ANCA’s New Era of Automation: Intelligent Solutions for Maximizing Productivity 24/7
March 30, 2022
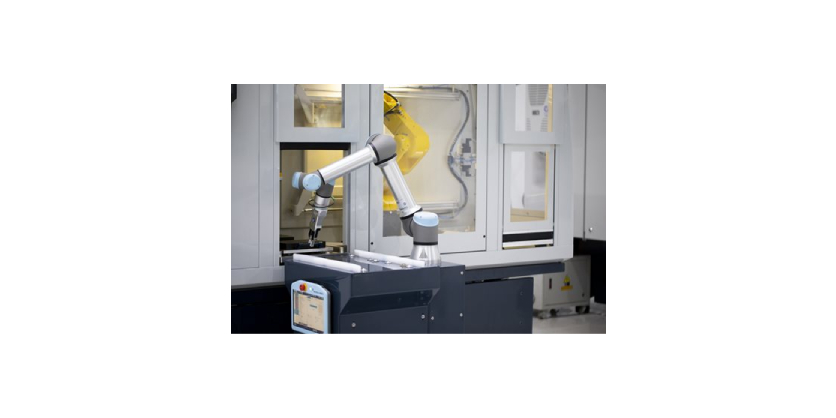
The first to market ANCA Integrated Manufacturing System (AIMS) uses smart automation and IT integration to connect tool production processes and systems.
ANCA’s launch of integrated solutions with AIMS, connects sequential processes in tool manufacturing, to bank the benefits of automation and integration. AIMS facilitates streamlined tool production, linking separate processes to each other and factory IT systems. The future of toolmaking is here, with AIMS providing versatile, modular options for common manufacturing challenges to optimise cutting tool production.
AIMS offers functionality that is adaptable to each factory’s needs; from smaller scale, data-based options to the full AIMS setup across a series of machines with endless possibilities. Central to any AIMS system is the AIMS Server that manages data flows between the elements of the AIMS system and established IT platforms, such as your ERP system. Building on this, customers can choose from a suite of “auto” solutions for reducing production costs, resolving labour challenges and integrating systems to improve product and process quality. From transferring tools between operations with AutoFetch robot options; fully automated tool measurement and process compensation using AutoComp; and managing data via the AutoSet hub – AIMS delivers streamlined manufacturing, with connected tool production processes integrated to IT systems that takes tool production to the next level.
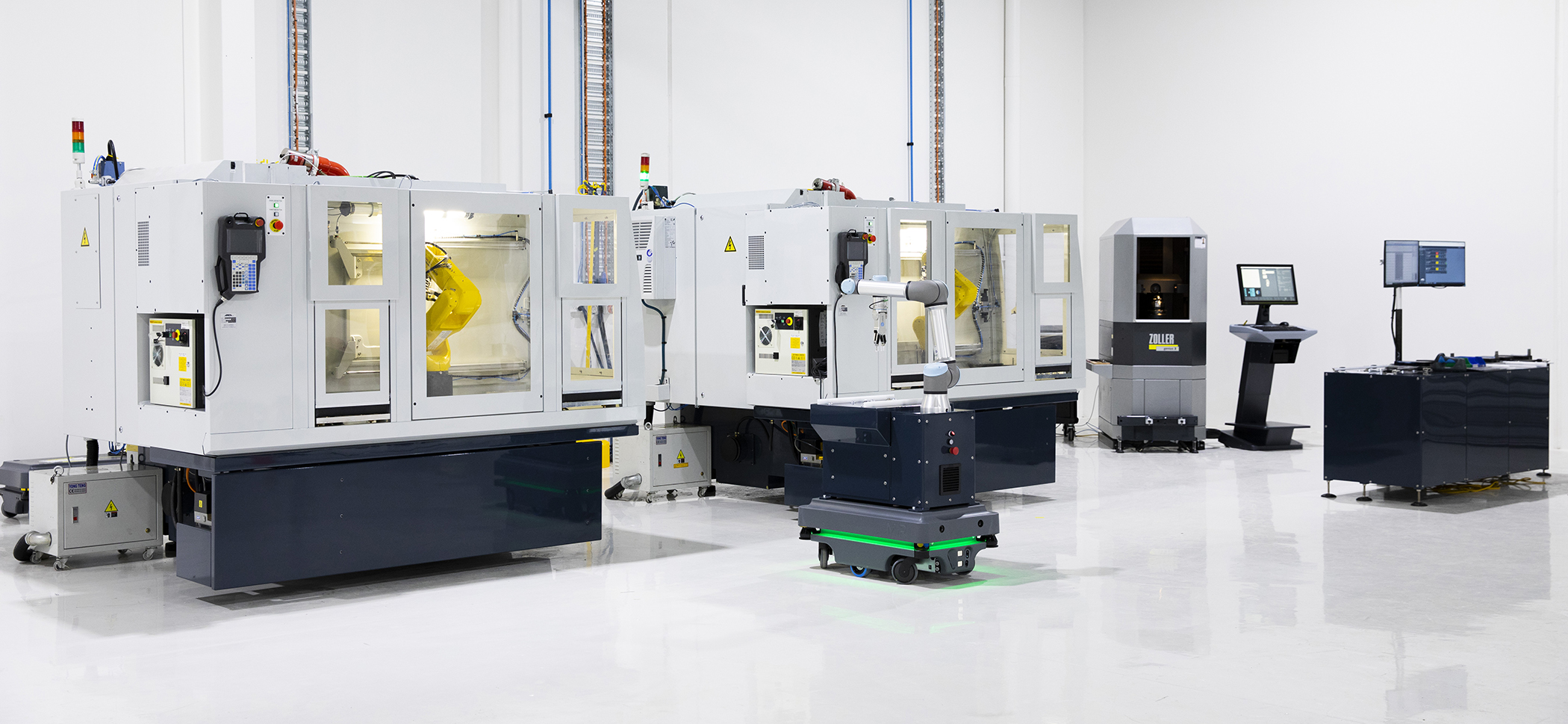
“ANCA is here to provide tool manufacturers with solutions to support production that work across all industries and applications and expand to complete tool production needs. This is a new landscape for interconnected technology, working end to end,” said Chris Hegarty, ANCA Group CEO.
