ASI8100 Stepper Motors with Integrated Drives Enable Cabinet-Free Machine Concepts
December 9, 2024
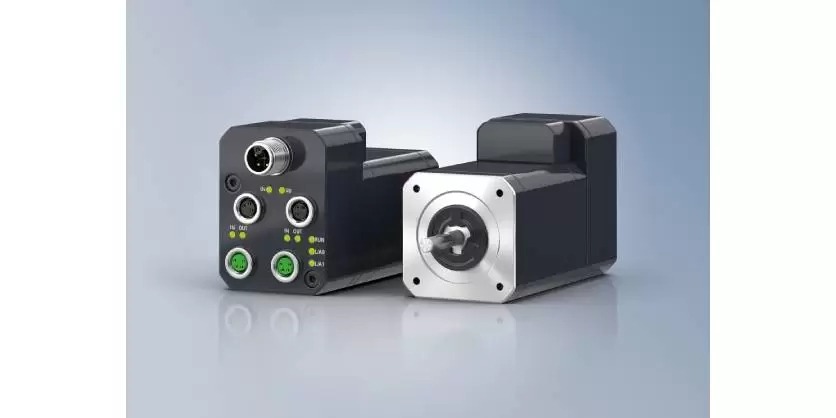
Beckhoff’s new compact stepper motor drives include onboard I/O to increase design flexibility
The ASI8100 stepper motor with built-in drive from Beckhoff adds another space-saving tool to the company’s broad range of compact drive technology products (up to 48 V DC). The ASI8100 series combines a stepper motor, stepper motor output stage, and fieldbus connection in a fully integrated design. These EtherCAT devices mount directly on the machine without a control cabinet or upstream I/O, allowing for highly compact, control cabinet-free machines.
The ASI8100 series covers all motion requirements for stepper motors in the power range up to 250 W. Easy-to-read status LEDs report drive conditions. With the integrated travel path control, simple function blocks for motion applications are built in. The standardized connectors – M8 for EtherCAT and M12 for power – minimize assembly time, cost, and complexity. The two additional I/Os enable effective execution of drive-related functions, such as the detection of end positions or latching.
The stepper series starts with NEMA 17 drives (42 mm), available in two stack lengths with a 0.29 Nm or 0.8 Nm holding torque. Four additional NEMA 23 devices (56 mm) offer holding torques of 0.75 Nm, 1.4 Nm, 2.35 Nm, and 2.5 Nm. Pre-assembled cables and infrastructure components, such as IP67 distribution box modules, are available as accessories.
More Information
Related Story
Beckhoff Launches Compact, Multi-I/O Interface for Endless Use Cases in One Device
Beckhoff’s new EL8601-8411 EtherCAT Terminal offers incredible interface flexibility in a compact, 12-mm-wide design. With up to 12 signal interfaces (8 x DI, 2 x DO, 1 x AI, 1 x AO) and nine signal types in one terminal, the multi-interface is ideal for numerous applications. These use cases include systems that require only a few complex signals or to enable highly flexible signal configuration on custom machines without adding single-purpose hardware.