Why Authorized Employee Training Is Important
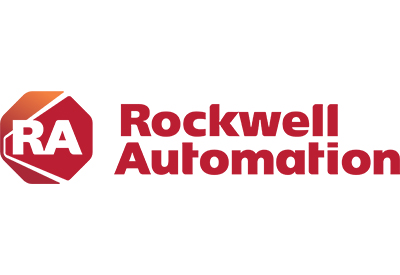
August 20, 2021
By Jake Thatcher, Senior Safety Project Engineer, Rockwell Automation
Authorized employee training is one of the most important aspects of a complete energy control program. Training delivers the knowledge that employees need to effectively lock out equipment for servicing or maintenance. This type of training should include the use of energy control procedures as well as lockout locks, tags and devices.
Training Prepares Employees to Do Their Job Efficiently
The purpose of authorized employee training is to verify that the employees understand the purpose and function of the energy control program and that they also have the knowledge and skills required to use the program properly and safely. Employers are required to provide the training to the authorized employees prior to a lockout ever being administered.
Anyone Who Services Equipment Must be Trained as an Authorized Employee
By OSHA standards, an authorized employee is defined as any employee who services or maintains equipment and needs to perform lockout/tagout. Authorized employees are required to be trained in the recognition of energy sources – for example, electrical, pneumatic, water, gas, steam – and the types of magnitudes that are present in the corresponding facility. They will also need to be trained on how to isolate and control the energy correctly on different equipment.
These employees must know how to test the equipment to verify that all energy has been properly controlled prior to working on the unit. For example, a new employee could likely lock out a pump without issue, but there would be a greater risk if they were tasked with shutting down a boiler since they wouldn’t understand how to do this without the proper training, and there is a greater risk of a boiler imploding unless the proper steps are taken to shut it down before servicing.
Understanding the Value of Exclusive Control (Locks) and the Limitations of Warning Tags is Essential
What happens when an energy source does not have a means to have a lock applied? Employees must be trained on the limitation of tags. Tags are simply warning devices that do not provide a physical restraint to the energy sources themselves. The authorized employees also need to be instructed not to remove or bypass any tags, and that the authorized employee who installed the tag is the only employee who is permitted to remove it. In addition, the authorized employees must be trained on when to use the tagout system, and what information is required to be included on the tag.
Monitoring and Review for Safety Employee Success is an Annual Job
Additionally, employees may need to be retrained after their initial training. The need for retraining will be determined during the annual review that is required by the OSHA standard 1910.147. If any deficiencies are found during the annual review of the employees, retraining is required for those workers who did not pass the annual review. Also, authorized employees must be retrained if there is a change in the energy control procedures at the site, or the employee’s job description.
Final Tips for Lockout/Tagout Program Success
For successful energy control program training, it is important to deliver training that is understandable and relatable to the facility itself. For example, workers at a pharmaceutical plant would need to know how reverse osmosis systems work, but at a paper mill there is no need. Food manufacturing sites that use ammonia cooling systems for large cooling warehouses or walk-in freezers would need special training for authorized employees working on equipment like ammonia compressors.
The safety of employees will increase greatly when you have an effective authorized employee training program in place. Be sure to include all necessary information that OSHA requires, as well as any other additional information specific to the site.
If you would like help with creating or delivering your authorized employee training, Rockwell Automation has lockout/tagout specialists who have helped hundreds of companies reach compliance with their lockout/tagout programs.