Robot Simulation and Offline Programming Software: What You Need to Know
May 14, 2025
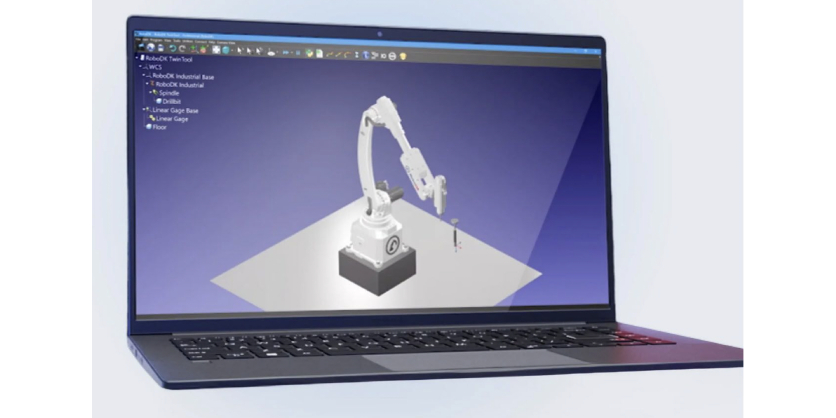
When integrating robotics into manufacturing or research environments, programming and optimizing robotic tasks quickly becomes a critical factor.
Traditionally, robot programming was done manually on the shop floor using a teach pendant—a time-consuming and error-prone process.
Today, advanced robot simulation and offline programming (OLP) software have transformed how engineers design, program, and deploy robotic systems.
This article explains the key types of software available for robotic simulation and offline programming, and how they support different automation goals.
Offline Programming (OLP) Software
Offline Programming Software allows engineers to create, simulate, and validate robot programs on a computer without taking the physical robot out of production. OLP software outputs code that can be uploaded directly into the robot controller.
Key benefits:
- Reduces downtime on production lines
- Shortens robot commissioning times
- Enables early troubleshooting and optimization
- Supports complex path generation based on CAD models
Examples: RoboDK, DELMIA Robotics, Octopuz
OLP is ideal for facilities that require frequent program changes, work with complex parts, or need to validate cell designs before building them physically.
Robot Simulation Software
Robot Simulation Software focuses on creating virtual models of robots and manufacturing cells to test movements, identify collisions, and optimize layouts. Some simulation software also includes basic programming capabilities but emphasizes visualization and design validation.
Key benefits:
- Verifies reachability, cycle time, and collision risks
- Optimizes workcell layouts and robot placement
- Supports virtual commissioning
- Aids in feasibility studies for new projects
Examples: RoboDK, Visual Components, Process Simulate
Simulation software is useful early in the project lifecycle for evaluating concepts and verifying that a robot can physically complete a task before investing in hardware.
CAD/CAM to Robot Software
CAD/CAM-to-Robot Software bridges traditional CAD/CAM workflows with robotic control. Instead of manually programming a robot for machining or additive manufacturing, CAD/CAM paths are automatically converted into robot motions.
Key benefits:
- Automates complex multi-axis path generation
- Reduces reliance on manual robot programming
- Enables robotic machining, 3D printing, and laser cutting
- Integrates easily with existing design workflows
Examples: RoboDK, SprutCAM Robot, Robotmaster
This type of software is best for applications like robotic milling, cutting, sanding, or any task where the robot follows a path derived from a CAD model.
Robot-Specific OEM Software
Many robot manufacturers provide proprietary software tailored to their robot models. These often offer simulation and limited offline programming but are locked to one brand.
Key benefits:
- Tight integration with the manufacturer’s hardware
- Simplified tools for basic applications
- Often bundled with the robot purchase
Examples:
- ABB RobotStudio
- FANUC ROBOGUIDE
- KUKA Sim Pro
While OEM software can be highly useful for brand-specific projects, it lacks cross-brand flexibility. Facilities working with multiple robot brands often prefer independent platforms like RoboDK.
Choosing the Right Software
Selecting the right tool depends on your project requirements:
Need | Recommended Software Type |
Reduce downtime during robot programming | Offline Programming Software |
Verify cell layouts and collision risks | Robot Simulation Software |
Automate toolpath generation from CAD models | CAD/CAM-to-Robot Software |
Program and simulate within a single robot brand | Robot-Specific OEM Software |
For most general-purpose applications requiring flexibility across brands and manufacturing tasks, RoboDK offers a robust and cost-effective solution that combines offline programming, simulation, and CAD/CAM integration in one platform.
Related Story
Electromate Certified as a Great Place to Work® Once Again
Electromate® is proud to announce that it has again been certified as a Great Place to Work® after a thorough, independent analysis conducted by the Great Place to Work Institute® Canada.
This certification is based on direct feedback from employees, as part of an extensive and anonymous survey about their workplace experience. The recognition highlights Electromate’s continued commitment to fostering a high-trust, high-performance culture built on transparency, respect, and collaboration.