OTTO Motors 2.26 Software Release: Move Materials Faster in Your Manufacturing Facility
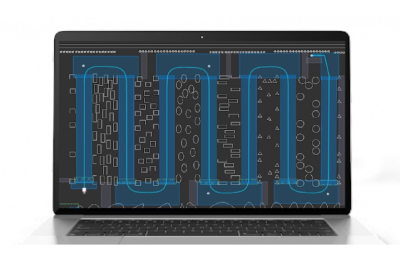
October 11, 2022
Manufacturing organizations are accelerating their adoption of autonomous mobile robots (AMRs) to effectively tackle labor challenges. They are using AMRs to carry out tedious and dangerous material handling tasks while their workers handle more fulfilling and specialized jobs. As manufacturers look to deploy autonomous solutions in critical 24/7 operations, they want solutions that are safe, scalable and provide a high ROI.
To solve these challenges, OTTO Motors is continuing to invest in software upgrades with the release of software version 2.26, available to all new and existing customers. A critical element of the OTTO AMR solution is its industry leading robot driving and fleet management software.
Table of Contents
2.26 Features for Performance Augmentation
1 Faster and more predictable path planning with Graph-Based Planner
2 Higher average speed with Ground Segmentation
3 Consistent tracking of objects and localization improvements with Dynamic Obstacle Tracker
2.26 User Experience Enhancements
4 Quicker and easier robot localization
5 Improved troubleshooting with 3D camera data in snapshots
6 Build complex robot workflows without any coding
Below is a breakdown of some of the most exciting and valuable features in the new 2.26 software release (OTTO customers, if you’d like to access the release notes then click here).
2.26 Features for Performance Augmentation
1. Faster and more predictable path planning with Graph-Based Planner
The latest software release makes significant enhancements to the robot path planning method, which is one of the most critical aspects in ensuring safety and productivity of AMR deployments. Up until now, we have used Search-Based Planner (SBPL) which has enabled OTTO AMRs to make their own paths from start to destination taking into account parts of the map that are not explicitly excluded. While SBPL provides flexibility to prevent blockages and deadlocks, it also increases planning time.
To enable faster and more predictable path planning, OTTO Motors is introducing a Graph-Based Planner (GBPL) that allows customers to specify lanes and junctions to restrict normal path planning to only the segments that customers want the robots to use. Instead of starting from scratch at the beginning of every movement, GBPL creates a network of paths, or a ‘graph’, throughout the map during the map creation and distribution process.
It is important to note that the robot is not restricted to only using the Graph-based Planner. It is free to attach and detach as necessary to circumnavigate obstacles. Users can enable Graph-based Planner (GBPL) simply by adding GBPL features to their map such as graph lanes.
Graph-Based Planner delivers faster planning times, more reliable and repeatable paths, resulting in lower takt times and higher ROI for the customers.
Our experts breakdown the benefits of GBPL below:
a. Faster and more predictable path planning
To highlight the differences in performance, we created a simulated environment to compare them.
Video 1.0 SBPL vs GBPL side by side comparison https://share.vidyard.com/watch/J1sKrN55taFtRP4bFDbVbA?
In the video 1.0 above, on the left side is the scenario where the robot uses SBPL and on the right side it uses GBPL. In the SBPL video, you can see that the robot acts greedily and cuts through the aisle. In the final move, SBPL requires the OTTO 100 to reverse into a tight space. OTTO 100 heavily favors moving forward-based on its hardware design but the current Search-based Planner (SBPL) does not take that into account properly. As a result of which, the robot fails to complete the job.
In the video with GBPL, at first glance it may appear that it is following a longer route which is counterintuitive to it being a faster path. But it becomes clear that GBPL lays down the right rules and path for the robot to successfully complete the job, in less time. It tells the robot what to do rather than what not to do and adds predictability (where the user wants it) while getting the job done.
For further clarity on how GBPL works and makes robot path planning better, please listen to the video 2.0 below from our experts at OTTO motors.
Video 2.0 See how OTTO can plan routes faster in a simulated environment using GBPL https://share.vidyard.com/watch/dxvz9nPzBWorFV4pNgSbqw?
b. Robot creates smoother, more reliable, and repeatable intersection interactions
Image 1.0 is a snapshot of junctions and lanes from the OTTO Fleet Manager created by the GBPL and Image 2.0 is the resultant graph. As you can see, multiple lanes coming together in a junction can be automatically transformed into traffic circles for efficiency. Instead of using lanes for long traversals of a facility, they are used as portals into and out of junction zones, resulting in much smoother intersection traffic.
c. Graph-Based Planner creates unique graphs for different robot types to enable faster routes
Each OTTO robot is unique in its capabilities, size, shape and dynamics, which should be the driving factor in how it plans the path in your facility. Graph-Based Planner enables each robot to achieve this by allowing them to generate a unique graph, on the same route, that is customized for their robot type. This enables the robots to build the most optimized route and reach their destination in the fastest manner possible.
