Festo AX: Breakthrough AI-Based Automation Software that Optimizes Machine and Process Performance, Uptime
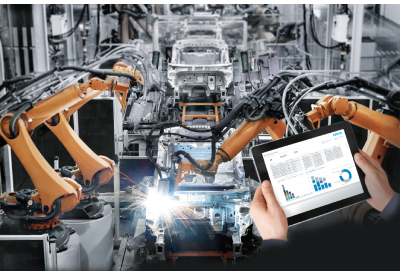
October 26, 2022
A (very) early warning tool for maintenance, Festo AX also helps improve energy efficiency, product quality
Festo introduces the Festo Automation Experience (Festo AX), a new machine learning and artificial intelligence (AI) software platform for manufacturing and process systems to ensure maximum uptime of key production assets. Additionally, Festo AX can automate quality assurance and energy monitoring that can reduce material and energy waste. Festo AX gives end users an easy-to-use tool to thrive in a tight labor market and original equipment manufacturers (OEMs) a unique capability to differentiate their machines.
Festo AX is a monitoring and maintenance management tool that extracts maximum value from machine and process data. That data is sent direcTtly to Festo AX and immediately processed by algorithms for real-time analytics. When data deviates from the “healthy state” of the asset, operating personnel can be immediately alerted via notification message sent to computer, tablet, and/or smart phone. Notifications can state in clear, easy-to-comprehend language which components are involved and the issue. Notifications can provide the recommended corrective action, again in clear and easily understood language.
Festo finds that employing Festo AX can improve process transparency by 100%. It can lower waste by more than 50% and product rejection costs by more than 45%. Machine availability can improve by more than 25%. Unplanned downtime can fall by more than 20%.
Early detection of anomalies also gives personnel time to secure replacement components. Corrective action can then be taken during regularly scheduled maintenance. The same process of learning the asset’s healthy state and anomaly detection is used to maintain high quality products and minimize energy waste. These features add up to a healthier and more productive plant, whatever it produces, from chemicals to auto parts to baked goods.
In a predictive quality application for silicon wafers production, Festo AX provided early detection of wafer defects. It improved accuracy for quality assurance sample selection and delivered high positivity in quality observations. Festo AX lowered waste per machine per year by $100,000.
At a premium-segment auto plant producing 1,000 cars per day, Festo AX continuously monitored actuation data from the plant’s welding guns. Festo AX is credited with decreasing unplanned downtime by 25% at the plant.
A US autobody parts manufacturer uses it to find anomalies in the pneumatic clamping for sheet metal bending and stamping. If the clamp is not right, the quality of the finished parts is not quite right, and they could be rejected by the customer. Festo AX functions as an early warning system to maintain proper clamping and quality.
Subscription-based Festo AX is compatible with Festo and third-party components and machines. It can reside directly on the system (on-edge), on servers, or in the cloud. Connecting Festo AX to the Festo Smartenance maintenance manager or another maintenance management or spare parts management system creates integrated end-to-end solutions from the application to the business process. Festo technicians working individually with end users and OEMs speed startup and ensure that every AX installation is serving to improve maintenance processes and operational performance, including product quality where applicable, while lowering material and energy waste.
Visit Festo Automation Experience – Festo AX – for more information and www.festo.com for the full range of Festo automation solutions.