Nidec Machine Tool Launches MV12BxⅡ
A Compact, Best-In-Class, Double-Column Machining Center that Meets “The Machining Needs of All Industries”
February 6, 2023
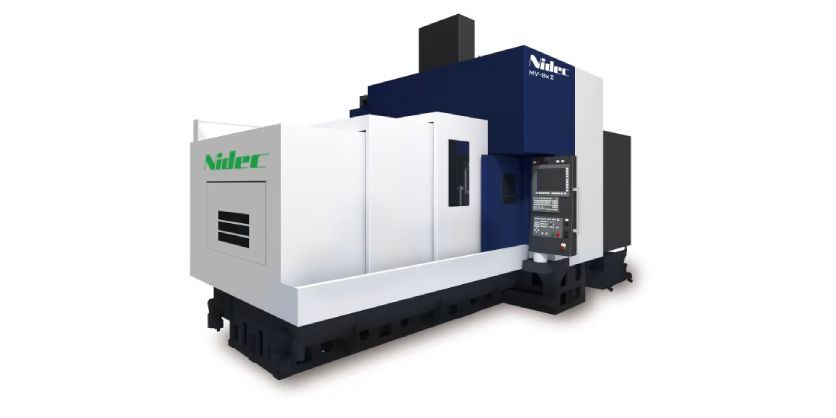
Nidec Machine Tool’s double-column Machining Center, MV12BxⅡ
- High-speed rapid traverse and a powerful spindle to improve productivity significantly
- Eco-friendly operations that reduce environmental load and running cost
Nidec Machine Tool Corporation, a Nidec Group company, announced that it has launched its latest double-column machining center, MV12BxⅡ. Developed based on the concept of meeting “the machining needs of all industries,” this high-efficiency machine brings the best-in-class speed of a rapid traverse that significantly reduces non-cutting time, while achieving the highest productivity among all compact double-column machining centers.
In addition MV12BxⅡ uses grease to lubricate all of its spindle and feed axes to improve energy efficiency and running cost, as well as featuring an electric power unit that enables ecofriendly operations. Offered as a machine that meets a diverse range of production requirements, such as high-precision surface quality to general parts machining, including light cutting to heavy cutting.
MV12BxⅡ will be unveiled to the public at Nidec Machine Tool’s Large-Machine Preview scheduled on Tuesday, February 21 and Wednesday, February 22 at its Main Plant in Ritto, Shiga, Japan.
With the high-speed of the rapid traverse (Ⅹaxis: 48m/min., and Y- & Zaxes: 32m/min.), MV12BxⅡ realizes shorter non-cutting time, while its spindle’s maximum rotating speed has been improved to 7,000min-1, and its motor output has been increased to 26kW. Further, with a compact machine-installation space of 3.4 x 5.8m and a maximized range of operation (X-axis stroke: 1.6m, and Y-axis stroke: 1.3m), MV12BxⅡ’s productivity is second to none among double-column machining centers with a BT50 taper spindle in this class.
With the use of an energy-efficient and low-noise electric power unit to operate its pump only when necessary, MV12BxⅡ consumes much less power than conventional hydraulic units that are always running. In addition, the adoption of the tribology technology that Nidec Machine Tool has long developed and perfected, it enables the use of grease to lubricate MV12BxⅡ’s spindle and feeding axes, helping the machine to use less air and lubricant agent, to reduce running cost and operators’ workload.
Additionally, MV12BxⅡ has available a variety of user-satisfying options that were jointly developed with Nidec OKK Corporation, whose product lineup includes small- and medium-sized machining centers. The options include an automatic operator door, a coolant shower, and a selectable chip conveyor, is enough to meet various user needs.
Nidec Machine Tool stays committed to developing technologies for optimum productivity, safety, and environmental performance, and offering products that meet the diverse needs of production sites around the world.
MV12BxⅡ’s main specifications:
Section/model | MV12BxⅡ | ||
Distance between columns (mm) | 1,460 | ||
Table | Table work surface | Width (mm) | 1,300 |
Length (mm) | 1,600 | ||
Loading capacity (kg) | 3,000 | ||
Distance from table surface to spindle nose (mm) | 200-860 | ||
Axis travel (mm) | X | 1,600 | |
Y | 1,300 | ||
Z | 660 | ||
Rapid traverse (m/min) | X | 48 | |
Y | 32 | ||
Z | 32 | ||
Cutting feed X, Y and Z axes (m/min) | 10 | ||
Spindle | Speed (min-1) | 7,000 | |
Motor output (kW) | 26 | ||
Taper | BT50 | ||
ATC tools (quantity) | 30 |
For inquiries on the above product, please contact Sales Division of Nidec Machine Tool Corporation at +81-77-552-9760
Related Product
Nidec Machine Tool Launches MVR-Aⅹ, a New Series of Double-column Machining Centers
Nidec Machine Tool Corporation (led by Kenichi Wakabayashi, president, and headquartered in the city of Ritto, Shiga Prefecture) announced recently that it has launched MVR-Ax, the series of the company’s new models of double-column machining centers, on the same day. These new products were developed as easy-to-use machines to meet the diverse needs of manufacturing sites that machine large-size components.
Nidec Machine Tool stays committed to offering machine tools that are needed in all industries to contribute to improving their customers’ manufacturing capabilities.