Precise Gear Machining Every Second
November 11, 2024
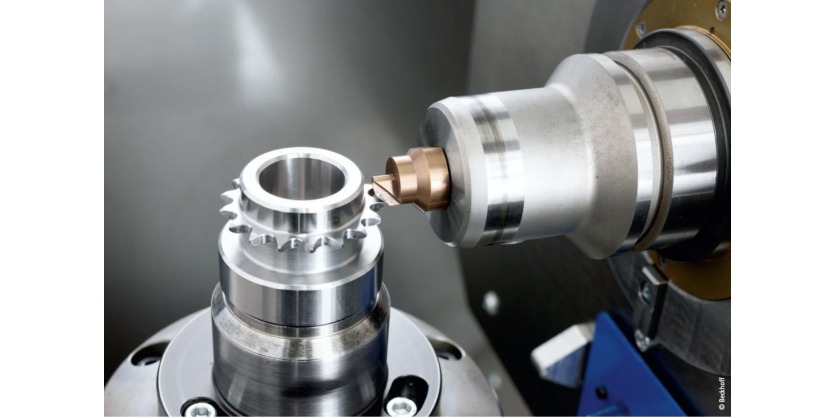
PC-based control automates the chamfering and deburring of gears
Many innovations have their roots in the Black Forest, including radial chamfering, which Tec for Gears (TfG) from Furtwangen are using to automate a previously predominantly manual production step with TwinCAT NC PTP and EtherCAT oversampling terminals from Beckhoff, among other things. The gear chamfering and deburring process becomes precise, reliable, and so fast that it can be integrated directly into production.
During chamfering, a rotating cutting tool moves radially into a rotating gear, removing burrs on the gear contours. The aim is to create a precise chamfer on the tooth front edges. “The tool moves along the front of a gear, removing material in the process,” explains Niklas Müller, founder and Managing Director of Tec for Gears in Furtwangen. This results in the continuous processing of components. This may not sound like a high requirement at first, but the process is demanding in terms of control technology.
“Synchronizing the two axes – which are rotating at different speeds – with each other in a defined rotation ratio alone is a challenge,” says Deter Völkle, member of the sales team at the Beckhoff branch in Balingen. This is because the spindle rotates at up to 17,000 revolutions per minute and the workpiece in the chuck rotates at up to 1000 revolutions per minute. The rotation ratio of the two spindles is determined by the respective boundary conditions of the workpieces and tools.
CNC or cam plate?
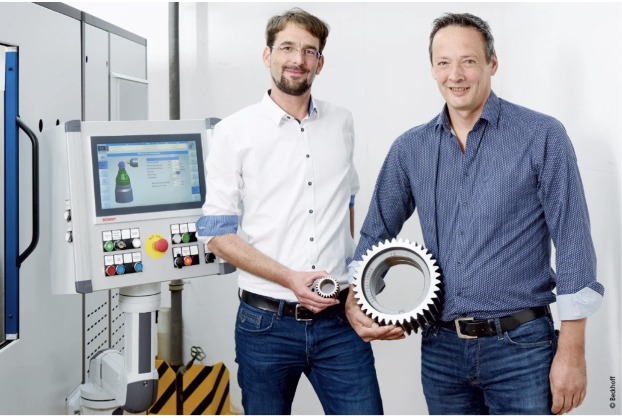
Initially, it was not clear whether a CNC was required, whether cam plates were sufficient, and how quickly the tooth gaps had to be detected. In the end, the special requirements of the chamfering machine were achieved with TwinCAT 3 PLC/NC PTP, TwinCAT 3 NC Camming, and TwinCAT 3 Motion Control XFC, which run together with the TwinCAT HMI server on a CX5140 Embedded PC with an Intel Atom® quad-core processor. “Dieter Völkle supported us with his expertise in designing the system right from the start,” explains Niklas Müller.
Given that the gears are clamped in an unaligned position, the cutting tool and tooth gap must be precisely aligned with each other before machining. However, this should not significantly increase process times. The tooth gaps are therefore detected at a high speed. Depending on the number of teeth – the proximity switch used delivers two pulses per tooth – this results in a very fast signal sequence. To record these signals, TfG uses EL1258 EtherCAT Terminals with a multi-timestamping function to achieve a sampling rate of up to 100 kHz and to transmit the sensor pulses to the controller using several timestamps. The exact position of the teeth are determined and the clamped product is verified at the same time.
In addition to the encoder signals of the rotation axes, the values of a linear measuring system for compensating thermal expansion are also incorporated into the synchronization and positioning of the tool. The synchronization between the tool spindle and the workpiece axis must be correspondingly stable – even when the machining forces are added during chamfering and at spindle speeds of up to 17,000 revolutions per minute. Volker Eschle, Sales at Tec for Gears, comments:
“The continuous and fast rotation of the component and cutting edge enables our RGC350 chamfering machine to achieve very short cycle times while maintaining a high and, above all, consistent machining quality.” TfG achieves the high repeatability with precise motion control from Beckhoff, AX5000 compact servo drives and AM8000 servomotors. “No other control manufacturer would have been able to automate our machine with such performance and precision with their technology,” says Niklas Müller.
OEMs are demanding “clear edges”
More and more OEMs and their suppliers are now demanding precise, defined chamfers on the tooth fronts and are writing “chamfering that is true to contours” in their design drawings. This is no longer possible using conventional deburring in the gear cutting machine, which produces a burr-free but sharp edge. This is why the industry needs radial chamfering technology. With automatic loading and unloading, the RGC350 can chamfer up to one million parts per year. As a rule, the machining time per gear is eight to ten seconds for the complete process which involves clamping the workpiece, detecting tooth gaps, axis synchronization, chamfering, unclamping.
