Festo Introduces Pneumatic Essentials – a Program for Easy-Order/Fast-Ship Pneumatic Products
January 17, 2023
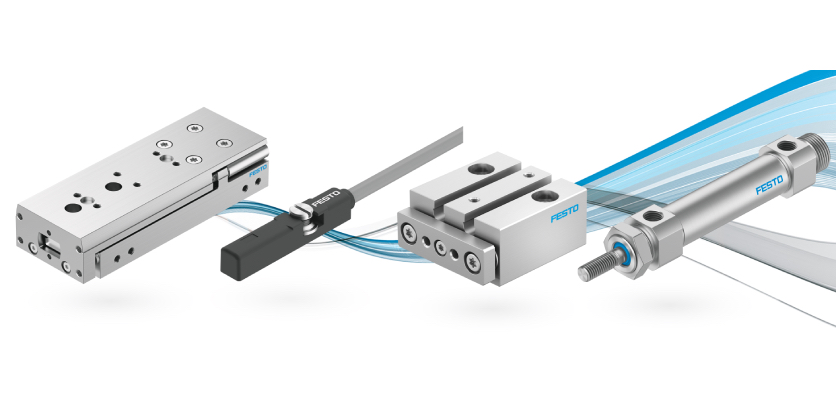
Festo launches the Pneumatic Essentials program, an ambitious global undertaking to streamline ordering, ensure fast delivery of guaranteed in-stock pneumatic components, and produce more compact parts for today’s smaller footprint, energy efficient machines. In addition to competitive prices, guaranteed availability, short delivery time, and innovative design, customers are assured of world-renowned Festo quality components that boost machine performance, lower waste, and reduce the risk of downtime.
Pneumatic Essentials is a one-stop-shop for the 16 fundamental components that Festo finds fit most common pneumatic applications. These components include air preparation, high wear polyurethane tubing, one-way flow control valve, high flow valves for normal and harsh environments, self-teaching proximity switch, mini slide, guided drive, direct interchangeability ANSI NFPA cylinders, and metric and imperial round and compact cylinders.
Making something so simple isn’t easy. Festo invested sizable resources over four years to create Pneumatic Essentials.
North American customers will experience short delivery times for both catalog and customized Essentials components from the Festo Global Production Center in Mason, Ohio. Quick, assured Essentials shipping is available to customers globally from Festo regional service centers. Global availability is an inventory and uptime plus for original equipment manufacturers and end users, as they are assured of rapid receipt of replacement parts.
Festo invested substantial time, energy, and resources in augmenting manufacturing and logistics to ensure a robust supply chain for Pneumatic Essentials. And the company was not content simply to rebrand existing components. Festo identified key products that would benefit from upgrading and built new manufacturing lines for those with new designs. For example, the new design-award winning SDBT-MSX proximity sensor is the world’s first programmable proximity switch with automatic switching point setting.
Smaller, lighter parts contribute to reduced footprint and more energy efficient machines and are important attributes of Essentials products. The DGST pneumatic mini slide, for example, is one of the most compact units on the market. Festo machines the DGST slide and yoke plate from a single piece of aluminum, ensuring low torsion and accurate alignment.
A new ultra-compact double-acting cylinder, the ADN-S, is 36% shorter and 20% lighter than similar actuators. And the round body metric cylinder, DSNU-S, has the same bore and stroke as its ISO counterpart DSNU, yet is up to 40% slimmer, 35 mm shorter, 50% lighter, and ideal for space constrained applications.
For more information on the advantages of working within the Festo ecosystem ‒ the ecosystem that leads to less engineering overhead, fast time to market, and seamless connectivity ‒ visit Festo Essentials | Festo Canada
Related Story
Moving Into the Future with Controlled Pneumatics from Festo
The production of tires and the production of wafers seem to have absolutely nothing to do with each other. In terms of automation technology, however, they use the same technology: Controlled Pneumatics. That is why Festo has further developed compressed air technology to make pneumatics sustainable, resource-saving and energy-efficient.
In Controlled Pneumatics, Festo combines proportional technology, sensors, and control algorithms to form a control loop. These are mechatronic pneumatic systems with innovative valve and communication technology that enable digital influence in conjunction with closed-loop control based on a sensor variable.
This technology creates new areas of application, especially for pressure and flow control, that push the limits of pneumatics and enable simpler, more reliable, faster, more precise, and more efficient solutions. Conventional standard pneumatics, on the other hand, are used specifically for simple applications such as point-to-point movements. It is above all the simplicity of standard pneumatics that makes it the ideal solution in many cases.