Safe in the Knowledge
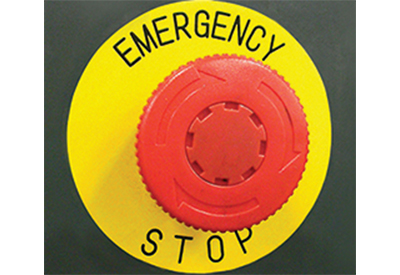
December 11, 2020
As an engineer, the responsibility to adopt not just the latest, but the safest technologies, never goes away. Protecting people and machinery has become, quite simply, industry’s number one priority. Safety first. Always.
Factory automation is certainly no exception. Here, major advances have fuelled a greater focus on smarter controls and increased integration of smart devices and safety componentry. Included in this are the latest pneumatic solutions, which nowadays form a core part of safety controls for implementing the preventative technical measures needed to ensure machine safety, including clamping, blocking, exhausting and holding equipment in place.
But hold on a moment, what actually classifies a product as a safety component? Well, as with all things related to machine safety, the best place to find out is the Machinery Directive, which states that a product is deemed to be a safety component when it is tested and verified to provide a specific safe function for a pre-determined period of time in a given state.
The Machinery Directive also offers a clear distinction between safety devices and standard pneumatic components deployed in a safety circuit. Notably, the term ‘safety component’ does not imply the actual reliability or safety level of the component. Those products offered as safety-rated must undergo stringent requirements for certification, testing, and approval. As a further point, the Machinery Directive does not prescribe the use of safety-rated componentry, it merely provides a description of the conformity assessment procedures to market a product as safety rated.
So, how is it best to determine what level of safety is required? The answer: perform a risk assessment. Three steps are involved here: analysis, evaluation, and reduction. The first step, risk analysis, also requires engineers to estimate risk and determine the performance level required (PLr).
After the PLr is established the performance level (PL) will need to be calculated based on safety categories that are established in line with factors such as a measure of diagnostic capabilities (DC) for the control system, the meantime to dangerous failure (MTTFD) and common cause failure (CCF). In combination, these inputs will define the level of a given safety function.
In tandem with the strategy set out here, peace-of-mind can, of course, be found by specifying safety-rated products from a reputable supplier. After all, as machine builders will be well aware, the price of non-compliance can be extremely costly.