Five Automation Trends in Electronics Manufacturing
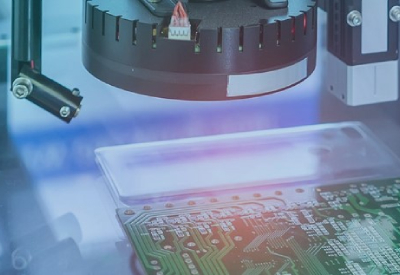
May 6, 2022
These days, we can’t build electronics quick enough. From the way our cars can sense their surroundings and the refrigerator that can order groceries when you run out to our ability to look up anything in the palm of our hand, electronics drive it all. Consumers and businesses alike want all of it—fast.
The pace at which we’re becoming comfortable and accustomed to powerful electronics in the everyday world has put extreme pressure on electronics manufacturers; resulting from the volume of demand and the expectations around continuously condensed and connected capabilities.
To accommodate these needs, electronics manufacturers have naturally turned to various forms of automation. Not only can they accelerate throughput, but automated systems also operate more precisely at millimeter scale and provide insightful data.
Here are five examples of how electronics manufacturers are taking advantage of automation in their facilities.
1. Internet of Things (IoT)
IoT is everywhere. It’s the idea that more than just a computer or smart phone can be connected to the internet. Examples include voice assistants, wearable fitness trackers, cars and many more. Electronics manufacturers are at the heart of making it all work, seamlessly integrating sensors, connectivity, and the web.
Many manufacturers also practice what they preach, using this technology to make themselves more efficient. Sensors are abundant in today’s electronics factories, from tool center points to motors and beyond.
This enhanced visibility provides all kinds of actionable data. One example of how this data is used is for predictive maintenance. The costs associated with maintenance and downtime are significant. The ability to monitor temperature, for example, can indicate how a component has worn or if it’s near the end of its lifecycle. It’s a simple example but knowing when to maintain and/or replace instead of educated guesswork can save time and money.
2. Decentralized Enterprise Resource Planning (ERP) Systems
Take the idea of predictable maintenance and multiply it again and again. That’s an ERP in essence. They’re nothing new, but with the sensors and communications that the IoT affords, ERPs can reach further into an operation to extract granular, real-time, and actionable data.
Where in the past, a single ERP may have handled several locations, today there are more organized tiers, and data can be analyzed in the cloud or your cell phone instead of in the back office. This can all but automate decisions that once required light coordination or discussion—everything from stocking inventory to workflows.
3. Artificial Intelligence (AI)
Both the data generated by all the inventory moving across a floor and the robotics performing thousands of repetitive tasks make for a manufacturing environment that’s rich in AI potential. Most electronics manufacturers fit that bill.
Any abnormalities, improvements or trends in performance can not only be identified, but specifically diagnosed. This level of adaptiveness can impact everything from improving product design processes and workflow to reducing defects.
4. Additive Manufacturing
Also known as 3D printing, additive manufacturing has made the once time-consuming and expensive prototyping phase much more efficient. Instead of machining tiny molds or delicate parts, these detailed pieces can be built into near-finished components.
Electrical engineers and designers can troubleshoot and test their products faster and with more certainty than ever. Additive has enabled innovative chip designs and chips that can’t be recreated with subtractive machining, including fabricating multiple components more efficiently as a single part.
5. Collaborative Robot Systems
No, the robots haven’t taken over. In fact, electronics manufacturers are finding great value in collaborative robot systems. These robots work alongside humans, typically handling repetitive tasks or moving a heavy component from one place to another. They may have a drill at one end or a gripper to pick and place.
Collaborative robots have gotten much easier to use and safer in recent years making them an attractive option in electronics fabrication. User interfaces have become more standardized, and the hardware is easier to integrate than ever. In the right manufacturing volume/mix environment, collaborative robot systems have proven a great way to fill in gaps and open up bottlenecks.
Ready to see what’s possible for your facility? Experience the latest in electronics and other manufacturing automation in person at the Automate show in Detroit, Michigan, USA from June 6-9. Register FREE today!