Why Double-Ended Sensor Cables Make More Cents
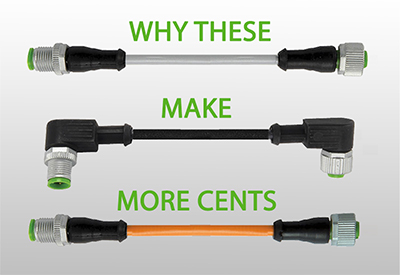
June 3, 2021
By Colin Cartwright, System Sales Manager, Murrelektronik Canada
Last month we looked at decoding all those M12 connectors from A to Y-Coded and narrowed things down to the four main types of M12 connectors you’re likely to run into on machines and assembly lines out there. For those who missed it, you can check it out here.
This month we are going to take a quick look at some of the benefits of using double-ended sensor cables instead of single-ended cables with field-attachable connectors. If you’re a controls manager or machine builder looking for some easy ways to increase your bottom line, this will be a worthwhile read.
Sensor cables have been available in double-ended connector versions with a variety of convenient lengths for some time now. However, there are still many machine builders and system integrators who continue to buy single-ended sensor cables with the intention of cutting them to length, then adding a field-attachable connector during installation. Now, I realise that there are times when this “cut and add a connector” approach to cable installation is the only option (i.e. an emergency repair, or a retrofit project where the cable lengths were impossible to determine in advance), but most of the time double-ended cables could quite easily be used with a little bit of planning and preparation. This is especially true on new machine builds.
So why aren’t more people buying double-ended sensor cables?
Based on the feedback I’ve received; it basically comes down to two factors: price and convenience. We will dig deeper into the price factor later in this article, so let’s tackle the convenience factor first. There are a couple of reasons why single-ended cables appear to be more convenient. For example, cable lengths do not need to be calculated ahead of time and they can look neater when cut to suit the application, or maybe standardizing on 5-meter female single-ended sensor cables and male field-attachable connectors makes inventory management easier. On the surface, these might make sense, but when you dig a little deeper, using single-ended sensor cables with field-attachable connectors might just be costing you some serious dollars and cents.
Let’s look at it from a slightly different angle:
Imagine if mechanical designers and millwrights standardized and stocked only 12” bolts, then cut these down to length to suit each application. If you’ve ever cut a bolt, then tried to thread it without first using a file to taper the end, you’ll understand why bolts are stocked in different lengths. It just takes too much time to cut bolts to length, and therefore doesn’t make any economical sense.
I think in most cases, it’s a similar scenario with sensor cables.
If we look at the cost of a single-ended sensor cable versus a double-ended sensor cable of the same length, it’s true that single-ended cables cost less. Single-ended cables also work well if you’re terminating the pigtail end directly to terminals, but as soon as you add a field-attachable connector that single-ended cable becomes much more expensive. Here is a quick comparison of costs using average Canadian prices that have been rounded to the nearest dollar.
Single-ended sensor cables are often bought in 5-meter lengths and the average cost of an M12 single-ended female sensor cable is about $9. The cost of an M12 male IDC field-attachable connector is around $10. That works out to be about $19 for the cable and connector. Now let’s factor in the cost for the labour required to connect the field-attachable connector.
Assuming it takes 5 minutes to connect a field-attachable connector (I’m being generous – they often take longer) and your net hourly labour cost is $50 per hour (I used a $25 per hour rate and factored in employer contribution costs for benefits, EI, CPP, etc.), it will cost you around $4.16 in labour to install the connector. When you add the labour cost to the material cost, you end up with a total cost of $23.16 per cable.
Now let’s compare that to a double-ended sensor cable.
The average cost of a 5-meter M12 double-ended cable is around $15, a 3-meter cable is around $12 and a 1.5-meter cable is $10. Depending on the length of cable you buy, a double-ended cable will save you around $8 to $13 per cable. That’s a lot of money!
Putting it another way: If you install a thousand sensor cables a year, you can make an extra $8k to $13k simply by switching to double-ended sensor cables!
If that’s not enough to convince you that double-ended sensor cables make more cents, something else to consider is the amount of troubleshooting time your commissioning team currently spends locating bad connections on sensor cables. Field-attachable connectors are notorious for causing connection problems if not installed properly. So, unless your team is extremely careful when connecting them (which increases that 5-minute installation time), you end up adding more unnecessary time to your sensor cable installations which ultimately adds even more to the cost of those single-ended cables. On the flipside, all double-ended sensor cables made by Murrelektronik are 100% tested before being packaged and shipped, so you won’t have any troubleshooting or debugging time at all.
Lastly, all that time consumed adding field-attachable connectors and troubleshooting bad connections could be time spent on other meaningful tasks that would help to decrease your overall installation time.
At the end of the day, there are some situations where the best option is a single-ended cable with a field-attachable connector, but most of the time, having a good selection of double-ended sensor cables of various lengths available can save you some serious time and money.
Murrelektronik stocks a wide variety of double-ended cables in different lengths so feel free to reach out to me or any of my Murrelektronik colleagues around the world if you would like to start making more cents.
For more information, visit www.murr.ca.