EtherCAT in Boost Mode
May 14, 2025
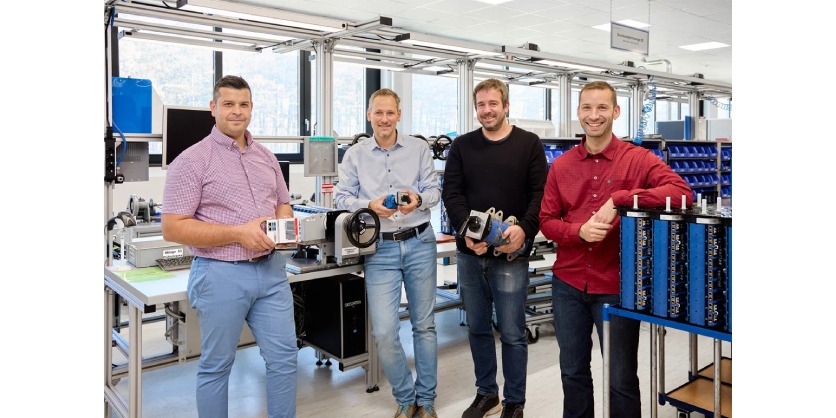
EtherCAT and PC-based control in test bench technology
EtherCAT is by far the fastest Industrial Ethernet technology. Nevertheless, the data acquisition process at Kraus & Naimer’s cam controller test benches called for an even shorter bus cycle. To achieve the required performance, Beckhoff specialists reduced the previous cycle time from 100 µs to 20 µs.
With over 118 years of experience, Kraus & Naimer is a recognized specialist in switches and cam controllers. In addition to its extensive range of standard switches, the company provides customized solutions for various applications with up to 96 contacts and customer-specific contact configurations. “Our ability to deliver such specialized cam controllers starting from a lot size of one is all part of what sets Kraus & Naimer apart,” emphasizes Christoph Halbertschlager, Head of Product Data Management and Marketing at Kraus & Naimer.
Around 8,000 switches are manufactured every day at Kraus & Naimer’s largest production facility in Weikersdorf, ranging from compact control switches and load-break switches with dozens of contacts to large units for use in power plants and energy distribution systems.
Every single switch undergoes thorough testing with documented results, and that includes the many custom variants on offer. The test process involves placing the switch into the fixture, pneumatically engaging the test probes onto the contacts with a foot pedal, and moving through the various switch positions via a handle equipped with an integrated encoder. The signal curves and rotational angles are recorded with high precision during the switching process. “High-resolution recording of multiple inputs and outputs is crucial for precise testing of switching operations with respect to timing and angular position,” notes Ibrahim Podrimja, Head of Automation Technology at Kraus & Naimer in Weikersdorf.
Fast signal acquisition with standard components
Signals are recorded using a CX2043 Embedded PC, eight EL1018 digital input terminals (8-channel) with fast input filtering, and 26 EL2202 digital output terminals with distributed clock function for rapid signal output. The switch position during operation is detected with a resolution of 1° using an EL5001 EtherCAT Terminal – an SSI master with distributed clocks function. Up to 24 switch positions are possible depending on the switch configuration. With the current configuration, Kraus & Naimer can test up to 48 contacts (24 contact pairs).
The challenge during the test was to record the switching pattern quickly and accurately during actuation. “We set very tight tolerance ranges in which a contact must open or close,” explains Gerald Platzkammer, Electrical Design and Software Development at Kraus & Naimer. To achieve the high temporal resolution required, the team worked on exploring solutions together with the specialists at Beckhoff.
eXtreme Fast Control or faster bus cycle?
At the beginning of the project, the team considered implementing the high temporal resolution requirements with eXtreme Fast Control Technology (XFC). While assigning inputs and outputs via precise timestamps was technically feasible, it would have added complexity to the evaluation process in this case. “It was much more effective to reduce the EtherCAT cycle time to 20 µs,” explains David Kittl, sales representative, Beckhoff Austria. Two bus cycles were used to set the outputs and read back the inputs. “Reducing the cycle time further would have made it impossible to clearly assign inputs and outputs,” adds Gerald Platzkammer.
In its current configuration, the CX2043 Embedded PC records around 830,000 bits for 48 contacts via EtherCAT during each test. In the fully expanded configuration for 92 contacts, this figure rises to around 3,000,000 bits. The data is transferred as an array to the evaluation program, where it is compared with the target switching program and switching sequence. The C#-based evaluation program retrieves data from the control program via ADS and accesses order-specific switching programs from the ERP system and various databases through web services.
“A major advantage of PC-based control is that we can continue to run our software on the Beckhoff control system with minimal adaptation effort,” says Rainer Fraunschiel, a developer specializing in software implementations for automation solutions. This enabled Kraus & Naimer to eliminate the need for an additional PC as an interface between the ERP system and the controller. “Thanks to the fast bus cycles and PC-based control, the entire electrical test still takes no longer than 2 seconds,” adds Ibrahim Podrimja. At the end of the process, a test report is stored in a database together with the target/actual comparison of the switching patterns for each individual switch.
PC-based control replaces separate measurement technology
Before switching to Beckhoff as its automation supplier, Kraus & Naimer used a separate measurement technology computer with custom-designed plug-in cards. The move to PC-based control technology allowed the company to cut down on equipment significantly. “Eliminating the need for an additional PC has allowed us to save both space and costs,” explains Ibrahim Podrimja. “We’ve also become more independent by using Beckhoff’s standard components.” He goes on to highlight the comprehensive product portfolio, strong support, and solution-oriented approach of the sales team, which continues to provide valuable assistance for future projects.
The switch to TwinCAT 3 and Structured Text as the programming language provided further advantages. “We were able to make the control program more intelligent and add features that would have been very difficult to implement before,” notes Gerald Platzkammer. The open architecture of PC-based control allows for the use of any visualization solution when needed, alongside TwinCAT HMI. Another major advantage of TwinCAT, according to Ibrahim Podrimja, is the widespread use of TwinCAT 3, “Many vocational students learn to program with TwinCAT 3 during their training and are already familiar with PC-based control when we hire them as control engineers.”
He also points out that having software documentation and functional descriptions available in German is another significant benefit.
More projects in the pipeline
Parallel to the ongoing projects in assembly automation, cooperation in the testing technology sector is starting with the manual high-end test bench. Plans are in place for additional test stations to be used at Kraus & Naimer’s production facilities around the world, while existing fully automated test benches are set to receive Beckhoff control system upgrades. Since the start of the collaboration in fall 2023, four other projects have been implemented in parallel to the test stations, with a new assembly automation system currently in the planning stage. “Beckhoff’s approach and company size make it the perfect fit for us,” concludes Ibrahim Podrimja.
More Information
Related Story
Beckhoff Nominated for Best of Industry Award 2024
Beckhoff is delighted to announce that they has been nominated for the Best of Industry Award 2024 in the Artificial Intelligence category. This prestigious award, presented by the Vogel Communications Group, honors outstanding innovations in the industry.