Success Story: How to Extend the Life of Pneumatic Powered Tools?
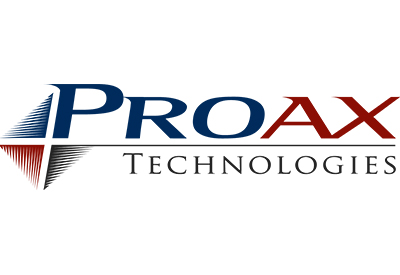
January 20, 2021
By Kevin Nguyen, Marketing & Communications, Proax Technologies
A local equipment repair facility was facing a huge problem which was costing them thousands of dollars in repairs to their own equipment and delaying projects: water in their pneumatic airlines. Fortunately for them, there was a simple solution at hand. This repair facility made use of a many pneumatic-powered air tools and machines. Their pneumatic system had a simple air compressor to supply pressurised air to their equipment. Although effective in generating compressed air, their system was inadequate in terms of effectively dealing with water and particulate contamination. This resulted in damaged air tools and machines which tranlsated into costly repairs and equipment replacement over time. The repair facility was faced with the question: “how can we extend the life of our pneumatic equipment?”
Why is there water in my pneumatic lines?
In this case, the pneumatic air power tools weren’t the problem, but the air being supplied to the equipment was. A typical air compressor works by converting electrical energy to mechanical motion (Electrical Motor), to compress atmospheric air to create pneumatic potential energy. It is this potential energy that is stored and distributed in pneumatic lines to be used to do work. As air is compressed, water and particulate always found in atmospheric air are concentrated. Through condensation water droplets form in the air system. Without proper air preparation, you run the risk of internal rusting, grease erosion, bearing seizing and clogging up machine components, making them malfunction. Many equipment repair facilities use untreated compressed air for their operations.
How to extend the life of your pneumatic powered tools?
To extend the life of pneumatic powered tools, we need to address the source of the problem: the air. For industrial applications like this particular company, the moisture generated in the pneumatic system was slowly damaging the equipment, dramatically shortening their lifespan. The solution was an air dryer.
How does air dryer work?
The air coming out of compressors is typically hot, with a lot of relative moisture. Air dryers take the incoming air and cool it down, lowering its dew point. The dew point is the temperature where water vapour condensates and creates water droplets. Dryers remove the water droplets through an auto drain. As long as the air temperature stays above the dew point (usually 3-5 deg C), condensation won’t be an issue.
Proax Technologies Recommended Solution
We suggested going with SMC’s IDFB, which had a stainless steel heat exchanger for better corrosion resistance vs a competitors model with a copper heat exchanger. With competitive pricing, a quality product offering and technical support from Proax, this was a winning combination. The repair facility ordered several sets of AFF filters to remove particulate and IDFB11E dryer units to resolve their water issues. Since being installed, water in their airlines has no longer been an issue.