Piezo Motion
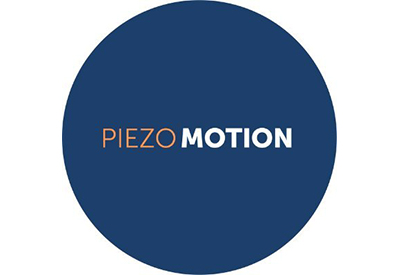
March 18, 2021
Piezo Motion is a provider of ultrasonic standing wave-type piezo motor technology. Their experience in the research and development as well as the manufacturing of piezomotors for high-tech industries across the globe is second to none. While there are several types of piezo motors on the market, the design and technology employed by Piezo Motion in its standing wave-type piezo motors is quite unique and provides certain key advantages in both use and manufacturability. Available in a variety of sizes and configurations, Piezo Motion’s full line of rotary and linear piezo motors address many of the modern-day requirements for motion control systems.
Piezo Motion’s ultrasonic piezo motors are used around the world in various applications and products within biomedicine, optics, semiconductor and nanotechnology as well as industrial electronic and automotive systems, just to name a few.
Rotary Piezoelectric Motors:
- – Direct-Drive mechanism – provides better accuracy, repeatability and resolution due to elimination of mechanical transmission/gear system. Also abolishes backlash and hysteresis
- – High torque with wide range of torques – 10-times better torque (per unit of size/mass) than any comparable stepper motor – enables high dynamic (start-stop) characteristics.
- – Low temporal drift – Angular position of the rotor is held fixed (self-braked), providing negligible angular drift (i.e. <1 arc-sec/hour)
- – High resolution & high accuracy – <1 arcsec resolution with an absolute positioning accuracy of 4 arc-secs in closed loop mode using their optional high-resolution optical encoder
- – Bidirectional angular positioning – Accuracy one order of magnitude better than the best of currently available systems due to direct-drive mechanism
Linear Piezoelectric Motors:
- – Unlimited Travel Range – limited only by length of rail used
- – Wide range of linear steps and velocities – from 5nm/sec to 1m/sec
- – High resolution and high accuracy – 5 nm resolution.
- – High push/pull force with wide range of forces – from 4 N up to 50 N
- – Simplified power requirements – controller system operates from low voltage (e.g. <12 VDC).
- – Low temporal drift – Linear position is held fixed (self-braked), providing negligible drift (i.e. < 1nm/hour)
- – Non-electromagnetic/Non- magnetic – can be made entirely from non-magnetic materials