Renishaw Central Demonstrates How the Digitalisation of End-to-End Manufacturing Processes Can Transform Operational Efficiency
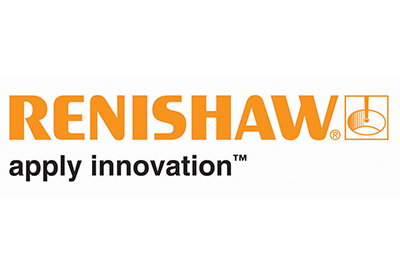
July 16, 2021
At EMO Milano 2021 (hall 5, stand C14), global engineering technologies company, Renishaw, is demonstrating its latest smart factory solutions to support the digitalisation and control of end-to-end manufacturing processes.
End-to-end process data capture is invaluable for the insight, analysis, and improvement of manufacturing processes. It allows manufacturers to predict, identify and correct process errors before they happen. Digitalisation of end-to-end manufacturing processes increases operational efficiency, reduces reliance on skills, improves ease of use and enhances decision making for process improvements.
Rapid progress in artificial intelligence (AI), robotics and the ‘Industrial Internet of Things’ (IIoT) has triggered an explosion in the pace of technological breakthroughs for the industrial sector. The integration of physical manufacturing processes with digital information technologies provides manufacturers with an opportunity to develop smarter processes for improved capability and productivity.
Trends promising to transform manufacturing industries include predictive analytics, AI and increased connectivity. The foundations for all these systems is data. Metrology data related to both processes and parts can be used to build controlled processes that enable manufacturers to take advantage of automation and boost throughput.
Visitors to EMO Milano 2021 can learn about Renishaw Central, Renishaw’s new manufacturing connectivity and data platform. Renishaw Central helps manufacturers to access the right data at the right time, enabling them to better understand production processes and improve process control and part quality. Renishaw manufacturing technologies enable intelligent manufacturing to automatically adjust and maintain control of CNC machining processes without the need for intervention by skilled personnel.
At the heart of the Renishaw Central manufacturing data platform are the themes of connectivity, and the ability to connect sensors on machines across the shop floor; consistency, through the monitoring of data from connected machines from a central location; and control, through the use of collected data to update CNC controls.
Renishaw Central collects and provides visibility of machining process data across the factory for insight at the point of manufacture, to analyse and health check the performance of devices on the shop floor, examine device utilisation and part quality, and to sign off and validate the part. Renishaw Central data is accessible, visual and supports in-process control applications and continuous improvement.
Renishaw Central supports end-to-end manufacturing processes, including additive manufacturing and the control of finishing and downstream processes. Visitors to the Renishaw stand at EMO Milano 2021 can see a demonstration of the additive manufacture and subsequent downstream machining of a tibial tray component, which is used in the manufacture of medical implants for knee replacements.
By providing a consistent method of connecting Renishaw measurement devices, Renishaw Central makes it easy for a variety of systems and processes to access and make use of device data. It will make Renishaw device data accessible and available to third-party platforms, which also support future Industry 4.0 technologies.
Guy Brown, Renishaw Central Development Manager, says: “We’re delighted to be supporting our global customers with their manufacturing ambitions by helping them to bring their factory of the future ever closer. By connecting process, machine and part data from across the process chain, including additive manufacturing systems, on-machine measurements, shopfloor gauging and co-ordinate measuring machines (CMMs), the Renishaw Central manufacturing connectivity and data platform provides a clear view of a manufacturing facility’s process and metrology data – and that’s powerful.”
A smart manufacturing system will allow manufacturers to identify and save production data, improve their quality systems and record details of any defects. When preparing for the future, manufacturers should be building a history of data in their own plants so that, should they decide to invest in automation technologies and AI, they have a body of intelligence from which to learn. These aspects will also provide manufacturers with data that they can leverage today for improved process control.
By standardising the flow of data to and from the modern, data-intensive shop floor, Renishaw Central can deliver a new level of operational efficiency.