Traditional Factories Have Data Needs Too by Omron
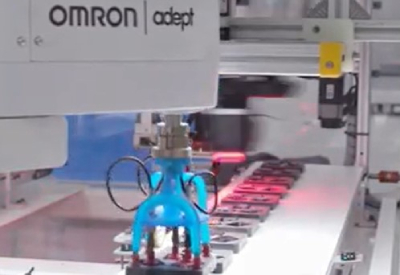
May 19, 2022
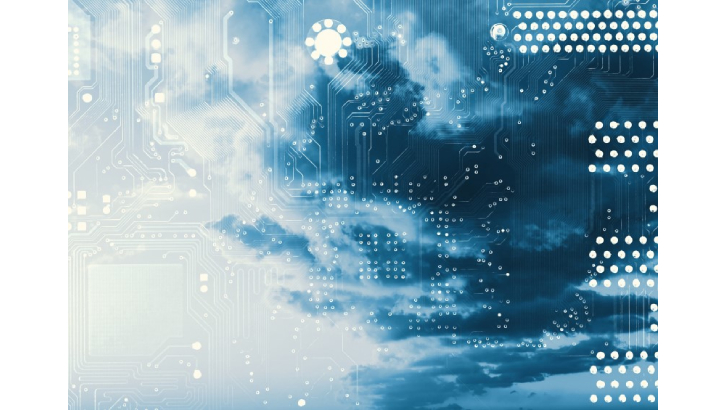
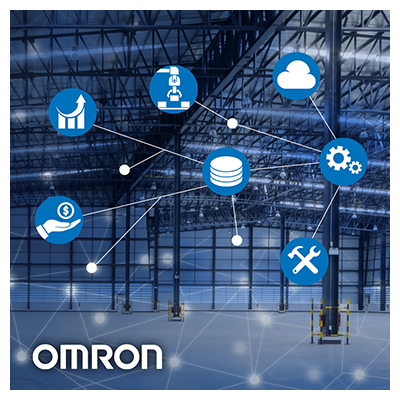
May 19, 2022
August 15, 2023 At Noark Electric, they manufacture top-quality low-voltage electrical components including circuit breakers for many applications. Circuit breakers are critical components commonly used in panelboards, switchboards, CDPs etc. for residential or commercial buildings, and industrial facilities, to protect against electrical damage caused by short circuits or overload conditions. By shutting off the flow of current upon…
“Innovative automation with a system.” For HandlingTech Automations-Systeme GmbH, the slogan says it all. Founded in 1994 as an automation newcomer in his parents’ basement turned parts business, Managing Director Jörg Hutzel’s family-owned company has developed into a veritable robotics player.
The introduction to SEW Eurodrive’s Innovation Lab was a big success. With Ontario reopening earlier this year, SEW Eurodrive has been excited to present their technology and automation solutions with customers, students, and the public again. Konrad Kurylo, P. Eng., was on site with other SEW Eurodrive experts to welcome an enthusiastic and engaged audience, who were eager to see what products and solutions SEW Eurodrive has to offer for Industry 4.0.
Schneider Electric, a major provider in digital transformation of energy management and automation, recently released a research report to foster an understanding of how digitized and smart applications will be powered in the future.
March 5, 2025 Modern manufacturing and logistics sectors demand increasingly efficient and reliable automation solutions, especially when it comes to handling delicate or irregularly shaped items. Available through Proax, SMC’s elite distributor, the ZGS Vacuum Gripper System (Foam Type) represents a significant advancement in this field, offering a comprehensive solution for palletizing and depalletizing applications, particularly…
ABB has been awarded a major contract by NatureWorks, the world’s leading manufacturer of polylactic acid (PLA), a low-carbon bioplastic made from renewable agricultural resources, to automate their new, greenfield plant in Thailand, converting sugar cane to the polylactic acid (PLA) biopolymer, Ingeo™.
July 18, 2025 By Krystie Johnston Humber Polytechnic is a technical institute located in the Greater Toronto Area of Ontario, and it has a long history of building brilliance and training the workforce of the future. In this article, Neal Mohammed, Director of the Barrett Centre for Innovation Technology shares his insights about Humber’s initiatives… Read More…
July 15, 2025 By Krystie Johnston In the U.S., California is the leading employer for electro-mechanical and mechatronics technicians. Training people to fill these roles domestically is critical for supply chain resilience. For the U.S. to compete globally, and bring manufacturing and innovation back to American soil, they need a skilled workforce that can operate… Read More…
In today’s fast-paced manufacturing and logistics industries, the need for efficient and flexible material movement solutions has never been greater. Traditional methods like conveyor systems, forklifts, and manual pushcarts have served us well, but they come with limitations.
That’s why Omron is thrilled to announce the launch of their game-changing MD Series of Autonomous Mobile Robots (AMRs). Read more
July 15, 2025 WAGO at your fingertips — scan the QR to get the app now. Stay connected with WAGO wherever you go. Download the WAGO App to access product details, documentation, configuration tools, as well as local distributors — all from your mobile device. Scan the QR code to get started on the App… Read More…
July 15, 2025 A new round of testing by Endress+Hauser of a multi-vendor Ethernet-APL setup has wrapped up successfully, further validating the technology’s readiness for widespread deployment. Ethernet-APL is becoming a must-have tool for advancing the digitalization of process plant operations for optimized performance and other major benefits. The recent load tests were tailored to… Read More…