Easy Quick-Change of Gripper Fingers During the Ongoing Process
March 56, 2024
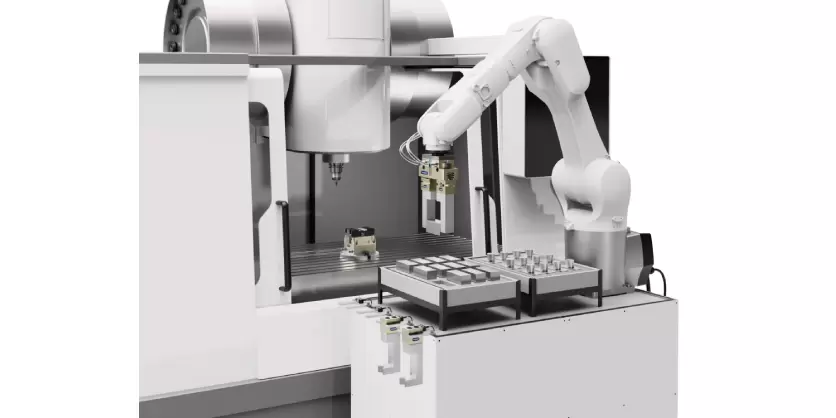
The new BSWS-R jaw quick-change system, SCHUNK enables automatic finger change during the ongoing process
With the new BSWS-R jaw quick-change system, SCHUNK enables automatic finger change during the ongoing process. The cleverly designed system consists of just a few components and is compatible with all grippers with PGN-plus-P screw connection diagram. The BSWS-R is the next stage of evolution of the BSWS series from SCHUNK
In many industries, production is increasingly moving towards high mix, low volume. It is becoming a major advantage for companies to be able to produce a wide range of variants, even in the smallest batch sizes, without needing any manual set-up work. This flexibility is now made possible by the BSWS-R jaw quick-change system. With the latest evolutionary stage of the BSWS series, robots can change their gripper fingers automatically during the ongoing process – in less than three seconds!
Simple structure, easy application, more freedom
Up to now, automated changing has only been possible by replacing the entire gripper. The BSWS-R accomplishes this task with minimal use of components: all that is needed for each gripper finger is a jaw quick-change base, two adapter pins and a storage station. The base is screwed to the workpiece-specific gripper finger and the adapter pins are attached to the base jaw of the gripper. When the base moves into the storage station, the locking pin is actuated, and the form-fit locking mechanism is unlocked.
The robot moves upwards out of the jaw quick-change system, and the fingers and the base remain in the storage station. No additional effort is required as the robot performs the change with its own force. The new system design eliminates the need to drill through the finger, and only threaded holes are required. This gives users even more freedom when designing their fingers.
Process reliability thanks to presence monitoring
The BSWS-R is available in nine sizes. In smaller versions up to size 100, the storage stations are designed with elastomer bearings and makes them ideal for applications with cobots. For even greater process reliability, an optional inductive proximity switch is available to control whether the finger is in the storage station. The base is also prepared for installation of an RFID data carrier for finger coding. In addition to the new BSWS-R, the two manual change systems of the series will continue to be available. With the proven BSWS, the operator changes the finger simply with a Allen key, with the BSWS-M at the push of a button.
More Information
Related Story
Key to the Comprehensive SCHUNK Chuck Jaw Portfolio
With new adapter jaws, SCHUNK has established compatibility between machine vises and the world’s broadest portfolio of top jaws from SCHUNK/GRESSEL. These useful connecting elements offer new and flexible clamping options for any machining task