Introducing LoadMate Plus Robot Cell for Flexible Machine Tool Tending
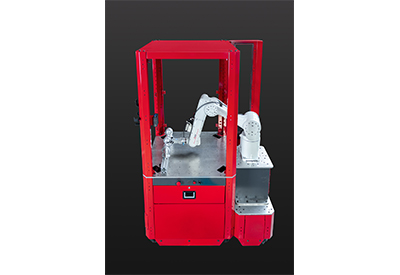
June 17, 2021
Mitsubishi Electric Automation, Inc. recently announced the release of its LoadMate Plus engineered solution. LoadMate Plus is a robot cell which can be easily moved for efficient use, and is targeted towards manufacturers in CNC machine tool applications that find themselves facing a labor crunch, while needing to be more efficient and improve their production. The robot cell provides flexible solutions for traditionally high-mix, low-volume facilities to introduce automation, and is designed with mobility and flexibility in mind.
LoadMate Plus automates the task of loading and removing parts from a machine tool through the use of robotics, and can be mounted next to one machine, between two machines, and otherwise moved around a facility as jobs require. When this cell is paired with Mitsubishi Electric M8 Series CNC, operators can use the Direct Robot Control (DRC) feature within the CNC controls to also control and program the robot with menus and G-code from the same screen used for the machine tool. No robot programming experience or teach pendant is required, allowing manufacturers to use existing staff to automate and make adjustments.
“Most automation solutions for machine tending rely on either cobots for flexibility, or industrial robots for performance and larger parts,” said Rob Brodecki, services product manager at Mitsubishi Electric Automation. “With LoadMate Plus, users don’t have to sacrifice one for the other. The cell is flexible, regardless of the robot, and users can choose from a number of robots to match a shop’s specific needs. Plus, with an available 3-year robot warranty, and Mitsubishi Electric technicians who can service LoadMate Plus, users can ensure that their production will continue uninterrupted.”
LoadMate Plus can be used with a variety of machine tools, including mill, lathe, and drilling/tapping.