Will a Robot or Cobot Work for Your Small to Medium Shop?
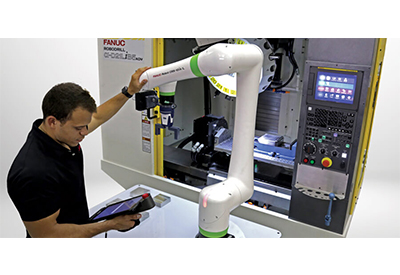
October 13, 2021
Today, small and large manufacturing plants in North America are ramping up production, and many are considering using robots for the first time. Why now? Some shop owners are having a difficult time finding skilled workers, and others who already have a full staff continue to look for ways to keep social distance measures in place and meet increasing customer demands. Whatever the situation, a production manager must first ensure a safe work environment. If the plans call for traditional industrial robots, there’s safety fencing and sensing devices to consider along with robot software to prevent contact with people (better known as speed and separation monitoring). Another great option to consider is a cobot or collaborative robot, which is power and force limiting by design. Either type of robot can be highly effective for part transfer and machine tending, as long as everyone involved follows the proper safety protocols, and the robot meets your payload and speed requirements.
How do you decide what type of robot will work best for your shop?
Standard industrial robots can operate near workers as long as the appropriate sensing hardware is used. Traditional robots are typically the best choice when people only need to access the work cell infrequently – perhaps just every few hours to reload raw materials or check critical part features. Cobots on the other hand, such as FANUC’s latest CRX Collaborative robot are ideal for working alongside people to assist with the dull, dirty and dangerous jobs while the operator is there to perform tasks that require human skills.
Whatever choice you make, robots and cobots have come a long way in the last decade. Gone are the need for huge conveyors and fixed guarding that take up a big chunk of floor space. In most cases, today’s robots are able to locate parts from any orientation – often with the help of 2D or 3D robot vision, such as FANUC’s integrated iRVision. Vision enables the robot to pick randomly oriented parts from a bin, tote, or any type of container. Once the part is picked, the robot can reorient it as needed, and quickly load it to any type of work holding device. When that portion of the operation is complete, the robot transfers the part to the next task.
Another flexible robot solution designed to help manufacturers deal with capacity shortfalls and labor shortages is mounting a robot to a mobile platform – much like Acieta’s FastLoad CX1000. This type of mobile robot solution makes it easy for one worker to move the robot to different machines around the plant floor and quickly set it up for any number of tasks – a huge benefit that allows companies to meet their customers’ demands, and save time and money.
Cobots on the other hand, such as FANUC’s latest CRX Collaborative robot are ideal for working alongside people to assist with the dull, dirty and dangerous jobs while the operator is there to perform tasks that require human skills.
Even though today’s robots and cobots improve throughput, increase flexibility to tackle multiple operations, and reduce operating costs, there’s still a wide gap between machine tools that are being ordered and those that are automated with robots. The term “lights out” has been a far-reaching goal for some manufacturers – at least for a portion of their production operations. Typically, robots are used for large batch/high-volume runs at night with less people, while the small batch/low-volume jobs are processed during the day with more staff available. In the last few years; however, there’s a growing number of robotic solutions able to handle the low volume, high-mix work that is typical in smaller companies. In these cases, the robot handles different sized parts in a family or group of parts, allowing for fast changeover when the parts change. This technology continues to improve.
Robotic machine tending has revolutionized manufacturing, allowing companies to increase their overall equipment effectiveness. Once the robot loads a machine, it can perform secondary processes like deburring, cleaning, inspection and much more utilizing the same gripper or a quick tool changer if needed.