How Fountain Drink Technology Enabled Lifesaving Vaccines
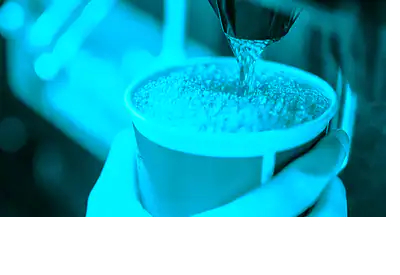
December 13, 2021
Think about the last time you enjoyed a bubbly fountain drink—perhaps a cold root beer or cola. Now imagine that same technology being put to use in the production of a lifesaving vaccine.
In 2015, when Parker’s Bioscience and Water Filtration Division shifted operations to support the life sciences market, the team could hardly have imagined what a critical move it would turn out to be. By end of 2020, less than one year into the coronavirus pandemic, the division’s Inline Dilution System had been used to support the production of numerous vaccines.
“In June we got a phone call from one of our pharmaceutical manufacturer customers asking for support in its vaccine campaign,” explains Dean Pighin, engineering manager for Parker’s Bioscience and Water Filtration Division. “We brainstormed with the team and realized we had an enabling technology we could bring to this application.”
The challenge was multifold—how to rapidly transform the way vaccines are manufactured at scale. In order to mass produce enough vaccine locally to align with global demand, drug manufacturers would first need to obtain enough raw material to meet accelerated manufacturing needs.
The team started by incorporating existing Parker tech –including patented high-precision, single-use sensors from its portfolio and an inline mixer that was about to be commercialized in another application—and added software and automation. The result? The SciLog® Inline Dilution (ILD) System, a new-to-the-world solution designed for high volume manufacturing.
“The basic principle of inline dilution is combining two streams of liquids and mixing them together, like we do in a soda machine,” explains Michael Maben, engineering supervisor for the division. “And that’s exactly what our inline dilution system does in vaccine production. It combines the buffer ingredient with purified water, mixes it together and sends that solution off to the rest of the process.”
Not only does the ILD mix up to four vaccine ingredients gently and quickly without the need for machine changeovers, it saves Parker’s customers time and turns what had traditionally been a manual process into a more efficient automated one.
“For the system to work and the application to work and for us to be able to provide all the benefits of water on demand, these ‘smart’ ILD machines must communicate with the plant and each other constantly,” adds Pighin. “We call it handshaking or a heartbeat—the system ensures that communication hasn’t broken down, all the utilities in the plant are running optimally and reports the exact volume consumed so our customers can factor that into their production planning.”
The ILD machines haven’t been the only ones in constant communication. The realities of going from problem to working prototype to onsite testing to full production in the span of just five months, during a global pandemic fraught with supply chain disruption, is central to this story as well.
“It took a lot of research, development and trial and error,” says Pighin. “We went from taking things off the shelf to sourcing parts from anywhere we could. Luckily, Parker had seen the writing on the wall and made some strategic investments in raw materials. The supply chain team really rolled up their sleeves to make it happen for us.”
Clearly, this is a team that has gone above and beyond fulfilling customer requirements to create a positive impact at a time when the world needed it most.
“We’re lucky to represent Parker in telling this story but it was definitely a team effort–a great collaboration story touching so many different engineers and departments,” says Maben. “When I was onsite with our customer, I watched vaccine being produced knowing that, in a few months, it would be put into vials and sent out across the world. These projects often last a number of years, so it’s rare to get to see the end result. The direct impact of this made it all the more rewarding.”