MiS210/MiS250 Enhanced Motion Safety, Decentralised Flexibility, Ethernet Connectivity
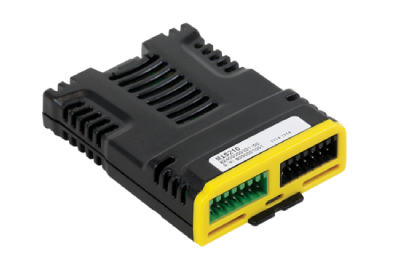
January 12, 2022
Relying on a centralised safety PLC can mean additional cost through complexity of the wiring and safety software. Alternatively, electromechanical safety devices typically mean lower throughput, longer machine stoppages and extra time required for set-up and maintenance. The new MiS210/MiS250 safety option for Unidrive/Digitax extends the built-in STO with motion safety capability and enables decentralised flexibility with the option of safety over ethernet connectivity.
Supported motion safety functions
- Safe Stop 1 (SS1)
- Safe Stop 2 (SS2)
- Safe Operating Stop (SOS)
- Safe Brake Control (SBC)
- Safe Direction (SDI)
- Safely Limited Speed (SLS)
- Safely Limited Acceleration (SLA)
- Safely Limited Position (SLP)
- Safe Speed Monitor (SSM)
- Safe Emergency Stop (SES)
- Safe Two-Handed Control
Safety over ethernet
- Supports CIP Safety over EtherNet/IP
- Supports Safety over EtherCAT (FSoE)
Safety certifications
MiS210 and MiS250 have been independently assessed by TUV Rheinland to meet the following standards:
- IEC 61508 SIL3
- IEC 62061
- ISO 13849-1 PLe
- IEC 61800-5-2
- European Machinery Directive 2006/42/EC
Fast and simple set-up
The MiS210/MiS250 customer fit option module simply clicks into place, with no screws or other mounting requirements.
Once fitted, the safety functions are seamlessly incorporated into the drive’s feature set.
- Easy configuration with Connect, the free drive management PC tool for CT drives
- Simple parametric interface
- No code to write nor new programming language to learn
Decentralised motion safety flexibility
MiS210/MiS250 enables motion safety decentralisation in combination with the appropriate encoder. This can remove the need for a central safety PLC and reduce the number of sensors necessary to achieve the required SIL/PL level.
Benefits of integrated safety include:
- Reduced wiring and costs
- Ease and speed of commissioning
- Speed of actuation thanks to close coupling of safety function and drive
- Reduced footprint and cabinet size
- Scalable SIL through choice of encoders – up to SIL 3 with a single, motor-mounted encoder
- SISTEMA library integration
- Incrementally add safety functionality
Learn more about the MiS210.MiS250, click here