Three Questions to Ask Yourself When Selecting an Autonomous Mobile Robot Vendor
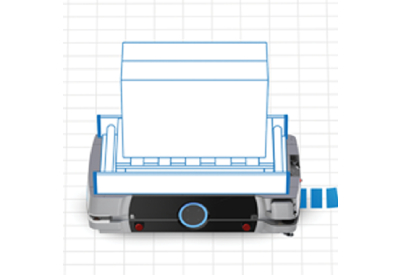
December 5, 2022
Order picking is perhaps the most time-consuming and labor-intensive activity that is essential to the logistics industry, and it’s ripe for automation with today’s most advanced robotic technologies. Autonomous mobile robots (AMRs) have recently emerged as one of the most effective ways to eliminate cumbersome manual processes and streamline logistics operations.
AMRs differ among automation vendors, so it’s important to have a good grasp on the specific features of each version of the technology and whether these will address the specific needs of your application. Certain AMRs have capabilities that make them more likely to offer the greatest value in any application and help logistics companies prepare for the future. This article looks at three questions that will help you determine whether a specific mobile robotic technology is right for you.
1. Is the navigation reliable and maintainable?
The selling point of AMRs — as opposed to highly inflexible conveyor systems or semi-flexible autonomous guided vehicles (AGVs) — is that they can move throughout dynamic and peopled environments without requiring any facility modifications (not even floor magnets or wall-mounted beacons). This makes it much easier to change the floor layout when necessary.
AMRs first create a base-line map of the facility using their sensors, and afterwards they will compare this map with what they “see” during their operation. This lets them automatically reroute to avoid sudden obstacles. Since there’s no need to pre-designate a path, autonomous robot navigation is more flexible than AGVs, reducing their total cost of ownership (TCO).
Be sure to choose AMRs that can detect ANY obstacles, not just the “expected” ones. Most AMRs have little trouble detecting objects between floor level and average knee-height, but they might miss objects hanging from the ceiling or drawers sticking out unexpectedly from cabinetry. Side lasers are a great thing to look for if your facility contains such obstacles.
Thanks to our exceptional robot navigation technology, Omron makes AMR installation easy. Learn more about what goes into mobile robot ease of use in this white paper.
2. Can the AMRs collaborate in a fleet?
Once logistics companies see the advantages a single mobile robot can offer their facilities, it’s unsurprising that they often want to implement more of them. This ultimately leads to developing an AMR fleet, which uses a fleet management system to automatically allocate tasks in the most efficient way.
There are two main ways to identify a good fleet management system. The first is whether it manages traffic in such a way that robots don’t end up blocking each other’s paths or waiting too long for others to pass. The second has to do with efficient job management and whether the jobs are completed in the least amount of time with the least distance travelled overall.
A good fleet management system can even “look ahead” and predict which nearby robot will be available soon to work on the next job. It’s also important for it to manage the schedule in such a way that each robot can disengage to automatically recharge its battery.
Interested in more automation solutions tailored to the needs of the logistics industry? Check out our logistics-focused robotics portfolio.
3. Do the AMRs have the right safety measures?
AMRs are quite different from industrial robots. They can operate around people without needing to be fenced off in giant, heavy-duty cages. However, there are still some ways in which they can be unsafe, and it’s important to make sure your vendor has found ways to mitigate concerns around mobile robot safety.
Stable stopping is a common issue. This depends directly on the robot’s center of gravity, which changes when the robot is fully loaded. Make sure the AMRs can detect obstacles in the way early enough to stop smoothly. With Omron’s technology, you can also program zone sets into the AMR area scanners to react to unexpected obstacles depending on level of severity.
In the case of an emergency evacuation, mobile robots don’t need to get out of the facility, but they could get in the way of people escaping if they continue to work as though everything was normal. It’s important for your external alarm system to tie in properly with the robots’ internal messaging to coordinate their actions.