Gapless Safety from Leuze
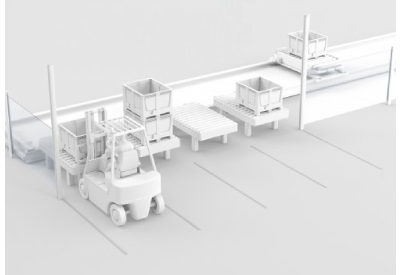
December 19, 2022
In applications where corridor supply vehicles interact at transfer stations with a direct connection to a danger zone, operation must be as safe and efficient as possible: Throughout the entire area, the safety system must be able to differentiate reliably between forklift trucks and, in some cases, also people. This is possible using a Leuze safety solution for multi-station access guarding in forklift truck logistics.
Transfer stations at which forklift trucks carry materials in and out are often connected to danger zones. System operators must safeguard the access points of these areas
Person or vehicle?
Transfer stations are often directly connected to danger zones. At these stations, corridor supply vehicles such as forklift trucks carry materials in and out. These zones can be dangerous for people in the immediate vicinity due to adjacent machines or cross conveyors that feed the transfer stations. Both manufacturers and operating companies are therefore responsible for safeguarding the access points of the machines and transfer stations. The challenge is how to ensure maximum efficiency during operation while also protecting operators and other people. To fulfill these two aims, the safety concept must be able to reliably differentiate between forklift trucks and people. Two safety functions are particularly relevant here: Firstly, stopping the dangerous movement in good time. Secondly, releasing access to the danger zone only to specified forklift trucks. Various concepts are possible and in use to prevent people from accessing such transfer stations and permit only forklift trucks to enter. However, the safety-related evaluation of these concepts often shows significant differences regarding the residual risks. Such risks can even be so great that a concept proves insufficient.
Conventional muting with a high residual risk
An obvious approach uses a type of “muting” with induction loops as a trigger signal. The induction loops, which are embedded in the floor before every transfer station as “muting sensors”, make it possible, in principle, to differentiate between high-lift trucks and people. However, to differentiate SAFELY, additional evaluation measures are generally required. Nevertheless, the main dealbreaker for this approach is ultimately the muting requirements specified by standards such as IEC 62046, which are not met. This is because, if all transfer stations are safeguarded jointly by an active opto-electronic protective device (AOPD) used for muting, the presence of a forklift truck on one loop pair triggers the muting function for the entire area – i.e. across all stations.
At that moment, people can enter the danger zone along with the forklift truck, undetected and without realizing. While the high-lift truck stands on the induction loop, the muting function is active and the safety function of the AOPD is overridden.
At the same time, the lateral distances between the muting object (here, the forklift truck) and the fixed limit are far too great and therefore no longer compliant. As a result, a conventional muting approach is not suitable for this type of application. In addition to the large amount of effort required to install the induction loops, the approach has residual risks and does not comply with the muting requirements of standards.
One access-guarding approach: An active opto-electronic protective device (AOPD) is located before the transfer stations and covers all stations. Two loops are installed before every AOPD. With this approach, the muting requirements of standards such as IEC 62046 are not met
Better suited intelligent safety concepts
A better approach for multi-station access guarding in forklift truck logistics is based on sequence- and time-monitored protective field adjustment that fits the zone precisely. In these respects, this approach differs greatly from the above-mentioned muting concept, which is primarily timing controlled and covers the whole area. The principle: Safety laser scanners with vertical protective fields safeguard the access area for all transfer stations. At each station, additional sensors monitor the entrance of forklift trucks and supply this information to the safety system. These sensors detect when a forklift truck drives into the transfer station from in front. Only in this case does the safety concept release a defined area in the protective field precisely for this one station.
During this process, all other stations remain safeguarded by their own protective fields, which are still active. Once the forklift truck has left the transfer area, the protective field is reset to its original state and the whole area is once again safeguarded. As part of this approach, the functionality of a Leuze safety laser scanner allows it to safeguard multiple transfer stations simultaneously.
There is a residual risk here: If there is a high-lift truck on the induction loop, meaning that the muting function is active, people can enter one of the other stations without being detected by the safety system. During the muting, problem-free bypassing is easily possible
Interruption-free operation
Another advantage of this solution is that this safety concept enables goods to be handled at transfer stations that are intended for this purpose and located behind an opto-electronic protective field, without interrupting the work processes of adjacent machines. All stations can be used simultaneously and independently of each other. With this safety concept, the traffic area and the transfer area are safely separated from each other – this enables optimum workflows. Above all, this safety concept differentiates reliably between forklift trucks and operators. The access-guarding protective fields must be positioned in such a way that the necessary safety distance from the danger zone is complied with.
The time required to stop the dangerous movement must be taken into account. The requirements according to EN ISO 13855 and EN ISO 13857 apply here. To ensure that the system detects the forklift trucks reliably, system operators should use high-lift trucks that are similar in size and shape. In addition, there is a minimum speed at which vehicles must enter the transfer station to be detected as vehicles.
A more efficient and safer concept is the sequence- and time-controlled protective field adjustment from Leuze: The system differentiates reliably between forklift trucks and operators. Forklift trucks can enter and leave the area without interrupting operation and all stations can be used simultaneously and independently of each other
An optimal combination: Laser, ultrasound and radar
The Sensor People from Leuze offer this concept as a safety solution in a complete package. A core component is the RSL 400 safety laser scanners. They are installed vertically above the transfer stations so that they can safeguard the entire access area. A practical feature of the RSL 400 is that it can safeguard multiple transfer stations simultaneously due to its operating range of up to 8.25 meters and the parallel operation of various protective fields. This reduces the installation effort and helps to create a cost-optimized system design. The Leuze project teams flexibly adjust the protective field configurations that are appropriate for the respective system to the conditions on site. The safety laser scanners are characterized by their robust operation. They filter out objects such as dust and particles due to their high angular resolution of 0.1 degrees – this makes the sampling rate 3x higher than that of conventional scanners. Other components of the safety solution include ultrasonic and radar sensors that are used for each station. A Siemens safety control, together with the associated Leuze safety program, is used to control the overall system.
Danger averted
For system operators, this approach to multi-station access guarding pays off: It is suitable for retrofitting existing systems as well as for new systems. The solution reliably differentiates between forklift trucks and operators, and operation is not interrupted. Even protection against bypassing is optimized and tampering prevented. The safety concept meets the requirements for performance level d according to EN ISO 13849-1 and therefore contributes significantly to reducing the risks at transfer stations. The safety integrity level according to EN IEC 62061 is SIL 2. In addition, the solution can easily be scaled to the number of stations at any time – this offers flexibility for later extensions. The Leuze safety experts are happy to advise anyone interested in this concept at any time. They provide support relating to the safety solution from the target/actual analysis to the hardware selection including accessories, to the configuration, start-up support and validation of the application.