KONTEC KSX-E: 100 Percent Electric!
February 26, 2025
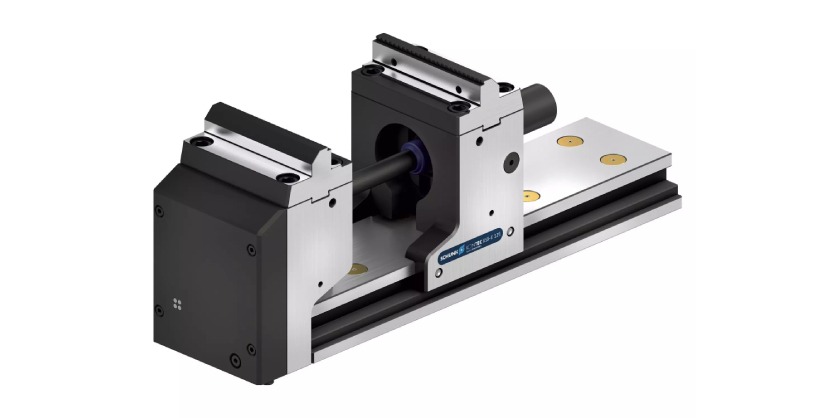
With the KONTEC KSX-E, SCHUNK is launching the first 100 percent electrically driven 5-axis vise with infinitely programmable clamping stroke – another future-ready component for the digitalized and energy-efficient production.
Digital technologies create more energy-saving, efficient and flexible manufacturing processes. They are key components for a “Healthy Factory,” a production facility that is both healthy and economically successful. With this goal in mind, SCHUNK is also making its clamping devices increasingly parameterizable and networkable. The advantages are particularly evident in the machining of small and medium batch sizes and in transparent process monitoring. For this purpose, SCHUNK has added an electrically driven version with a freely programmable clamping stroke to its proven KSX series of 5-axis vises – the KONTEC KSX-E.
Digitalized process monitoring
The new KONTEC KSX-E with 24 Volt DC is controlled via spring contacts at the bottom or a side-mounted wired connector. All programmable parameters such as clamping force, clamping stroke or jaw position can be controlled at the same time and can be transferred and evaluated via the integrated IO-Link interface to the machine control unit. An IO-Link is a fieldbus-independent point-to-point connection, in which the clamping device can be integrated into the corresponding fieldbus system via an IO-Link master. In the future, it should be possible to transfer and set the data via wireless communication or cable to an app.
Optimal 5-sided accessibility
A large clamping range of up to 420 mm and the pre-positioning of the jaws make the KONTEC KSX-E particularly flexible for automated machine tending with a high part variation. Thanks to its geometry with very high jaws, the vise provides optimal accessibility for 5-sided complete machining on 5-axis machines. The upper-lying spindle makes sure that the clamping force is applied directly below the workpiece and thus prevents the jaws from lifting up.
Moreover, the continuously programmable clamping force of up to 40 kN per jaw ensures that the workpiece can also be clamped process-reliably and vibration-safe even with minimal clamping surfaces. The vise also works reliably under the influence of chips, dirt, or coolant. Its complete sealing and encapsulation, electronics and actuators are also well protected.
The comprehensive range of SCHUNK system and top jaws rounds off the complete package of KONTEC KSX-E. Suitable jaws are easy to find via the digital SCHUNK chuck jaw quickfinder. SCHUNK will offer the KONTEC KSX-E in size 125 from the first quarter of 2025 on.
Related Story
HERMES AWARD 2024 Goes to SCHUNK
German company SCHUNK was honored with the HERMES AWARD at the ceremonial opening of HANNOVER MESSE on April 21, 2024, in recognition of an innovative AI-based project. Bettina Stark-Watzinger, Germany’s Minister of Education and Research, presented the award in the presence of Federal Chancellor Olaf Scholz and Norwegian Prime Minister Jonas Gahr Støre.