Safe Handling of Bolt Blanks: Grippers in Welding Production
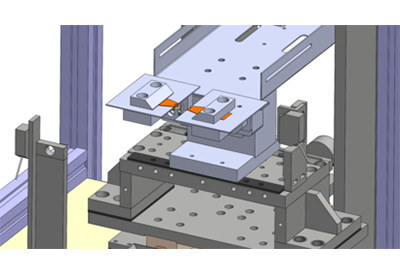
December 24, 2020
The metalworking industry is one of the most important manufacturing industries in the world. Welding technology plays a major role in the metalworking industry. Companies from this area are often pioneers in the development and application of new manufacturing and joining processes in production. While manual electrode welding is still frequently used on construction sites, companies that can carry out their production in their own factory are increasingly turning to automated production systems. In addition to the conventional metal shielding gas welding process (MSG), new, modern welding processes are being used time and time again. The metalworking industry also offers large areas of application and development potential in terms of automation. Robot applications in combination with gripping and sensor technology are increasingly finding their way into this industry, which is characterised by both single batch and series production.
Automated welding process
One of the most modern and innovative welding plants in the world is located in Taiwan, (about 9,000 kilometers away from Germany). A subsidiary of a globally active manufacturer in the field of fastening and dismantling technology produces fastening elements such as bolts and screws there. In this plant, which is subject to strict secrecy, the joining process of bolt blanks was automated using a special welding device. The actual welding process is quickly explained: A robot arm (an in-house built pneumatic linear Pick & Place unit) feeds an unwelded bolt head to a gripper. This grips the blank with special gripper jaws or gripper fingers made of stainless steel, in which copper electrodes are inserted. The gripper itself forms the counterpart to the welding head and is mounted horizontally below the welding head in the system. In addition to feeding, the gripper has the task of fixing the bolt heads for the welding process. Reliable alignment of the heads must be guaranteed for each weld in order to keep reject rates to a minimum. After the welding process, the gripper drops the bolt blank. In addition, the gripper has a no less important function: its gripper jaws also serve as electrodes and are connected to the welding inverter via two cables. The welding inverter is not, as one might think, another welding process, but another welding power source. This means that an inverter welding machine is added to the transformer and rectifier. Inverter welding machines are available for all common welding processes, such as manual electric welding, gas-shielded welding and also TIG welding. Nowadays, these are becoming more and more popular compared to the regular welding power source, as they offer advantages such as smaller size as well as additional functions.
Gripping under the most adverse conditions
For this demanding task under the most adverse conditions, the system developers decided to use two GPP5010N-24-A grippers from Zimmer Group, the gripper specialist from Baden, Germany. The premium grippers of the 5000 series are universally applicable pneumatic grippers that offer high gripping forces with short cycle times, have sealed steel-in-steel profile groove guides and also feature high repeatability. The conditions on site in Taiwan and the requirements for the use of the “Zimmer grippers” in the welding process were sometimes very challenging. Thus, precision played an important role from the very beginning: The bolt parts had to be welded together with an accuracy of 0.2 millimeters. It was therefore necessary for the grippers to achieve a repeatability during gripping of 0.1 millimeters. (Note: 0.2 – 0.1 = 0.1 for the accuracy of the welding head). Another important requirement for the grippers was their protection class. Since the grippers are located directly next to the welding zone and thus have to perform their work permanently under the most difficult environmental conditions, they should also have appropriate protection or corrosion protection. Resistance to welding spatter and metal fumes was therefore a crucial criteria. With the previous gripper solution of a market competitor, these adversities caused severe wear in the profile guides. To eliminate this danger, the GPP5000 was selected from the extensive Zimmer Group portfolio, two grippers with the highest protection class, IP67. It was also easy to install the new grippers. Since only the existing gripper mechanism was to be replaced, the new grippers could easily be integrated into the existing installation space due to their compact design.
Success with superior longevity
The use of the new grippers quickly paid off in the welding process and in the plant. For example, no maintenance has been required for two years, whereas the old solution required a monthly effort of four to eight hours for service. As already mentioned, the grippers are directly exposed to welding spatter as well as gases. The fact that the grippers are able to withstand these influences is demonstrated by the fact that, despite this harsh environment, the bolt heads continue to be gripped in the correct position even after 20 million cycles.
According to the customer’s data, the cycle time remained unchanged, as this depends on other components in the machine, but due to the unsatisfactory performance of the previous gripper solution, the return on investment (ROI) for the new grippers is around two to four months. Furthermore, the development team on site was enthusiastic, as there was no need to invest in development capacity for a very well-functioning “standard component” and it was possible to focus on the core technology of the machine. All in all, not only the developers, but also the machine operators and the maintenance team perceived the changeover to a Zimmer Group gripper as a significant improvement and therefore nothing stands in the way of further cooperation with this Taiwanese company.