The machine can be used to process virtually all types of gears ranging between 10 and 300 mm in diameter – even those with double or multiple teeth and interfering contours. Components with helical gearing can also be machined. A further spatial axis and coupling is then taken into account when calculating the curves to compensate for the helix angle.
HMI masks complicated technology
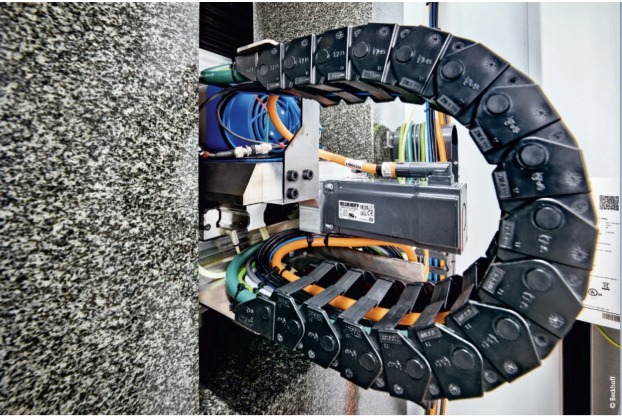
Niklas Müller states that, despite this variability, machine operators need no more than 10 minutes to retool the machine to fit a new gear. “All data for automatic chamfering is imported into the control via XML,” adds Dieter Völkle. The operator only has to call up the data set associated with the job in the visualization implemented with TwinCAT HMI and clamp the corresponding tool.
This uncomplicated retooling process makes the RGC350 interesting not only for large quantities, but also for contract manufacturers with changing orders and small batches. “One of our customers was able to replace four manual workstations requiring two-shift operation with one machine and then instate the employees elsewhere,” says Volker Eschle.
In order to convert processing speed into added value, most customers integrate the chamfering machine into their production processes with an automatic material feed and removal system. The flexible and open nature of PC-based control is demonstrated in such projects, which allows for the implementation of customer-specific adaptations. Extensions such as additional drive controllers and motors are easily and quickly implemented and integrated into the control program.
“This flexibility helps us to implement our customers’ ideas as well as our own, of course, without having to modify the basic concept,” enthuses Niklas Müller. Another reason to rely on Beckhoff as a control partner is that they are always ready with advice in case of questions or problems and provide competent and solution-oriented support.
Efficient tool management
One development project concerns tool management. This is because each gear variant requires the right tool for chamfering, which TfG has manufactured in Germany based on the component dimensions. Depending on the variation of components, a customer has to manage a large number of tools and take their service life into account when planning orders. This helps them to make optimum use of the tools and to avoid producing faulty parts due to excessively worn tools.
Currently, there are tool life counters that can be created for each individual tool in the HMI. As long as each tool has been created with its serial number in the visualization, the machine setter can then choose a tool with a sufficient tool life to match the order size. “The component is often changed, but not the tool,” says Volker Eschle. This results in a crash that causes unnecessary trouble for the customer. “We want to eliminate such mix-ups and avoidable errors in the future and optimize tool management,” says Niklas Müller. “We’ll definitely succeed with Beckhoff as our system partner.”
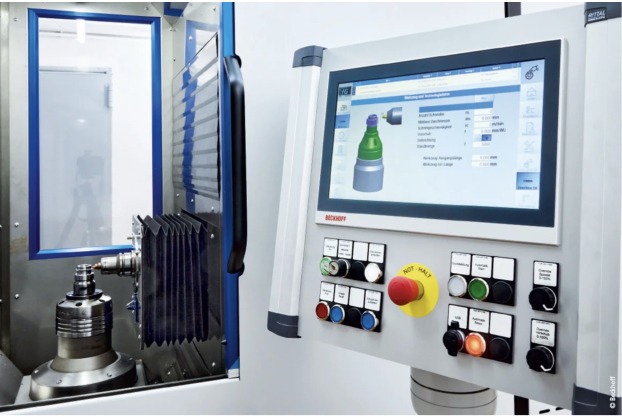
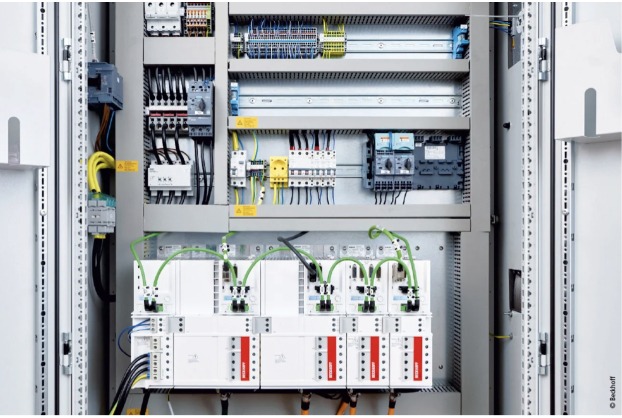
More Information
Related Story
TwinCAT PLC++: Next Generation PLC Technology
TwinCAT PLC++ is a completely new development from Beckhoff that integrates seamlessly into the existing TwinCAT ecosystem. Of course, TwinCAT PLC++ continues to be based on the languages described in IEC 61131-3. Due to – but not limited to – the advanced compiler technology and the new architecture used, a significant leap in engineering and runtime performance can be achieved.