Rotary Encoders for Harsh Environments
January 30, 2023
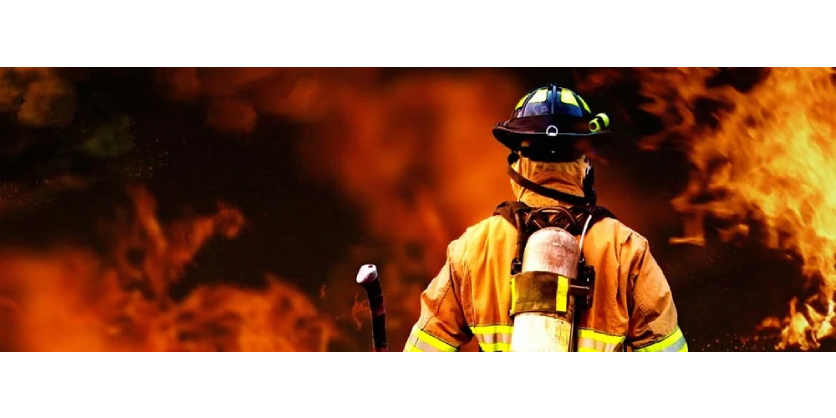
Rotary encoders are electromechanical devices that provide feedback on the rotational movement of an axle or shaft. Comprising two parts – a reader and a scale – they typically accomplish this task either by either “absolute encoding” or “incremental encoding”: Absolute encoders measure the precise angular position of the reader relative to the scale, while incremental encoders sense the motion of the scale relative to the reader.1
Whether incremental or absolute, rotary encoders are vital in virtually all automation or robotics applications that involve precisely controlled rotational movement. Conveyor systems, for example, commonly use them on drive wheels to control the speed and position of the belt. Likewise, they are used in elevators to ensure that elevator cars start and stop smoothly and in the right place. Any rotational robotic joints will also contain rotary encoders to ensure movement is accurately controlled.
Harsh Environment Applications
Rotary encoders are fundamental to industrial motion control, so they’re frequently relied upon to perform in harsh environments. These applications include paper manufacturing, chemical/petroleum processing, cranes, food and beverage processing, and a range of other harsh manufacturing and processing environments.
In these environments, many things can cause rotary encoder failure, including mechanical overload or signal output failure. However, solid or particulate contamination is the most common cause of rotary encoder failure.
Contamination is of particular concern for optical encoders.2 Optical rotary encoders are unparalleled for accuracy, meaning they’re the most common type of rotary encoders. However, because they depend on a clear line of sight between reader and scale, optical encoders are extremely sensitive to solid or liquid contamination that might make its way between these two moving parts.
While rotary optical encoders can be protected to some degree, seals and enclosures typically slow the rate at which contamination can enter the encoder. In heavy industrial applications, seals can wear, and temperature variations can cause rotary encoders to draw contaminated air into the enclosure. Once optical elements are contaminated, rotary encoders can start to behave unpredictably or stop functioning altogether.
These encoders are commonly exposed to all manner of solid particulates, including sand, sawdust, and other forms of dust and dirt. Liquids such as water, coolants and lubricants are also a common threat to rotary encoders – particularly problematic in applications such as food production where machinery is cleaned with high-pressure water.
For heavy-duty applications in challenging environments, inductive types are often preferred. Because inductive sensors rely on electromagnetic sensing, no line of sight between the reader and scale is required. This means that inductive rotary encoders are effectively impervious to contamination. Both the reader and the scale can be independently enclosed, providing a robust non-contact solution.
Heavy-Duty Enclosed Rotary Encoders from Celera Motion
A world leader in motion control technology, Celera Motion provides a full range of high-performance motion control systems and components, including optical rotary encoders and inductive rotary encoders.
Our Ultra IncOder series of inductive rotary encoders offer unparalleled performance in harsh environments. As well as superior ingress protection, proven in a range of defense and industrial applications, the Ultra IncOder offers extreme accuracy of up to 19 arc seconds. The low-profile form factor and large bore make it easy to adapt Ultra IncOder sensors into a wide range of automation and robotics applications.
To find out more about our range of inductive and optical rotary encoders, get in touch with Celera Motion today.
Related Product
Celera Motion Introduces Ultra-Lightweight Inductive Angle Encoder
Celera Motion has recently introduced their new ultra-lightweight inductive angle encoders, featuring a bearingless, compact PCB construction with an ergonomic hollow bore design. These encoders require no calibration with no precision installation tolerances, and have absolute position feedback and an immunity to contamination.