The Benefits of Effector Offsets: The Invisible Tech that Delivers Real Results
November 2, 2022
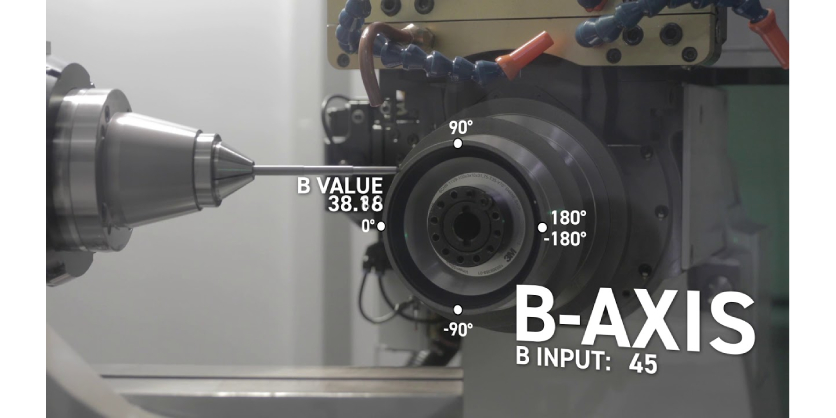
By Lucas Hale, Global Marketing Manager
An important part of being a leader in CNC machine technology is striving for innovation. Whether it’s by exploring ways to evolve the mechanics of the machine, or by creating revolutionary new software for it, innovation has been central to ANCA’s 45-year history.
The use of software control in cutting tool manufacture has made the process easier and more precise. And we continue to look for ways to improve our machines.
Two huge benefits of software control are effector offsets and ANCA’s patented soft axes system. Let’s review them both.
The effector offsets effect
So, let’s start with what an effector is. The term comes from robotics, where an end effector is the device at the end of a robotic arm, designed to interact with the environment. What that device is depends on what the robot is built to do. These could be jaws to grip something, needles to penetrate something, a vacuum to hold something, and so on.
In CNC machining, we’ve adopted this term to refer to the cutting wheels on the machine. And, as you know, cutting wheels come in different sizes. So, when programming the movement of the spindle along a tool, we need to take into account the size and length of the cutting wheel.
An effector offset is a point in space a distance away from the spindle center to the grind point on the edge of the wheel that actually does the cutting. The machine needs to recognize what the diameter and length of the cutting tool is and compensate for that when following its programmed path. This is all handled by the ANCA software, so there’s no complicated maths required of the operator.
Another advantage for the operator is that the position display of the machine also uses this effector point, so the programmed position and the actual position are in the same reference frame. This ‘what you see is what you get’ approach makes for much easier operation.
All you really need to know is that it’s all being taken care of by the control system to ensure you’re cutting the tool where you want to cut it.
The invention of soft axes
The introduction of soft axes is a truly revolutionary development in CNC machine technology. Soft axes refer to software axes that make it much easier to program complex axis combinations.
ANCA CNC machines are unique in offering nine axes capability. The five physical axes are the X-Axis, which is parallel to the tool movement, the Y-Axis, which is horizontal to the tool movement, the Z-Axis, which is vertical, the A-Axis, which rotates the tool clockwise and anticlockwise, and the C-Axis, which rotates the wheel pack clockwise and anticlockwise.
Then there are the four soft axes. The B-Axis movement is always around the edge of the wheel. The B input value is entered in degrees—a positive value moves it clockwise around the wheel, while a negative value moves it anticlockwise. The U-Axis movement is always radially towards the center of the wheel. The V-Axis movement is perpendicular to the front surface of the wheel. And the W-Axis movement is tangential to the edge of the wheel.
This greatly reduces the number of calculations required when moving from point to point between the tool and wheel. By simply inputting the soft axis B value, the ANCA software will calculate all the spline points itself and automatically perform the necessary moves.
The addition of these extra soft axes offers quite a few benefits. For a start, it makes it much easier to design significantly more complex parts, optimized for performance. The ability to better control the speed of the movement along the path can result in a more uniform surface finish. And the quality of the parts produced is increased. What formerly required multiple setups can be achieved in one, reducing the chance of any errors.
ANCA holds a patent on the soft axes system technology. It provides operators using our machines far greater flexibility and broadens the capability of what they’re able to produce.
And there’s nothing soft about that.