Moving Into the Future with Controlled Pneumatics from Festo
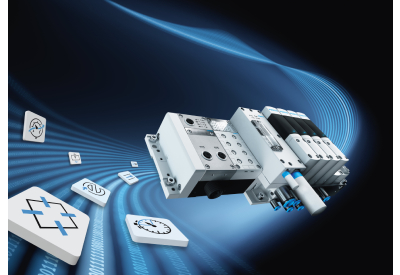
October 19, 2022
The production of tires and the production of wafers seem to have absolutely nothing to do with each other. In terms of automation technology, however, they use the same technology: Controlled Pneumatics. That is why Festo has further developed compressed air technology to make pneumatics sustainable, resource-saving and energy-efficient.
In Controlled Pneumatics, Festo combines proportional technology, sensors, and control algorithms to form a control loop. These are mechatronic pneumatic systems with innovative valve and communication technology that enable digital influence in conjunction with closed-loop control based on a sensor variable. This technology creates new areas of application, especially for pressure and flow control, that push the limits of pneumatics and enable simpler, more reliable, faster, more precise, and more efficient solutions. Conventional standard pneumatics, on the other hand, are used specifically for simple applications such as point-to-point movements. It is above all the simplicity of standard pneumatics that makes it the ideal solution in many cases.
Digitized pneumatics
A prime example of a Controlled Pneumatics product is the Festo Motion Terminal VTEM, which Festo is using to digitize pneumatics. This automation platform uses piezo technology and Motion Apps that can replace over 50 individual components within a pneumatic control circuit.
When applied to tire production, there is a potential for savings in the loading processes in the curing presses: with the Motion App “Selectable pressure level”, the Festo Motion Terminal allows the green tire blank (raw tire without tread) to be gently fed into the press. The smaller the fluctuations of the handling system during loading, the more the feeding-in speed can be increased. The process for each tire is thus accelerated by several seconds. This doesn’t sound like much at first, but with roughly 1.8 billion car tires produced each year, this can result in considerable sums for each tire manufacturer. Another advantage of controlled pneumatics is that it reduces the impact forces and thus significantly increases the service life of the components used.
Less pressure = less energy
In practice, it is not just that the loading operations are accelerated, they also require less energy because pressure can be reduced, and so compressed air consumption is also decreased. In addition, calculations reveal compressed air savings of nearly 33% when comparing the movement of the horizontally installed pneumatic cylinder DSBC with standard pneumatics, and of nearly 75% when the same cylinder is installed vertically. Just for controlling the vertical and horizontal cylinders, energy savings of roughly 60% are achieved during these loading and unloading operations.
Perfect tire material for the hot-press tire building machine: the Festo Motion Terminal VTEM now controls the different pressures on the rubber layer very simply and precisely using a Motion App
Predictive maintenance
The Motion App “Leakage diagnostics” is also used, since it simplifies maintenance and automatically monitors leakages. Malfunctions can thus be detected and pinpointed to a specific actuator using diagnostic cycles and defined threshold values. This results in a reliable basis for predictive maintenance.
Furthermore, the Festo Motion Terminal can close off the faulty air duct, thus avoiding the supply of more and more compressed air if there is a leak. The innovative automation platform thereby prevents unnecessary air consumption.
Piezo technology prevents wear
When, on the other hand, wafers need to be transported and stored in the semiconductor industry, the N2 purge system from Festo prevents oxygen from oxidizing the wafers. The cost-efficient flow controller therefore continuously supplies the atmosphere around the wafer with inert nitrogen. The flow controller, also known as the mass flow controller MFC, is based on piezo technology and integrated sensor technology.
The design of the piezo valve reduces the risk of contamination of the gas flow caused by particle abrasion over the entire service life. The peak value is around a particle size of 0.1 micrometers per switching cycle. Conventional solutions generate five times the particle content. The piezo technology used prevents wear caused by friction, thus considerably increasing the service life of the valve. In comparison to conventional solutions, this results in significant savings in operation and maintenance.
Low intrinsic energy consumption saves money
Thanks to its design, the directly operated flow controller reduces the risk of leakages. The electrical energy consumption is less than a watt. That is 80% less than with conventional solutions in both cases. The closed control loop ensures an accurate, stable and linear behaviour of the flow rate, with only minimal hysteresis. The repetition accuracy is +/-0.25% of the setpoint value.
When wafers need to be transported and stored in the semiconductor industry, the N2 purge system from Festo prevents oxygen from oxidising the wafers
With Controlled Pneumatics, the related digitalization and with piezo technology, Festo is taking compressed air technology to a new technological level that is resource-saving, energy-efficient and sustainable.
To learn more about Festo’s Controlled Pneumatics products, click here