Five Considerations For Mobile Robot Safety
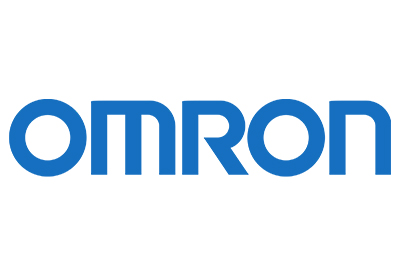
September 30, 2021
Autonomous mobile robots, or AMRs, can be a game-changing technology for manufacturers in all industries. They self-navigate through dynamic environments and transport payloads between workstations without requiring any permanent facility modifications, so they’re excellent for companies seeking to harness a flexible manufacturing paradigm.
Even though AMRs are quite easy to implement, it’s still important to take safety considerations into account and abide by best practices. Let’s take a look at several ways you can ensure the highest level of safety and efficiency when operating your mobile robot system.
Consideration #1: Emergency planning and evacuation
Any organization must prepare for emergency situations well in advance of the actual emergency occurring, and the primary goal is to get everyone out of the hazardous situation as quickly as possible. Mobile robots can complicate this somewhat, since they might still be operating while people are trying to evacuate.
There’s generally no reason to get the AMRs themselves out of your facility. However, they must allow a clear path for humans to reach the exit doors. Make sure that your external alarm system ties in with each robot’s internal messaging system so that they’ll respond by getting out of the way.
Consideration #2: Payload capacity and stability
Incorrect payload positioning could still make a robot tip over if positioned incorrectly, causing it to become an unproductive tripping hazard. Be sure to consider payload stability as it results from the loaded AMR’s center of gravity, and never exceed the unit’s capacity.
Mobile robot payloads go on the top of the unit, so a fully loaded AMR will have a higher center of gravity than an empty one. The goal is to have the weight be positioned as close as possible to the robot’s center.
Consideration #3: Obstacle detection and stopping
Stable stopping depends on a robot’s center of gravity, so a fully loaded AMR will need more time to stop from a given speed. Laser-based area scanners and other sensors help the robot notice obstacles in its path while there’s still plenty of time to stop smoothly.
Manufacturers can also set up zones that allow different speeds for different situations. Stopping distances can be calculated based on how much time a robot needs to stop at its current speed upon receiving a stop signal. You can program zone sets into the AMR area scanners to react to unexpected obstacles depending on level of severity.
Consideration #4: The nature of the surrounding environment
The surface a mobile robot travels upon can have a large impact on its balance and ability to stop safely. Angle of incline and decline, for instance, should be defined by the robot manufacturer, so be sure to not exceed this specification. Surface irregularity, like potholes and clutter, can also be hazards.
Aside from the possibility of an AMR tipping over and spilling its load, a less-than-ideal surface can also make it lose track of its location. If the robot is spinning its wheels inside a pothole, it might think that it’s moving closer to its destination when it isn’t. Since productivity depends on the robot knowing exactly where it’s located, this is a problem.
Consideration #5: Interaction with other machines
In addition to people, AMRs must communicate with other equipment, such as when they need to load or unload parts from a machine. Typically, the machine or the system will send a response to the network, which in this case would be a so-called “fleet manager” that serves as the master planner of the mobile robot system.
A fixed machine can send a signal to the enterprise system to say that it wants a robot to pick up a part. The machine then gets an estimate of when the robot will come. As the AMR approaches the machine, there comes a point where it needs to mute its area scanner, so it’s a good idea to have it reduce its approach speed in case a person gets in the way.