In Image 3.0, you will see the base map, which represents the end of two aisles (lanes) in a warehouse, meeting at a junction.
In Image 4.0 below, you can see two different robot types producing different graphs, indicated by light blue lines, unique to their capabilities, optimized for performance. While a curved path is planned for OTTO 100, note the 90 corner for the OTTO 1500 V1.2 which denotes a turn in place. The older OTTO 1500 V1.2 hardware version is not as fast when attempting to drive forward and turn at the same time so the path has been automatically optimized for more straight line driving.
2. Better and faster obstacle detection with Ground Segmentation
Ground segmentation, a 3D detection feature that allows OTTO robots to differentiate ground from non-ground parts, makes OTTO smarter at detecting smaller objects from a distance and therefore, allows them to maneuver swiftly and smoothly around the obstacle rather than stopping.
OTTO Motors first brought 3D Obstacle Detection to its product line via the introduction of Intel Realsense technology. The Realsense unit projects a grid of points in InfraRed (IR) and uses two IR cameras slightly physically offset to detect how that grid overlays the physical environment. Comparing the two data streams and using stereoscopic depth estimation, the system is able to perceive the surrounding environment in three dimensions.
Video 3.0 OTTO 1500 going around obstacle at Sunview Patio Doors https://share.vidyard.com/watch/M5fv2jKagwYeaxAqaaFYCU?
While 3D obstacle detection was a huge step forward from a simpler 2D planar LiDAR, its initial implementation was limited by the onboard computing power available at the time of the earlier models. OTTO Motors has been continuously working on making this available to our customers for being able to detect smaller objects.
While we were able to add ground segmentation processing to the OTTO 100 without personal computing (PC) changes, we introduced Graphics Processing Unit (GPU) on OTTO 1500 and OTTO Lifter to provide this capability across all our AMRs. Ground Segmentation uses the video feed to determine where the floor is within the IR data stream. Using this knowledge, the detection thresholds have been reduced making it possible to detect smaller objects resting on the floor.
3. Consistent tracking of objects and localization improvements with Dynamic Obstacle Tracker
Dynamic Object Tracking serves two purposes. First it allows for an estimation of an object’s velocity, which means the robot can understand if it will cross paths with the object and make course corrections. Second, a dynamic object can be excluded from the localization process, improving the quality of the algorithm.
In the 2.26 software version, incremental improvements have been included in the Dynamic Obstacle Tracker thanks to optimization of feedback within the algorithm and improved ability to maintain tracking of dynamic objects over time.
The result is a more consistent tracking of objects, less error in velocity measurements, better tracking of objects if they stop temporarily, and overall localization improvements.
2.26 User Experience Enhancements
4. Quicker and easier robot localization
In 2.26, we are introducing a new UI for re-localizing the robots if they get lost. This is much simpler than the older interface and can be completed in seconds. This capability is present in both OTTO App and in OTTO Fleet Manager.
If a robot is relocated while powered down, it would very likely be unable to localize upon reconnection with OTTO Fleet Manager. In order to recover from this scenario, the user is required to localize the robot. In the past, this process required guesses and checks.
In 2.26, the user is offered two improved options: Automatic Localization and Manual Localization.
a. Automatic Localization triggers a facility wide search for locations that result in a high localization score for the robot. The results are near instantaneous and require no input from the user.
Video 4.0 Automatic Localization
b. Manual Localization is sometimes required due to a very large, repetitive facility environment and the user experience has been greatly improved here too. Now, as the user adjusts the robot’s position, the scan data is displayed live. The user can easily move and rotate the robot throughout the map and make an informed decision on where to place it.
Video 5.0 Manual Localization
5. Improve troubleshooting with 3D camera data in snapshots
When robots get erroneously blocked or safety stopped by artifacts in the RealSense camera feed, customers can now collect “video bags” and send them to OTTO customer support so that we can help you resolve the issue. This enables customers to get the safety benefits of the cameras without performance impact.
OTTO Motors has created the ability to include video snippets within the snapshot process. In order to ensure that this feature is 100% opt-in, two steps are required.
A custom robot configuration is needed to enable the necessary data recording onboard the robot.
For each snapshot the user must select “Include advanced diagnostics”.
While OTTO endeavors to provide this troubleshooting feature to all customers, it may be restricted without warning based on backend infrastructure availability.
6. Build complex robot workflows without any coding
Using Blockly, OTTO now has a visual way to program workflow logic. It allows customers without computer science backgrounds to build complex workflows that sequence steps, specify precise driving instructions, use conditional and boolean logic to decide if a step should be taken, and react to external stimuli from the robot sensors.
Note: this feature is experimental. We encourage you to try this out with robots not running production jobs and share feedback with OTTO so that we can improve the feature and ultimately bring it to general availability
Call today to upgrade your OTTO AMRs
If you are an existing customer and want further details on what the 2.26 software release entails, check out the release notes or contact your Customer Support Representative at support@ottomotors.com for the upgrade.