Challenges and Strategies Shaping Traceability in Food and Beverage Packaging
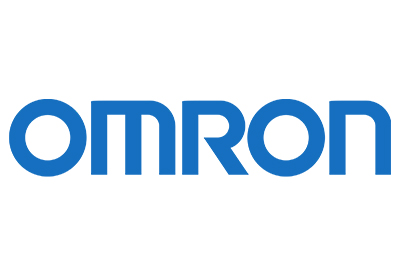
June 29, 2021
Authenticity is essential in the food and beverage packaging industry. Food allergies, as well as expired or contaminated foods, can cause serious illness and possibly death, so consumers need to know that the products they’re purchasing are safe. If manufacturers don’t guarantee the safety and authenticity of their products, their brand reputations will fall precipitously.
Since both public health and consumer satisfaction depend so heavily on product integrity, the entire industry is heavily regulated. One of the main things mandated by food and beverage regulation is traceability, the practice of maintaining thorough records on raw material origins and product status by scanning machine-readable codes throughout production.
Despite its importance and ubiquity, implementing traceability can be fraught with challenges. Let’s take a look at some of these challenges and explore ways to overcome them.
1. The challenge of inconsistencies in labeling
Whether applied by hand or by a robot, labels can sometimes contain errors or be applied to the wrong product. Food and beverage packaging must be extremely specific about what’s inside, and products with an information mismatch must be recalled immediately. As it so happens, labeling errors are the most common cause of food and beverage recalls.
One of the best ways to combat labeling mistakes is to implement an industry-standard label verification system. Print quality inspection systems perform a wide variety of verification-related tasks, including optical character recognition (OCR), optical character verification (OCV), master-to-label comparison and data and code matching.
These features help companies ensure accuracy and data integrity, identify defects, and avoid liability. Some printer-integrated systems can offer manufacturers 100% label inspection at print speeds of up to 254 mm (10 inches) per second.
2. The challenge of processing large amounts of data
The more data you can gather in your processes, the more opportunities you have to ensure quality. Today’s advanced traceability systems can even incorporate inspection data and machine data (such as temperature readings) and tie these data points together with a product ID and a timestamp.
Although having all this information on record is helpful, it can also slow down the system. Once traceability data is gathered via barcode readers or radiofrequency identification (RFID) reader/writers, it must be communicated to the rest of the system. As it turns out, processing large amounts of traceability data can slow the production cycle.
Fortunately, this need can be addressed with advanced control technology that can maintain high-speed control while handling all the data a traceability system provides. Some controllers can handle up to 1,000 products per minute and collect reams of data in synchronization with the production cycle while performing motion control.
3. The challenge of maintaining devices amid washdown conditions
Traceability systems include scores of barcode readers and smart cameras, while many food and beverage applications make use of frequent harsh washdowns to ensure consumer safety in meat/poultry and seafood processing, dairy, ice cream, frozen foods, fruits and vegetables, and other manufacturing and processing environments.
These washdowns can damage the delicate electronics inside code reading and vision technologies, potentially requiring costly replacements on a regular basis. Luckily, many automation solutions providers design technologies for maximum longevity amid washdown environments. Look for ratings like IP69K for washdown resistance and IP67G for oil resistance.
For every challenge that arises with traceability, there’s a solution that will help you maximize productivity while ensuring accuracy. The benefits of investing in traceability vastly outnumber the challenges, and a certain level of traceability is in fact mandated by law. Use the latest automation technologies to streamline your system and protect your brand.