Beckhoff Optimizes Linear Motion with Machine Learning Solution that Eliminates Cogging
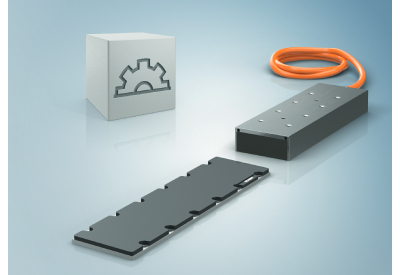
June 21, 2022
The highly dynamic AL8000 linear motors from Beckhoff now meet even greater requirements for accuracy and synchronization with the new TwinCAT Cogging Compensation software. This makes the linear motors particularly suitable for high-precision applications such as milling machines or laser cutting machines. The cogging compensation software makes use of machine learning, which is seamlessly integrated into TwinCAT and applied on a fully automated basis (Engineering TE5920, Runtime TF5920).
Cogging forces in linear motors are caused by the magnetic attraction between the iron core in the primary part and the permanent magnets in the secondary part. This physical effect leads to an unwanted and uneven “cogging” of the motor, meaning that applications with extremely high accuracy and synchronization requirements can only be executed to a limited extent. This is where the AL8000 linear motors in combination with the TwinCAT Cogging Compensation software offer an ideal solution: the cogging forces are reliably compensated with the help of this software, which accounts not only for magnetic effects but also factors related to mechanical design or energy chains. As a result, the range of possible applications for the AL8000 iron-core linear motors is significantly expanded.
Cogging compensation is based on the fully automated application of machine learning in TwinCAT. The software independently records the necessary cogging data in the respective customer application as part of a reference run over the entire length of the linear motor’s magnetic track. With the help of the data acquired, the software trains a neural network, which ultimately integrates into the control system for current pre-control. Adapting the current pre-control in this way can reduce the lag error by up to a factor of 7 and increase synchronization of the machine by up to a factor of 5 without any hardware changes to the AL8000.
To learn more about the TwinCAT Cogging Compensation (TE5920) from Beckhoff, click here