Everything You Need to Know About Pneumatic Systems
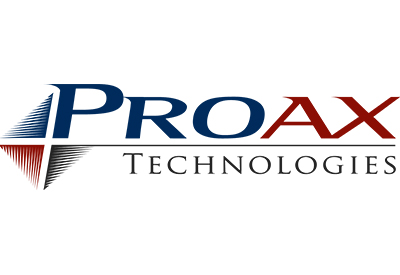
January 20, 2021
By Kevin Nguyen, Marketing & Communications, Proax Technologies
What are Pneumatics?
In its simplest form a pneumatic system uses compressed air to complete work. It starts with a compressed air source which is most often a compressor. A typical compressor will convert electrical energy to potential energy in the form of compressed air. It is this potential energy that is stored and distributed through the air lines for a variety of purposes.
One of the most common examples of a pneumatic actuator is the simple air cylinder. In a cylinder as pressurized air forced into one side of the cylinder, it pushes onto the piston. With the opposite side open to the atmosphere, there is a force imbalance across the piston. This imbalance creates motion. It is this force imbalance and action that is used to do work.
5 Benefits of Using Pneumatics
- Reliable/Low Maintenance – A properly designed pneumatic system supplied with clean, dry air is exceptionally safe and requires next to no maintenance. Components are rated for tens of millions of cycles, and the majority of modern equipment no longer needs lubrication.
- Simple – Pneumatic systems are relatively simple. Circuits are base on logic, and their outputs are typically linear or rotary motion.
- Ability to stall – Great for pressing and clamping applications. Pneumatics can supply a constant force indefinitely without the worry of burning out motors or drives.
- Self Cooling – Due to properties of expanding gases, pneumatic actuators cool themselves as they cycle back and forth. No need to worry about overheating.
- Inexpensive – Relative to their hydraulic and electrical counterparts, pneumatic components are much less expensive.
Basic Terminology
- Dew Point: Temperature at which moisture in the air condenses into water droplets
- Atmospheric Dew Point: Temperature at which moisture in the air condenses into water droplets at atmospheric air pressure
- Pressure Dew Point: Temperature at which moisture in the air condenses into water droplets at working air pressure
- Relative Humidity: Current moisture content in air vs theoretical maximum moisture content
- Compression Ratio: A measure of how much air is compressed
- Condensation: Formation of water droplets from water vapor
- CFM: Cubic Feet Per Minute
- L/min: Litres per minute
- SCFM: Standard cubic feet per minute
- Nl/min: Normal Litres per minute
- Standard Conditions:
-
- A generally accepted definition of standard consolidations by which values can be compared
- 7 psia, temp 68 decF, relative humidity 36%
- ANR
-
- Similar to Standard Conditions
- 1 bar, 20 deg C, 65% relative humidity
- Mist Separation/Coalescing: Removal of oil mist from air.
- NO vs NC Auto drains
-
- NO – Normally open, drains fluid when de-pressurized
- NC – Normally closed, drains fluid only when full
Main Parts of a Pneumatic System
- Compressor: A compressor compresses air up to the required pressure. It converts the mechanical energy of motors and engines to potential energy of compressed air. This is where it all begins. Compressors typically feed air into a tank where the air is allowed to cool, removing some of its moisture. Tanks also act as a storage for pneumatic energy and also eliminates pulses generated by piston compressors. Dryers are typically connected after the tank to remove the moisture created in the compression process.
- FRL – Filter, Regulator and Lubricator
- Filters remove particulate from the air, as small as 5 microns. Some also remove water droplets using centripetal force. Mist Separators or Coalescing filters can be added to remove oil from the air.
- Regulators control working pressure. Typical regulators have system air working against spring force across a diaphragm. As you adjust the handle on a regulator, you compress the spring more, requiring higher pressure to create a balance. When you need more force, this is what you adjust. Some electro-pneumatic regulators convert an electronic signal to pneumatic pressure settings. Regulators as the name imply create a stable pressure output. Most pneumatic systems run at 70-80 psi.
- Lubricators supply a steady stream of oil droplets into the airlines. Earlier generations of pneumatic components used to require this source of lubrication to work correctly. Today, most parts come from the factory don’t require lubricators
- Control Valves:
- Directional Control Valves are similar to electronic relays. They convert a small control signal to a larger signal used to move actuators back and forth, rotary actuators to spin CW or CCW or grippers to open or close.
- Flow Control Valves controls the amount of air flowing at a given point. These also include check valves, needle valves, shuttle valves, etc.
- Actuators: This is where the work gets done. An Actuator is a component which can undergo linear, rotary or reciprocating motion. Examples include round body and tie rod cylinders, rodless cylinders, rotary actuators, grippers etc.
- Pneumatic tube and connectors: Hollow pipes made of a variety of materials from rubber, nylon to stainless steel are used to transport compressed air from one Pneumatic component to the other, similar to wires in electric circuits. Tubing typically plugs into push-to-connect fittings on actuators and valves to allow for a secure yet removable connection. This includes silencers to reduce the noise volume of exhausting air
5 Things to consider about Pneumatics
- Air Quality – Moisture– When compressing air, you concentrate all that is in it. Especially includes moisture. Even on cold, dry days, there is sufficient moisture in the air to create a problem. Water in airlines corrodes metal parts they come into contact with, causing valves to seize, damaging seals and other components. It is vital to ensure the air in the system is dry by installing an appropriate air dryer system to remove moisture.
- Air Quality – Particulate – Keeping air clean is critical to maintaining a reliable pneumatic system. At a minimum, air should filter down to 5 microns. It’s recommended filter elements should be replaced every two years or when the pressure drop across the filter exceeds 14 psi.
- Meter In vs Meter Out –There’s an old saying in fluid power “When in doubt, meter out.” Metering out is when you control or limit the airflow exiting a component. Metering in is controlling or restricting the airflow entering a part. In most scenarios, you’ll want to meter out. Doing so will ensure smooth motion of actuators, especially at low speeds. Metering in can result in a stuttering motion. Why would you meter in? One example would be for single-acting actuators. You can’t control the air leaving the cylinder, so you have no choice but to control what’s entering it. The spring force acting against the piston will help eliminate the stuttering motion.
- The proximity of valves to actuators – You’ll want to physically mount valves as close as you can to the actuators they control. Minimizing the lengths of airlines to flow through from the valve to control the actuator. Longer tube lengths mean there’s more volume needed to fill to reach working pressure. On the retract stroke, that’s extra air needs to be vented and has to travel farther to do so. Adding cycle time and needlessly consumes compressed air.
- Speed– Typically, the most significant factor in limiting the speed of an actuator is the air exhausting from the low-pressure side. As pressure decays, there is less energy available to move air particles through tubing and out through the exhaust port. As stated above, having needlessly long tubing lengths compounds this problem. One solution is a quick exhaust. These get plumbed near the cylinder port. During the high-pressure cycle, these stay closed. During the low-pressure period, they open up and allow air to vent to the atmosphere right at the cylinder port, dramatically reducing restrictions on the exhaust air, increasing speed. Always keep in mind, maximum speed specifications and implementing some form of shock absorption should cylinders be travelling the entire stroke length at high speed.