Endress+Hauser Transitions to New Customer Experience Centre, Showcasing the Best in Process Automation
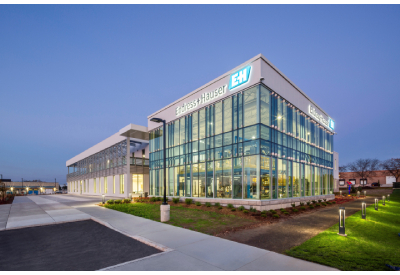
November 24, 2021
The staff have moved into Endress+Hauser’s Customer Experience Centre, the company’s new $28-million platform in Canada for showcasing its best-in-class instrumentation technology. Customers who visit the 47,000 sq ft, state-of-the-art support and training hub can expect to get a hands-on feel for the latest innovations in process automation to help them select the right products or solutions for their needs. Every effort went into ensuring the building offers a superior customer and employee experience throughout while demonstrating environmental leadership by operating on a net zero energy and carbon basis.
The two-story Customer Experience Centre will serve the customer base from Manitoba to Atlantic Canada, with an inauguration planned for next spring. The facility boasts a state-of-the-art Process Training Unit (PTU) – Endress+Hauser’s second in Canada – as well as a full-service calibration laboratory, second to none in the country, that’s capable of handling the entire spectrum of flow, temperature, pressure, and liquid analysis instrumentation. The PTU concept, featured in many Endress+Hauser facilities globally including Edmonton, is essentially a full-sized pilot plant with a wide range of the company’s instrumentation installed and fully functional.
“After almost two years of being limited to Zoom and Team calls with customers, having such an exceptional showcase where they can come see equipment demonstrated, ask questions of our experts, even handle some products, is going to be a delight for us – and a competitive advantage,” said Anthony Varga, General Manager, Endress+Hauser Canada. “Those visitors will get a value-added experience, which in turn will be a great relationship-builder.”
The facility was designed to extremely demanding environmental standards. The building generates its own electricity, heat, and cooling. It boasts a reflective roof with double sided solar panels to generate green power during the day. At night, most electrically powered systems like video monitors will be turned off rather than draw even standby power and the building environment is maintained by heat pumps supplemented by a geothermal system. A months-long testing regime necessary to gain LEED Gold and net zero certification has begun.
The Customer Experience Centre also is the new home for the company’s Burlington-based sales, service, and administration staff, with almost double the floor space of the building around the corner it replaces. Throughout the project design and development, the company’s intent was to ensure the comfort and well-being of employees. Building amenities include two cafes, a fully equipped health and fitness room, a wellness room for private time, as well as a multi-faith prayer room. There is an atrium with a live, full-sized tree for both aesthetic enhancement and oxygenation, and an outdoor terrace for employees and guests to enjoy.
None of this would have been possible, said Varga, without the enthusiastic and unflagging support of senior management of the family owned Endress+Hauser Group. “At the outset, they urged us to be bold, to create something special for all of our stakeholders that would reflect the company’s values. That’s so typical of Endress+Hauser’s corporate culture – to take the long view, to invest in our customers, employees, and communities, as furthering their success furthers ours.”