“Integration and automation solutions provide infrastructure to manufacture tools with increased productivity and higher quality. ANCA has the industry-leading software and control capabilities to deliver a system for production management that tackles time, cost and labour inefficiencies where it counts.”
“We are delighted to be accelerating into the fourth industrial revolution with advanced, smart factory solutions for cutting tool makers – intelligent automation for connecting processes and data management.”
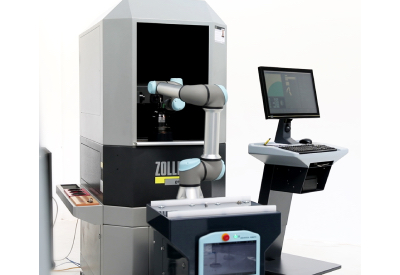
Connect, automate and create with AIMS
AIMS Project Lead, Duncan Thompson said: “Automated options that can be applied in the real world and tailored to a machine shop’s challenges, mean that tool manufacturers can reap the advantages of integrated processes and systems in a practical way.”
Over 70% of ANCA customers seek machines with robotic functionality. ANCA’s world-first technology developments utilise automation to gain efficiencies and have helped reduce production costs by 50%.
Duncan Thompson explains: “Our customers continue to look for custom solutions for increased automation in their operations and AIMS is ANCA’s holistic response; a tangible option for a smarter factory. Automation that works best is targeted to repetitive processes that can occur alongside value-adding individual skills. AIMS slots in to seamlessly automate routine processes.”
“Seeing this level of integration in action is pretty amazing. Our easy to view, virtual demonstration really highlights the ways that AIMS works to boost tool production. AIMS can be deployed to a single process or across an entire production line, towards end to end tool manufacturing.”
The AIMS online demo exhibits interconnected grinding technology solutions that eliminate wasteful manual handling, reduce machine downtime in between batches and take away the need to have operators constantly monitoring and adjusting production machines.
For complete tool production, AutoMarkX offers automated laser tool marking
The new AutoMarkX is ANCA’s tool marking solution designed particularly for the needs of cutting tool production. ANCA already has you covered with critical tool grinding processes; CPX for blank preparation, and tool grinding on ANCA’s TX, MX and FX tool and cutter grinders. AutoMarkX will work seamlessly alongside ANCA CNC grinders and automates the tool marking process, further extending unmanned production operations.
Tool manufacturers are seizing options that streamline processes and save labour costs. AutoMarkX is capable of automated pallet loading and takes care of the tool laser marking process, freeing up operators to perform more value-adding tasks. AutoMarkX is designed for integration with AIMS, being able to automatically receive and dispatch pallets from AutoFetch, while connectivity to the AIMS Server provides details of the message to be marked on the tools.
Product Manager, Jan Irzyk said: “This machine is efficient and compact – but more than that, it can be integrated with your ERP and AIMS, so that technology can work together. Removing the need for manual handling, our new laser marking solution pushes tool marking capabilities into lights-out production.”
“For full production, flexibility is important. This system accommodates a variety of tool sizes as well as mixed batches. With an easy to use interface and customisable marking, it is a complete solution that boosts labour efficiency.”
With over 45 years’ experience delivering CNC grinders to customers around the world, ANCA carries a reputation for delivering customer-focused innovations that meet market needs. Products that use smart automation for every day applications offer increased productivity and profitability. Integrated manufacturing, and machines that work together for complete tool production provide comprehensive options for manufacturers across multiple industries.
More Information
Related Story
How AIMS Improves Safety for Tool Manufacturers
The tool manufacturing industry embraces automation solutions at an unprecedented pace. This is a worldwide trend driven by several factors – labor shortage, increasing labor costs, the need for maximizing uptime, push for 24/7 machine availability and customers demanding shorter lead times. Manufacturers need to be more flexible and responsive than ever before.