ELM72xx Series from Beckhoff Offers Compact Drive Technology in Robust Metal Housings
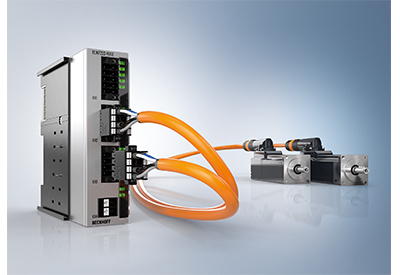
December 10, 2020
The new ELM72xx EtherCAT Terminals are fully functional servo drives in robust metal housings that deliver an output current (Irms) of up to 16 A at 48 V DC for the power supply. They expand the Beckhoff portfolio of compact drive technology in I/O terminal format and offer all of the current technology features together with increased performance and functionality compared with comparable EL series I/O designs.
The ELM72xx modules’ metal housings provide optimum heat dissipation even at high output power as well as optimal shielding against electrical interference. The new servo terminals can connect directly to other EtherCAT Terminals as an integrated component of the Beckhoff I/O system. The comprehensive functionality includes the direct connection of the motor, feedback and brake via the convenient connector front end, an integrated absolute value interface and One Cable Technology (OCT).
Additional I/Os enable latching of position values. In addition, the integrated brake chopper control permits direct connection of braking resistors. The system also integrates programmable TwinSAFE Logic for direct implementation of the safety application in the terminal and safe drive technology either as STO/SS1 via Safety over EtherCAT (FSoE) or as a comprehensive package of Safe Motion functions for safety-relevant drive technology via TwinSAFE.
Five different ELM72xx models equipped with either STO/SS1 or Safe Motion are currently available:
- – ELM7211: 1-channel servo terminal with 4.5 A (Irms)
- – ELM7212: 2-channel servo terminal with 2 x 4.5 A (Irms)
- – ELM7221: 1-channel servo terminal with 8 A (Irms)
- – ELM7222: 2-channel servo terminal with 2 x 8 A (Irms)
- – ELM7231: 1-channel servo terminal with 16 A (Irms)
In contrast to the established EL series I/O terminals, the ELM72xx wiring level utilizes a pluggable design. Matching motor and sensor cables further simplify installation. The drive design – ELM72xx combined with AM8100 Servomotors – is implemented using the familiar TwinCAT 3 Motion Designer software (TE5910). The electronic nameplate and the TwinCAT 3 Drive Manager 2 software (TE5950) ensure efficient commissioning.
For more information, visit www.beckhoffautomation.com.