What is an Automated Guided Vehicle (AGV)?
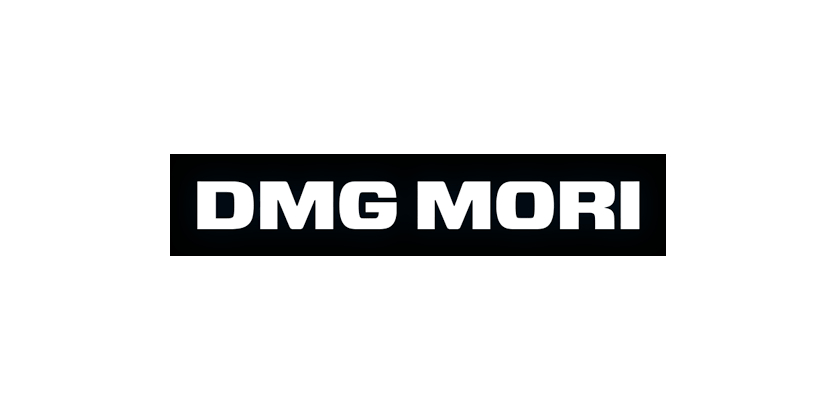
February 13, 2023
For many years, the manufacturing industry has been investing in ever new ways to automate its processes. Whereas 20 years ago autonomous manufacturing solutions were reserved in particular for high-volume parts, today the market offers a wide range of applications even for small batch sizes and products with many variants. The decisive factor for continuous operation of these flexible automation solutions is a constant material flow. Since the material storages and tool magazines of machine tools are limited for spatial and technological reasons, external storages are increasingly coming into play. These can be conveniently loaded and also expanded as needed. Driverless transport systems, so-called automated guided vehicles (AGV), play a decisive role in the decoupling of machine tools and storage solutions.
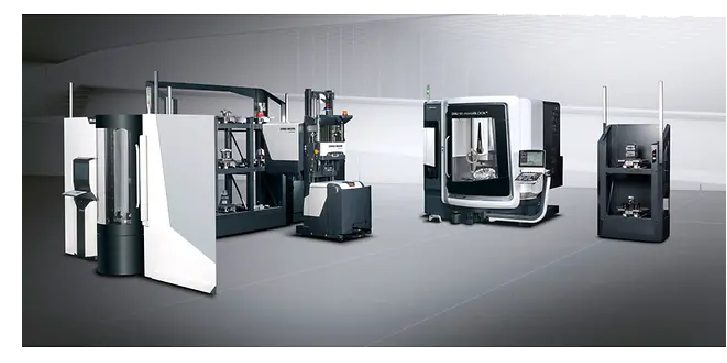
The first driverless transport vehicles were already in use in the 1970s – mainly for transporting materials from the warehouse to a workstation. From this, automated guided vehicles have developed to this day, which not only move material from A to B, but also bring parts into the machine’s working area. This is done via pre-equipped pallets or with the help of robots on the AGV, which also clamp individual components. Finished parts are automatically removed and, if necessary, taken to the next workstation for further process steps. In a similar way, automated guided vehicles can support tool management. Central tool storage systems are a solution wherever a large number of tools is required due to component variety or wear. Driverless transport systems take over the tool supply completely autonomously – up to the automatic change into the tool magazine of the machine.
Safe navigation on existing routes
Since automated guided vehicles move on the store floor, where personnel are also on the move, safety has a high priority in development. Modern AGVs are equipped with laser scanners and sensors that allow independent navigation without guideways. Thus, the layout is not subject to major constraints. automated guided vehicles use the same paths as humans. Their scanners and sensors ensure safe operation by adapting their speed to the environment – even coming to an immediate stop in the event of sudden obstacles. AI-powered methods are also already being used to help AGVs analyze the environment and optimize travel paths. In this way, for example, an Autonomous Mobile Robot (AMR), the latest generation of driverless transport systems, can autonomously avoid obstacles. The fact that no guideways are required has another advantage: automated guided vehicles are easily scalable with the number of vehicles and transfer stations.
