Rittal Presents its Wire Terminal WT C5 and C10
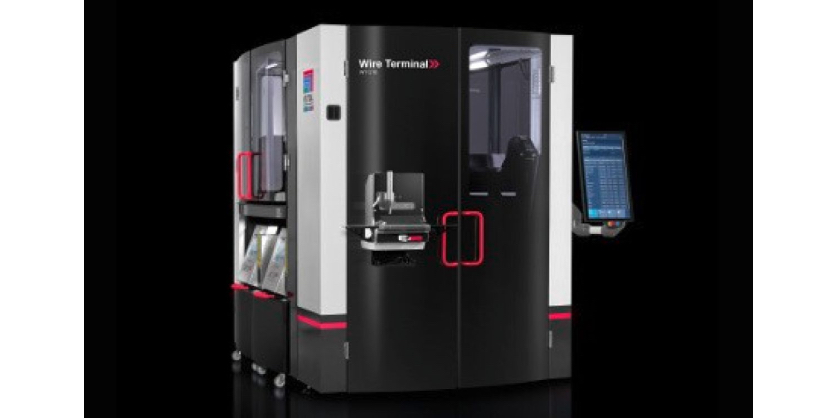
Innovations that allow wire processing at speeds ten times faster than by hand
Fully automatic wiring processing goes one stage further. Rittal presents its Wire Terminal WT C5 and C10 innovations that allow wire processing at speeds ten times faster than by hand.
Due to the modular system design and numerous option packages, panel builders and switchgear manufacturers now have a future-oriented automation solution. You can start with a small version and then adapt and expand it individually in terms of software and hardware as your needs grow. In addition, users are given a cross-process solution thanks to complete networking, ranging from electrical engineering to production.
Wiring in panel building and switchgear manufacturing are time-consuming elements, taking up around 50 per cent of the processing time. How can companies speed up their assembly and wiring processes while cutting costs and maintaining the same high quality? How can machine operation and production processes be made even simpler?
And how can plant constructors lay the foundations today for a technology that will still meet all their demands in another ten years or even longer?
Rittal has the answer with its new, fully automated wire processing machines: the Wire Terminal WT C5 and C10. They allow wires with individual wire printing (black, white and light blue) and picking to be assembled ten times faster than by hand. But there’s more: The core advantages are the variety of combinations, the different wire output methods and the support for downstream, digitally consistent and automated processes such as labelling, sorting and transport.
The technical basis for the multi-talent is an individually adaptable and expandable modular system structure in terms of both hardware and software, depending on the needs. This wire terminal puts users in an ideal position to meet future requirements. Moreover, the payback period is only 2.5 years for 300 enclosures per year.
Flexible configuration stages for Wire Terminal
The Wire Terminal WT is available in two different versions and flexible configuration stages. As an entry-level wire processing solution, Rittal offers the WT C5 variant with five vibratory bowl feeders for wire-end ferrules and a wire-end treatment feature for wires with cross-sections ranging from 0.5 to 2.5 mm². The product also cuts to length, labels and crimps. The WT C10 variant has ten vibratory bowl feeders for wire-end ferrules with wire cross-sections of up to 6 mm² as default. Both variants allow further expansion to full functionality in the respective wire application.
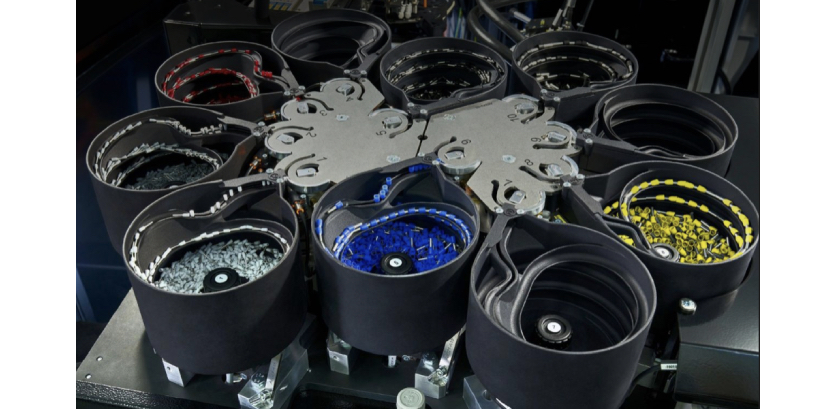
Quick-change system for wires
The fully automated machine, easily operated via a 24″ display, offers many improvements and innovations, such as when feeding and outputting the wires. Safe wire feeding and a simple, fast changeover to other wires are achieved via a new type of wire feeding system featuring three feed blocks for as many as 36 wires and with 12 wire types per feed block. The quick-change system allows the feed blocks to be set up and changed flexibly. An RFID transponder automatically secures the wire feed. This makes it easy to change complete wire magazines.
The highest quality of process reliability
With up to ten vibratory bowl feeders for the process-safe input of loose wire end ferrules and thanks to the easy way it can be refilled, the wire terminal WT C10 offers maximum flexibility and less set-up effort for the wire end treatment. The use of a new-technology crimper permits the processing of wire end ferrule lengths ranging from 8 to 18 mm. You can choose between stepless partial and full stripping up to 20 mm when stripping the wires. This new crimper, which uses servomotor technology, ensures continuous very high quality.
Three wire output methods
Depending on the requirements, the wires can be dispensed in a machine in three different ways: through ejection, by a rail system or via a chain bundler. The patented rail system can hold up to 2100 wires. Wire sorting is unnecessary, as the pre-assembled wires are produced in wire rails as standard, depending on the order. This enables the lined-up wires to be processed quickly and efficiently, which, in conjunction with the Wire Cart trolley, is ideal for improved order picking at the workplace.
Chain bundles can also be produced to make the wiring process even more efficient: Wires are arranged sequentially in the order chosen. This also allows companies to act flexibly as service providers. In a Wire Terminal, the three flexible output options can be implemented. Combined with the “Eplan Smart Wiring” software app, this leads to effective value creation in the additional process step of enclosure wiring.
A digitally supported process chain
Besides the labelling, sorting and transport options, Rittal also supports downstream processes with consistent data. Furthermore, the new software architecture ensures seamless integration into the RiPanel Processing Center job management software’s data workflow. This means more efficient production, not only due to the higher working speed. Consequently, production becomes an even stronger part of the entire digitally supported process chain, centrally planned and controlled with data directly from the Eplan and Rittal engineering and manufacturing ecosystem.
More Information
Related Story
It’s official! Rittal Limited is a Great Place to Work® and the Recipient of the Rittal Global Oscar Business Performance Award
Rittal Limited, Canada, is proud to announce that we have been certified as a Great Place to Work® after a thorough, independent analysis conducted by Great Place to Work Institute® Canada. This certification is based on direct feedback from employees, provided as part of an extensive and anonymous survey about their workplace experience.