A Box’s Journey: Understanding Palletizing from a Machine Safeguarding Perspective by Omron
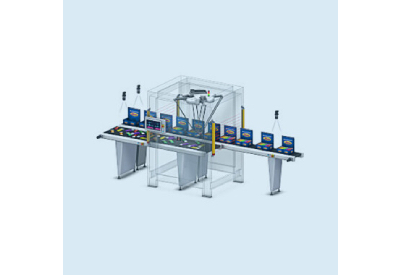
September 28, 2022
Palletizing and depalletizing machines tend to be large and have several zones of control. They must also accommodate products of numerous different shapes and sizes. These factors create challenges when safeguarding these machines.
To illustrate these challenges and the ways to overcome them, let’s follow a box on its palletizing journey – starting when it approaches the loading cell on a roller and ending when the pallet it gets incorporated into is wrapped up in clear plastic.
At each step of the way, we’ll highlight Omron machine safeguarding products to protect operators from hazardous motion.
ZONE 1: From the roller to the loading cell
We first meet the box as it approaches the loading cell on a path of rollers. Since this area of the machine has fewer moving components, it doesn’t need to be explicitly guarded, but there still needs to be a way for operators to shut the palletizing machine down if necessary.
This is accomplished using a combination of E-stops and rope pulls. Because rope pulls can be easily accessed and triggered at any point along their length, they’re an excellent choice for applications involving rollers or conveyors.
ZONE 2: Entering the loading cell of the palletizing machine
As the box enters the loading cell, we want to maintain the highest amount of guarding possible. Although the danger comes from inside the cell, the first line of defense is to prevent entry, so a major focus here is to ensure that operators don’t reach their arms into the cell.
F3SG-SR light curtain guarding is placed both above and below the rollers to prevent an operator from circumventing the safety measures by crawling below the roller. The light curtains will have programmable muting and fixed blanking activated so that only the section that the box passes through will be muted.
The muting actuator is ideal for initiating muting for a variety of targets and can even maintain muting for boxes that have holes.
- •F3SG-SR Safety Light Curtain
- •F3W-MA Muting Actuator
ZONE 3: Inside the loading cell
This part of the palletizing machine is where our box will be picked up by a strong robotic arm and placed onto its pallet. A door gives operators access to the interior of the loading cell, and the door is guarded by a non-contact door interlock. The cell’s interior uses safety scanners in opposing corners to ensure that no one is present in the interior of the cell during operation.
ZONE 4: Entering the wrapping cell of the palletizing machine
Once the box has been placed snugly on its pallet along with several other boxes, it’s time for the pallet to be wrapped. As with the entry to the loading cell, here we also need to prevent operators from reaching their arms into the cell where potentially hazardous machine motion is occurring.
The entrance to the wrapper will also feature light curtains that guard from above and below, but this time we’ll have the muting done by a sensor instead of an actuator. (For objects that have simple shapes, like our box, sensors and actuators work equally well for muting purposes.)
ZONE 5: Inside the wrapping cell
The wrapper’s interior features a giant roll of shrink wrap. Either this roll will be moved around the pallet to wrap it, or the pallet will get spun on its axis to cover itself with the wrapping. Whichever way is chosen, the result will be a very tight clear plastic wrapping.
This cell would be an extremely dangerous spot for a human to be while wrapping happens, so it must be monitored in entirety by safety scanners. There are two ways to do this: 1) having two safety scanners in opposite corners looking inwards toward the cell, or 2) raising the cell and having two safety scanners sitting under its center looking outwards.
Once our box has been loaded on the pallet and the pallet has been wrapped, it’s ready to be shipped! Thanks to the appropriate types of machine safeguarding at each stage, the process has been completed safely and smoothly.
Interested in learning more about our machine safeguarding technologies? Click here