT controllers from Beckhoff.
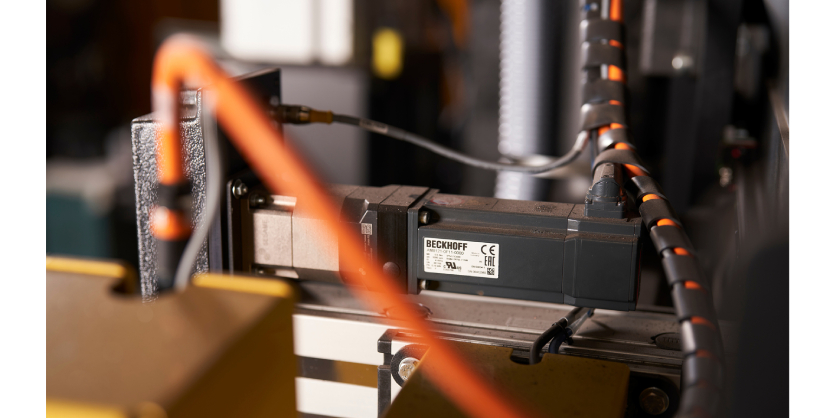
EtherCAT also supports connection to more than 30 communication protocols with the simple addition of an I/O module acting as a gateway. This promotes greater flexibility in component selection and avoids the poor integration of bolt-on scenarios. “On the Pipe Titan, the EL6224 IO-Link master terminal was particularly useful for connecting a laser displacement sensor, and we’ve used it in many other applications,” Dean Jacobs says.
Welding system delivers impressive results
By leveraging PC-based automation from Beckhoff, the team at LJ Welding implemented a system that surpassed the requirements of Cleaver-Brooks. The Pipe Titan led to impressive performance increases, according to McLeod. Cleaver-Brooks reduced arc time by 63% on average, which is nearly three times faster. The system also led to a 90% reduction in weld clean up time, 10% reduction in rework and 39% reduction in filler metal spend.
“The Pipe Titan welding system allows us to perform tasks faster and more efficiently than manual labor, leading to increased productivity and capacity. It reduces errors and inconsistencies, resulting in higher quality output,” Joel McLeod says. “Being mechanized, it can be programmed to perform a variety of tasks and can be easily reconfigured to meet our changing production demands. The Pipe Titan welding system helps reduce the risk of workplace accidents and injuries associated with manual labor, thereby improving employee safety.”
TwinCAT accelerated development, and the built-in software oscilloscope, TwinCAT Scope, enhanced tuning of the machine. Using the IPC Security Guideline from Beckhoff, LJ Welding can safely remote into customer machines for maintenance or troubleshooting. But the team isn’t stopping there.
The next phase for the Pipe Titan and other machines is higher-level connectivity for analytics and continuous improvement. Fortunately, for Dean Jacobs, this is another area where the Beckhoff technology is not bolt-on, but can be expanded flexibly. Standard analytics algorithms, no-code dashboards, secure connectivity via OPC UA and more are all built into TwinCAT.
More Information
Related Story
Beckhoff to Showcase Cabinetless Machine Control, Adaptive Automation, and New Vision at ADM Toronto 2023
At Advanced Design & Manufacturing Expo (ADM) Toronto 2023, Beckhoff will showcase Canadian market leaders in packaging, food and beverage processing, pharma and beyond how to automate what’s next. Visitors to Beckhoff booth #1205 will discover many revolutionary solutions in intelligent motion control and mechatronics as well as a wide range of Industrial PC (IPC), EtherCAT I/O, drive technology, vision, and more.