Automated guided vehicles as an integral part of digitization on the store floor
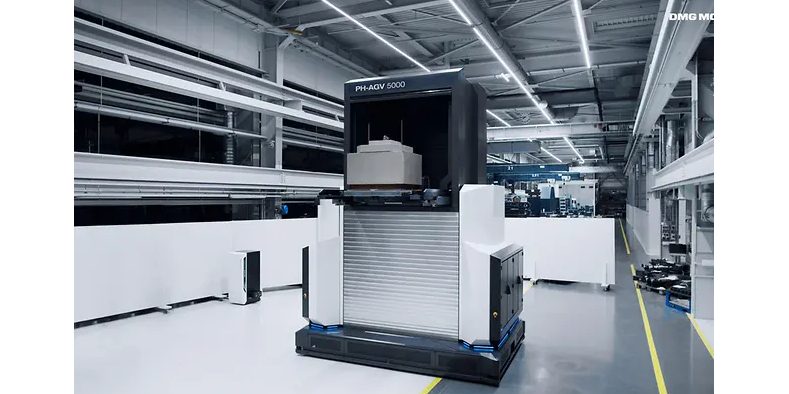
large pallets with a total weight up to 5000 kg
The introduction of AGV is a holistic approach to the automation of production processes. The focus is no longer solely on autonomous manufacturing on the machine. Automated guided vehicles involve the entire store floor. Their efficient use therefore requires good organization and planning of the production processes. In the context of digitization, for example, automated guided vehicles are perfectly suited for intelligent networking with production. This means that if production is subject to a certain dynamic due to incoming orders or material flows, AGVs are optimally integrated. Such fully digitized processes relieve workers who in the past transported the material with manual lift trucks or forklifts and also brought it into the machines. Today, they have more time available for more demanding tasks such as work preparation and programming.
Holistic Automated Guided Vehicles Portfolio for Automation solutions from a single source
With intelligent networking and the use of AGV, companies can sustainably increase the productivity and efficiency of their production. The decisive factor here is choosing the right products. The range of parts to be processed, for example, determines whether the automated guided vehicle should transport pallets or clamp and unclamp workpieces directly by robot. These and other considerations show that the topic requires thorough preparation. As a pioneer in the automation and digitization of machine tool manufacturing, DMG MORI has also actively promoted the development of automated guided vehicles and is available to its customers with advice and support in this regard.
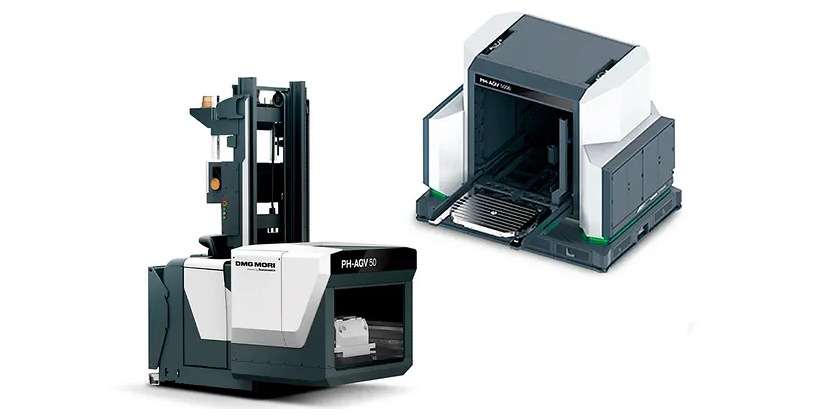
of numerous DMG MORI machine tools
The portfolio includes the PH‑AGV series for handling pallets up to 1,600 x 1,250 mm and 5,000 kg total weight. The flexible layout design of the PH‑AGV models comes into its own exactly where there is not enough space for a larger linear pallet pool (LPP). The WH-AMR, on the other hand, is an AGV equipped with a robot for direct tool handling. This is done with a positioning accuracy of +/- 1 mm. This ensures both precise clamping of the blanks in the chuck and reliable removal of the finished components. In addition, the WH-AMR is capable of overcoming 35 mm high cable ducts and independently bypassing obstacles. With its compact design, the WH-AMR requires little more space than a human, while the radar scanner enables safe operation without fences.
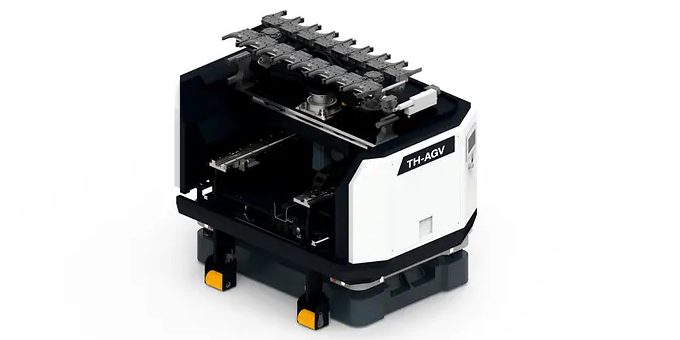
weighing maximum of 39 kg each, on the store floor
The TH-AGV strengthens the product range in the area of tool management. It transports up to 16 tools, each weighing a maximum of 30 kg, on the store floor. Thanks to an interface to the tool loading station of the DMG MORI wheel magazine, the TH-AGV can independently feed the tools into the machine. A central tool storage, the CTS (Central Tool Storage) serves as the basis for automated tool supply. Up to 1,440 (ISO 40) or 960 (ISO 50) tools can be stored here.
The automated guided vehicles are operated by means of the DMG MORI MCC-LPS 4 master computer, which DMG MORI successfully uses to optimize the entire production process. In other words: Customers who want to automate their production holistically can get everything from a single source at DMG MORI.